AD9100SE/883B Analog Devices Inc, AD9100SE/883B Datasheet - Page 6
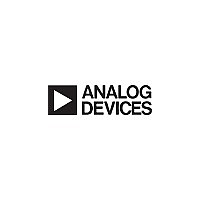
AD9100SE/883B
Manufacturer Part Number
AD9100SE/883B
Description
Manufacturer
Analog Devices Inc
Datasheet
1.AD9100SE883B.pdf
(12 pages)
Specifications of AD9100SE/883B
Lead Free Status / RoHS Status
Supplier Unconfirmed
Available stocks
Company
Part Number
Manufacturer
Quantity
Price
AD9100
The exaggerated illustration in Figure 1 shows that V
settled to within x% of its final value, but V
limitations, finite BW, power supply ringing, etc.) has not
settled during the track time. However, since the output buffer
always “tracks” the front end circuitry, it “catches up” during
the hold time and directly superimposes itself (less about 600 ps
of analog delay) to V
the output buffer is about 1.8 ns to 1 mV and is significantly
less than the specified hold time, acquisition time should be
referenced to the hold capacitor.
Note that most of the hold settling time and output acquisition
time are due to the input buffer and the switch network. For
track time, the output buffer contributes only about 5 ns of the
total; in hold mode, it contributes only 1.8 ns (as stated above).
A stricter definition of acquisition time would total the acquisi-
tion and hold times to a defined accuracy. To obtain 12 bit +
distortion levels and 30 MSPS operation, the recommended
track and hold times are 20 ns and 13.5 ns, respectively. To
drive an 8-bit flash converter with a 2 V p-p full-scale input,
hold time to 1 LSB accuracy will be limited primarily by the
encoder, rather than by the AD9100. This makes it possible to
reduce track time to approximately 13 ns, with hold time chosen
to optimize the encoder’s performance.
Hold vs. Track Mode Distortion
In many traditional high speed, open loop track-and-holds,
track mode distortion is often much better than hold mode dis-
tortion. Track mode distortion does not include nonlinearities
due to the switch network, and does not correlate to the relevant
hold mode distortion. But since hold mode distortion has tradi-
tionally been omitted from manufacturer’s specification tables,
users have had to discover for themselves the effective overall
hold mode distortion of the combined T/H and encoder.
The architecture of the AD9100 minimizes hold mode distortion
over its specified frequency range. As an example, in track mode
the worst harmonic generated for a 20 MHz input tone is
typically –65 dBfs. In hold mode, under the same conditions
and sampling at 30 MSPS, the worst harmonic generated is
V
IN
t
6ns
DHT
V
V
Figure 1. Acquisition Time Diagram
CH
OUT
BUFFER
TIME
INPUT
TRACK
CH
ACQUISITION TIME
AT C
. Since the small-signal settling time of
C
V
H
CH
H
TO X%
HOLD
t
S
OUTPUT
BUFFER
PEAK TRANSIENT
SEEN BY OUTPUT
BUFFER
OUT
(due to slew rate
V
OUT
CH
has
–6–
–74 dBfs. The reason is the output buffer in hold mode has only
dc distortion relevancy. With its inherent linearity (7 ns settling
to 0.01%), the output buffer has essentially settled to its dc
distortion level even for track plus hold times as short as 30 ns.
For a traditional open-loop output buffer, the ac (track mode)
and dc (hold mode) distortion levels are often the same.
Droop Rate
Droop rate does not necessarily affect a track and hold’s distor-
tion characteristics. If the droop rate is constant versus the input
voltage for a given hold time, it manifests itself as a dc offset to
the encoder. For the AD9100, the droop rate is typically
would see a 1 mV offset voltage. If there is no droop sensitivity
to the held voltage value, the 1 mV offset would be constant
and “ride” on the input signal and introduce no hold-mode
nonlinearities .
In instances in which droop rate varies proportionately to the
magnitude of the held voltage signal level, a gain error only is
introduced to the A/D encoder. The AD9100 has a droop sensi-
tivity to the input level of 1.5 mV/ V– s. For a 2 V p-p input sig-
nal, this translates to a 0.15%/ s gain error and does not cause
additional distortion errors.
For the AD9100, droop sensitivity to input level is insignificant.
However, hold times longer than about 2 s can cause distortion due
to the R
hold mode noise will increase linearly vs. hold time and thus de-
grade SNR performance.
Layout Considerations
For best performance results, good high speed design tech-
niques must be applied. The component (top) side ground
plane should be as large as possible; two-ounce copper cladding
is preferable. All runs should be as short as possible, and decou-
pling capacitors must be used.
Figure 2 is the schematic of a recommended AD9100 evaluation
board. (Contact factory concerning availability of assembled
boards.) All 0.01 F decoupling capacitors should be low
inductance surface mount devices (P/N 05085C103MT050
from AVX) and connected on the component side within 30
mils of the designated pins; with the other sides soldered
directly to the top ground plane.
The 10 F low frequency power supply tantalum decoupling
capacitors should be located within 1.5 inches of the AD9100.
The common 0.01 F supply capacitors can be wired together.
The common power supply bus (connected to the 10 F
capacitor and power supply source) can be routed to the
underside of the board to the daisy chain wired 0.01 F supply
capacitors.
For remote input and/or output drive applications, controlled
impedances are required to minimize line reflections which will
reduce signal fidelity. When capacitive and/or high impedance
levels are present, the load and/or source should be physically
located within approximately one inch of the AD9100. Note
that a series resistance, R
6 pF. (The Recommended R
Performance Section” shows values of R
loads which result in no more than a 20% increase in settling
time for loads up to 80 pF.) As much of the ground plane as
possible should be removed from around the V
to minimize coupling onto the analog signal path.
1 mV/ s. If a signal is held for 1 s, a subsequent encoder
C
H
time constant at the hold capacitor. In addition,
S
, is required if the load is greater than
S
vs. CL chart in the “Typical
S
for various capacitive
IN
and V
OUT
REV. A
pins