AD22105AR-REEL Analog Devices Inc, AD22105AR-REEL Datasheet - Page 7
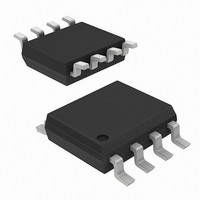
AD22105AR-REEL
Manufacturer Part Number
AD22105AR-REEL
Description
IC TEMP SENSOR/SWITCH LV 8SOIC
Manufacturer
Analog Devices Inc
Datasheet
1.AD22105ARZ.pdf
(8 pages)
Specifications of AD22105AR-REEL
Rohs Status
RoHS non-compliant
Sensing Temperature
-40°C ~ 150°C
Output Type
Open Collector
Voltage - Supply
2.7 V ~ 7 V
Accuracy
±0.5°C
Package / Case
8-SOIC (0.154", 3.90mm Width)
Available stocks
Company
Part Number
Manufacturer
Quantity
Price
Company:
Part Number:
AD22105AR-REEL
Manufacturer:
MIT
Quantity:
358
Part Number:
AD22105AR-REEL
Manufacturer:
ADI/亚德诺
Quantity:
20 000
REV. 0
OUTPUT SECTION
The output of the AD22105 is the collector of an NPN transistor.
When the ambient temperature of the device exceeds the
programmed setpoint temperature, this transistor is activated
causing its collector to become a low impedance. A pull-up
resistor, such as the internal 200 k provided, is needed to
observe a change in the output voltage. For versatility, the
optional pull-up resistor has not been permanently connected
to the output pin. Instead, this resistor is undedicated and
connects from Pin 7 (V
R
(R
The 200 k pull-up resistor can drive CMOS loads since
essentially no static current is required at these inputs. When
driving “LS” and other bipolar family logic inputs a parallel
resistor may be necessary to supply the 20 A–50 A I
Level Input Current) specified for such devices. To determine
the current required, the appropriate manufacturer’s data sheet
should be consulted. When the output is switched, indicating an
over temperature condition, the output is capable of pulling
down with 10 mA at a voltage of about 375 mV. This allows for
a fan out of 2 with standard bipolar logic and 20 with “LS”
family logic.
Low power indicator LEDs (up to 10 mA) can be driven
directly from the output pin of the AD22105. In most cases a
small series resistor (usually of several hundred ohms) will be
required to limit the current to the LED and the output
transistor of the AD22105.
MOUNTING CONSIDERATIONS
If the AD22105 is thermally attached and properly protected, it
can be used in any measuring situation where the maximum
range of temperatures encountered is between –40 C and
+150 C. Because plastic IC packaging technology is employed,
excessive mechanical stress must be avoided when fastening the
device with a clamp or screw-on heat tab. Thermally conductive
epoxy or glue is recommended for typical mounting conditions.
In wet or corrosive environments, an electrically isolated metal
or ceramic well should be used to protect the AD22105.
THERMAL ENVIRONMENT EFFECTS
The thermal environment in which the AD22105 is used
determines two performance traits: the effect of self-heating on
accuracy and the response time of the sensor to rapid changes in
temperature. In the first case, a rise in the IC junction tempera-
ture above the ambient temperature is a function of two variables:
the power consumption of the AD22105 and the thermal
resistance between the chip and the ambient environment,
Self-heating error can be derived by multiplying the power
dissipation by
surroundings with different heat sinking capacities, it is
necessary to specify
how the magnitude of self-heating error varies relative to the
environment. A typical part will dissipate about 230 W at
room temperature with a 3.3 V supply and negligible output
loading. In still air, without a “heat sink,” Table I indicates a
Thermal rise of the die will be considerably less in an environ-
ment of turbulent or constant moving air or if the device is in
direct physical contact with a solid (or liquid) body.
JA
PULL-UP
PULL-UP
of 190 C/W, which yields a temperature rise of 0.04 C.
) to Pin 2 (OUT).
a single connection should be made from Pin 1
JA.
Because errors of this type can vary widely for
JA
S
under several conditions. Table I shows
) to Pin 1 (R
PULL-UP
). In order to use
IH
(High
JA
.
–7–
Response of the AD22105 internal die temperature to abrupt
changes in ambient temperatures can be modeled by a single
time constant exponential function. Figure 11 shows typical
response plots for moving and still air. The time constant,
(time to reach 63.2% of the final value), is dependent on
the thermal capacities of the chip and the package. Table I lists
the effective for moving and still air. Copper printed circuit
board connections were neglected in the analysis; however, they
will sink or conduct heat directly through the AD22105’s solder
plated copper leads. When faster response is required, a therm-
ally conductive grease or glue between the AD22105 and the
surface temperature being measured should be used.
Medium
Moving Air**
Without Heat Sink
Still Air
Without Heat Sink
NOTES
**The time constant is defined as the time to reach 63.2% of the final tempera-
**1200 CFM.
USING THE AD22105 AS A COOLING SETPOINT
DETECTOR
The AD22105 can be used to detect transitions from higher
temperatures to lower temperatures by programming the
setpoint temperature 4 C greater than the desired trip point
temperature. The 4 C is necessary to compensate for the
nominal hysteresis value designed into the device. A more
precise value of the hysteresis can be obtained from Figure 6. In
this mode, the logic state of the output will indicate a HIGH for
under temperature conditions. The total device error will be
slightly greater than the specification value due to uncertainty in
hysteresis.
APPLICATION HINTS
EMI Suppression
Noisy environments may couple electromagnetic energy into the
R
sources, which typically come from fast rising edges, can be
coupled into the device capacitively. Furthermore, if the output
signal is brought close the R
OUT pin to the R
capacitance can come from several places such as, IC sockets,
multiconductor cables, and printed circuit board traces. In some
cases, it can be corrected by constructing a Faraday shield
around the R
the shield grounded. However, for best performance, cables
should be avoided and the AD22105 should be soldered directly
to a printed circuit board whenever possible. Figure 13 shows a
sample printed circuit board layout with low inter-pin capaci-
tance and Faraday shielding. If stray capacitance is unavoidable,
and interference or oscillation occurs, a low impedance capaci-
tor should be connected from the R
This capacitor must be considerably larger than the estimated
stray capacitance. Typically several hundred picofarads will cor-
rect the problem.
SET
ture change.
node causing the AD22105 to falsely trip or untrip. Noise
SET
Table I. Thermal Resistance (SO-8)
pin, for example, by using a shielded cable with
SET
pin potentially causing oscillation. Stray
SET
100
190
JA
pin, energy can couple from the
( C/Watt)
SET
pin to the GND pin.
AD22105
3.5
15
(sec)*
JA
and