NJM#3517E2 NJR, NJM#3517E2 Datasheet - Page 10
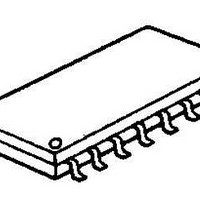
NJM#3517E2
Manufacturer Part Number
NJM#3517E2
Description
Motor / Motion / Ignition Controllers & Drivers Stepper
Manufacturer
NJR
Type
Stepper Motor Controllerr
Datasheet
1.NJM3517D2.pdf
(12 pages)
Specifications of NJM#3517E2
Product
Stepper Motor Controllers / Drivers
Operating Supply Voltage
5 V
Supply Current
60 mA
Mounting Style
SMD/SMT
Package / Case
EMP-16
Lead Free Status / Rohs Status
Lead free / RoHS Compliant
Available stocks
Company
Part Number
Manufacturer
Quantity
Price
7. To change actual motor rotation direction, exchange motor connections at P
8. Half-stepping. in the half-step mode, the power input to the motor alternates between one or two phase
9. Ramping. Every drive system has inertia which must be considered in the drive scheme. The rotor and load
• V
• The inhibit input not pulled low or floating. Inhibit is active high.
• A bipolar motor without a center tap is used. Exchange motor for unipolar version. Connect according to figure 3.
• External transistors connected without proper base-current supply resistor.
• Insufficient filtering capacitors used.
• Current restrictions exceeded.
• L
• A common ground wire is used for all three power supplies. If possible, use separate ground leads for each
If high performance is to be achieved from a stepper motor, the phase must be energized rapidly when turned on
and also de-energize rapidly when turned off. In other words, the phase current must increase/decrease rapidly at
phase shift.
When the winding current is turned off the induced high voltage spike will damage the drive circuits if not properly
suppressed. Different turn-off circuits
Diode turn-off circuit (figure 12)
— Slow current decay
— Energy lost mainly in winding resistance
— Potential cooling problems.
Resistance T O C (figure 13)
—
— Energy lost mainly in R-Ext
— Potential cooling problems
Zener diode T O C (figure 14)
Relatively high V
— Relatively fast current decay
— Energy lost mainly in V
— Potential cooling problems
are used; e. g. :
to specifications, see figures 19 through 24.
supply to minimize power interference.
COMMON FAULT CONDITIONS
DRIVE CIRCUITS
PHASE TURN-OFF CONSIDERATIONS
windings. In half-step mode, motor resonances are reduced. In a two-phase motor, the electrical phase shift
between the windings is 90 degrees. The torque developed is the vector sum of the two windings energized.
Therefore, when only one winding is energized, which is the case in half-step mode for every second step, the
torque of the motor is reduced by approximately 30%. This causes a torque ripple.
inertia plays a big role at higher speeds. Unlike the DC motor, the stepper motor is a synchronous motor and
does not change speed due to load variations. Examination of typical stepper motors’ torque versus speed
curves indicates a sharp torque drop-off for the start-stop without error curve. The reason for this is that the
torque requirements increase by the cube of the speed change. As it can be seen, for good motor perfor-
mance, controlled acceleration and deceleration should be considered.
A
MM
Somewhat faster current decay
and L
supply not connected, or V
B
used for continuous output at high currents. Use the RC network to set a proper duty cycle according
Z
gives:
Z
MM
supply not connected through diodes.
A1
and P
A2
(or P
B1
NJM3517
and P
B2
).