MAX1452CAE+ Maxim Integrated Products, MAX1452CAE+ Datasheet - Page 14
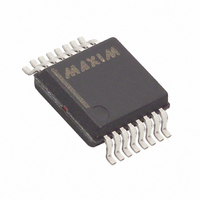
MAX1452CAE+
Manufacturer Part Number
MAX1452CAE+
Description
IC SENSOR SIGNAL COND 16-SSOP
Manufacturer
Maxim Integrated Products
Type
Signal Conditionerr
Datasheet
1.MAX1452CAE.pdf
(25 pages)
Specifications of MAX1452CAE+
Input Type
Analog
Output Type
Analog
Interface
Serial
Current - Supply
2.5mA
Mounting Type
Surface Mount
Package / Case
16-SSOP
Lead Free Status / RoHS Status
Lead free / RoHS Compliant
The analog signal driven onto the OUT pin is deter-
mined by the value in the ALOC register. The signals
are specified in Table 15.
The MAX1452 is designed to support an automated
production test system with integrated calibration and
temperature compensation. Figure 7 shows the imple-
mentation concept for a low-cost test system capable
of testing many transducer modules connected in par-
allel. The MAX1452 allows for a high degree of flexibili-
ty in system calibration design. This is achieved by use
of single-wire digital communication and three-state
output nodes. Depending upon specific calibration
requirements one may connect all the OUTs in parallel
or connect DIO and OUT on each individual module.
Compensation requires an examination of the sensor
performance over the operating pressure and tempera-
ture range. Use a minimum of two test pressures (e.g.,
zero and full-span) and two temperatures. More test
pressures and temperatures result in greater accuracy.
A typical compensation procedure can be summarized
as follows:
Set reference temperature (e.g., +25°C):
•
•
14
Low-Cost Precision Sensor
Signal Conditioner
Figure 6. Analog Output Timing
Initialize each transducer by loading their respec-
tive registers with default coefficients (e.g., based
on mean values of offset, FSO and bridge resis-
tance) to prevent overload of the MAX1452.
Set the initial bridge voltage (with the FSODAC) to
half of the supply voltage. Measure the bridge volt-
age using the BDR or OUT pins, or calculate based
on measurements.
______________________________________________________________________________________
Sensor Compensation Overview
OUT
DIO
Test System Configuration
1 1 1 1 1 0 1 0 0 1 1 0 1 0 1
DRIVEN BY TESTER
HIGH IMPEDANCE
1 1 1 1 1 1 1
THREE-STATE
NEED WEAK
PULLUP
•
•
Set next test temperature:
•
•
•
•
•
The MAX1452 temperature compensation design cor-
rects both sensor and IC temperature errors. This
enables the MAX1452 to provide temperature compen-
sation approaching the inherent repeatability of the
sensor. An example of the MAX1452’s capabilities is
shown in Figure 8.
A repeatable piezoresistive sensor with an initial offset
of 16.4mV and a span of 55.8mV was converted into a
compensated transducer (utilizing the piezoresistive
sensor with the MAX1452) with an offset of 0.5000V and
a span of 4.0000V. Nonlinear sensor offset and FSO
temperature errors, which were on the order of 20% to
30% FSO, were reduced to under ±0.1% FSO. The fol-
lowing graphs show the output of the uncompensated
sensor and the output of the compensated transducer.
Six temperature points were used to obtain this result.
1 1
Calibrate the output offset and FSO of the transduc-
er using the ODAC and FSODAC, respectively.
Store calibration data in the test computer or
MAX1452 EEPROM user memory.
Calibrate offset and FSO using the ODAC and FSO-
DAC, respectively.
Store calibration data in the test computer or
MAX1452 EEPROM user memory.
Calculate the correction coefficients.
Download correction coefficients to EEPROM.
Perform a final test.
1 1 1
THREE-STATE
2
VALID OUT
ATIM
1 1 1 1
TIMES
+1 BYTE
1
1 1
1 1 1 1 1 1 1 1
THREE-STATE
NEED WEAK
PULLUP
Compensation Example
Sensor Calibration and
1 1