ADXL105JQC Analog Devices Inc, ADXL105JQC Datasheet - Page 8
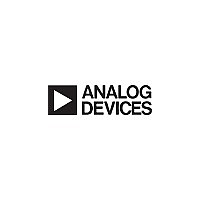
ADXL105JQC
Manufacturer Part Number
ADXL105JQC
Description
IC ACCELEROMETER SGL 14CERPAK
Manufacturer
Analog Devices Inc
Series
iMEMS®r
Datasheet
1.ADXL105AQC.pdf
(8 pages)
Specifications of ADXL105JQC
Rohs Status
RoHS non-compliant
Axis
X, Z
Acceleration Range
±7g
Sensitivity
250mV/g
Voltage - Supply
2.7 V ~ 5.25 V
Output Type
Analog
Bandwidth
12kHz
Mounting Type
Surface Mount
Package / Case
14-CerPak
Interface
-
Available stocks
Company
Part Number
Manufacturer
Quantity
Price
Company:
Part Number:
ADXL105JQC
Manufacturer:
BETRONIC
Quantity:
228
Company:
Part Number:
ADXL105JQC
Manufacturer:
AD
Quantity:
2 197
Part Number:
ADXL105JQC
Manufacturer:
ADI/亚德诺
Quantity:
20 000
ADXL105
Dynamic Operation
In applications where only dynamic accelerations (vibration) are
of interest, it is often best to ac-couple the accelerometer output
as shown in Figures 15c and 15d. The advantage of ac coupling
is that 0g offset variability (part to part) and drifts are eliminated.
Low Power Operation
The most straightforward method of lowering the ADXL105’s
power consumption is to minimize its supply voltage. By lower-
ing V
9.5 mW to 3.5 mW. There may be reasons why lowering the
supply voltage is impractical in many applications, in which case
the best way to minimize power consumption is by power cycling.
The ADXL105 is capable of turning on and giving an accurate
reading within 700 s (see Figure 18). Most microcontrollers
can perform an A-to-D conversion in under 25 s. So it is prac-
tical to turn on the ADXL105 and take a reading in under 750
2.7 V would be:
Note that if a filter is used in the UCA, sufficient time must be
allowed for the settling of the filter as well.
Broadband Operation
The ADXL105 has a number of characteristics that permits
operation over a wide frequency range. Its frequency and phase
response is essentially flat from dc to 10 kHz (see Figures 12
and 13). Its sensitivity is also constant over temperature (see
Figure 3). In contrast, most accelerometers do not have linear
response at low frequencies (in many cases, no response at very
low frequencies or dc), and often have a large sensitivity tem-
perature coefficient that must be compensated for. In addi-
tion, the ADXL105’s noise floor is essentially flat from dc to
+V
s. Given a 100 Hz sample rate the average current required at
0.22 F
50
Figure 18. Typical Turn-On Response at V
DD
T
from 5 V to 2.7 V the power consumption goes from
OUT
ST
100 samples/s
COM
Figure 17. Reducing Noise on V
COM
X SENSOR
SENSOR
TEMP
V
DD
A
V
OUT
DD
ADXL105
750 s
V
MID
V
NIN
UNCOMMITTED
V
IN
AMPLIFIER
1.3 mA = 97.5 A
UCA
OUT
DD
A-TO-D
CONVERTER
COM
VREF
AIN
DD
= 5 V
DOUT
–8–
5 kHz where it gently rolls off (see Figure 7). The beam reso-
nance at 16 kHz can be seen in Figure 7 where there is a small
noise peak (+5 dB) at the beam’s resonant frequency. There are
no other significant noise peaks at any frequency.
The resonant frequency of the beam in the ADXL105 deter-
mines its high frequency limit. However the resonant frequency
of the Cerpak package is typically around 7 kHz. As a result, it
is not unusual to see 6 dB peaks occurring at the package reso-
nant frequency (as shown in Figures 12 and 13). Indeed, the
PCB will often have one or more resonant peaks well below
7 kHz. Therefore, if the application calls for accurate operation
at or above 6 kHz the ADXL105 should be glued to the PCB in
order to eliminate the amplitude response peak due to the pack-
age, and careful consideration should be given to the PCB
mechanical design.
CALIBRATING THE ADXL105
The initial value of the offset and scale factor for the ADXL105
will require dc calibration for applications such as tilt
measurement.
For low g applications, the force of gravity is the most stable,
accurate and convenient acceleration reference available. An
approximate reading of the 0 g point can be determined by
orienting the device parallel to the Earth’s surface and then
reading the output. For high accuracy, a calibrated fixture must
be used to ensure exact 90 degree orientation to the 1 g gravity
signal.
An accurate sensitivity calibration method is to make a measure-
ment at +1 g and –1 g. The sensitivity can be determined by the
two measurements. This method has the advantage of being less
sensitive to the alignment of the accelerometer because the on
axis signal is proportional to the Cosine of the angle. For ex-
ample, a 5 error in the orientation results in only a 0.4% error
in the measurement.
To calibrate, the accelerometer measurement axis is pointed
directly at the Earth. The 1 g reading is saved and the sensor is
turned 180 to measure –1 g. Using the two readings and sensi-
tivity is calculated:
0.170 (4.318)
0.135 (3.429)
0.020 (0.508)
0.004 (0.102)
0.310 (7.874)
0.275 (6.985)
Sensitivity = [1 g Reading – (–1 g Reading)]/2 V/g
PIN 1
0.050
(1.27)
BSC
Dimensions shown in inches and (mm).
14
0.415 (10.541)
1
0.300 (7.62)
OUTLINE DIMENSIONS
MAX
0.020 (0.508)
0.013 (0.330)
14-Lead Cerpak
8
7
0.419 (10.643)
0.394 (10.008)
(QC-14)
0.190 (4.826)
0.140 (3.556)
SEATING
PLANE
0.0125 (0.318)
0.009 (0.229)
0.345 (8.763)
0.290 (7.366)
0.050 (1.270)
0.016 (0.406)
REV. A
8
0