BLM41PG181SN1L Murata Electronics, BLM41PG181SN1L Datasheet - Page 182
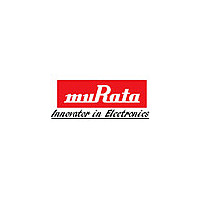
BLM41PG181SN1L
Manufacturer Part Number
BLM41PG181SN1L
Description
EMI Filter 3A Flat Style SMD
Manufacturer
Murata Electronics
Type
EMI Suppression Filterr
Datasheet
1.BLM18EG121SN1-D.pdf
(209 pages)
Specifications of BLM41PG181SN1L
Case Size
1806
Maximum Current Rating
3 A
Termination
Flat Style
Available stocks
Company
Part Number
Manufacturer
Quantity
Price
Company:
Part Number:
BLM41PG181SN1L
Manufacturer:
MURATA
Quantity:
5 000
Part Number:
BLM41PG181SN1L
Manufacturer:
MURATA/村田
Quantity:
20 000
- Current page: 182 of 209
- Download datasheet (9Mb)
PL
o
!Note
180
1. Standard Land Pattern Dimensions
PLT10H
2. Solder Paste Printing and Adhesive Application
PLT10H
PCB Warping
When reflow soldering the
coils, the printing must be conducted in accordance with
the following cream solder printing conditions.
If too much solder is applied, the chip will be prone to
damage by mechanical and thermal stress from the PCB
and may crack.
Standard land dimensions should be used for resist and
copper foil patterns.
PCB should be designed so that products are not
subjected to the mechanical stress caused by warping
the board.
• Please read rating and !CAUTION (for storage, operating, rating, soldering, mounting and handling) in this catalog to prevent smoking and/or burning, etc.
• This catalog has only typical specifications because there is no space for detailed specifications. Therefore, please review our product specifications or consult the approval sheet for product specifications before ordering.
Series
p
Chip Common Mode Choke Coil
oGuideline of solder paste thickness:
*Solderability is subject to reflow conditions and thermal conductivity. Please make sure that your
oReflow Soldering
product has been evaluated in view of your specifications with our product being mounted to your
product.
150-200 m: PLT10H
For the solder paste printing pattern, use standard land dimensions.
chip common mode choke
4.0
PLT10H
8.0
4.0
Solder Paste Printing
Copper Foil Pattern
Copper Foil Pattern + Resist
Resist
When flow soldering the
apply the adhesive in accordance with the following
conditions.
If too much adhesive is applied, then it may overflow into
the land or termination areas and yield poor solderability.
In contrast, if insufficient adhesive is applied, or if the
adhesive is not sufficiently hardened, then the chip may
become detached during flow soldering process.
Soldering and Mounting
Products should be located in the sideways direction
(Length: a<b) to the mechanical stress.
Poor example
chip common mode choke
Good example
b
a
(in mm)
coils,
Mar.28,2011
C31E.pdf
Related parts for BLM41PG181SN1L
Image
Part Number
Description
Manufacturer
Datasheet
Request
R

Part Number:
Description:
BUZZER PIEZO 25VP-P SMD
Manufacturer:
Murata Electronics North America

Part Number:
Description:
CAP 4-ARRAY 680PF 100V X7R 1206
Manufacturer:
Murata Electronics North America
Datasheet:

Part Number:
Description:
CAP 4-ARRAY 1000PF 100V X7R 1206
Manufacturer:
Murata Electronics North America
Datasheet:

Part Number:
Description:
CAP 4-ARRAY 1800PF 100V X7R 1206
Manufacturer:
Murata Electronics North America
Datasheet:

Part Number:
Description:
CAP 4-ARRAY 68000PF 16V X7R 1206
Manufacturer:
Murata Electronics North America
Datasheet:

Part Number:
Description:
CAP CER 1000PF 50V 10% X7R 0402
Manufacturer:
Murata Electronics North America
Datasheet:

Part Number:
Description:
CAP CER 10000PF 16V 10% X7R 0402
Manufacturer:
Murata Electronics North America
Datasheet:

Part Number:
Description:
CAP 5.5-25PF 2.5X3.2MM SMD
Manufacturer:
Murata Electronics North America
Datasheet:

Part Number:
Description:
CAP 4.5-20PF 2.5X3.2MM SMD
Manufacturer:
Murata Electronics North America
Datasheet:

Part Number:
Description:
CAP 5.0-20PF 3.2X4.5MM SMD RED
Manufacturer:
Murata Electronics North America
Datasheet:

Part Number:
Description:
CAP 2.0-6.0PF 3.2X4.5MM SMD BLU
Manufacturer:
Murata Electronics North America
Datasheet:

Part Number:
Description:
CAP 1.4-3.0PF 3.2X4.5MM SMD BRN
Manufacturer:
Murata Electronics North America
Datasheet:

Part Number:
Description:
CAP 3.0-10PF 3.2X4.5MM SMD WHT
Manufacturer:
Murata Electronics North America
Datasheet:

Part Number:
Description:
CAP 2.0-6.0PF 4X4.5MM TOPADJ BLU
Manufacturer:
Murata Electronics North America
Datasheet:

Part Number:
Description:
CAP 8.5-40PF 4X4.5MM TOPADJ YEL
Manufacturer:
Murata Electronics North America
Datasheet: