QT140-DG Atmel, QT140-DG Datasheet - Page 6
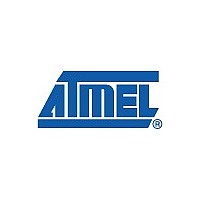
QT140-DG
Manufacturer Part Number
QT140-DG
Description
IC SENSOR 4KEY 5V 5MA SGL 28DIP
Manufacturer
Atmel
Series
QProx™, QTouch™r
Type
Capacitiver
Datasheet
1.QT140-D.pdf
(14 pages)
Specifications of QT140-DG
Touch Panel Interface
10, 2-Wire
Number Of Inputs/keys
4 Key
Resolution (bits)
10, 14 b
Voltage Reference
Internal
Voltage - Supply
3 V ~ 5.5 V
Current - Supply
2.5mA
Operating Temperature
0°C ~ 70°C
Mounting Type
Through Hole
Package / Case
8-DIP (0.300", 7.62mm)
Output Type
*
Interface
*
Input Type
*
Lead Free Status / RoHS Status
Lead free / RoHS Compliant
2 - QT140/QT150 SPECIFICS
2.1 SIGNAL PROCESSING
These devices process all signals using 16 bit
math, using a number of algorithms pioneered by
Quantum. These algorithms are specifically
designed to provide for high survivability in the face
of adverse environmental changes.
2.1.1 D
Signal drift can occur because of changes in Cx,
Cs, and Vdd over time. If a low grade Cs capacitor
is chosen, the signal can drift greatly with
temperature. If keys are subject to extremes of
temperature or humidity, the signal can also drift. It
is crucial that drift be compensated, else false detections,
non-detections, and sensitivity shifts will follow.
Drift compensation (Figure 2-1) is a method that makes the
reference level track the raw signal at a slow rate, only while
no detection is in effect. The rate of reference adjustment
must be performed slowly else legitimate detections can also
be ignored. The IC drift compensates each channel
independently using a slew-rate limited change to the
reference level; the threshold and hysteresis values are
slaved to this reference.
Once an object is sensed, the drift compensation mechanism
ceases since the signal is legitimately high, and therefore
should not cause the reference level to change.
The signal drift compensation is 'asymmetric'; the reference
level drift-compensates in one direction faster than it does in
the other. Specifically, it compensates faster for decreasing
signals than for increasing signals. Increasing signals should
not be compensated for quickly, since an approaching finger
could be compensated for partially or entirely before even
approaching the sense electrode. However, an obstruction
over the sense pad, for which the sensor has already made
full allowance for, could suddenly be removed leaving the
sensor with an artificially elevated reference level and thus
become insensitive to touch. In this latter case, the sensor
will compensate for the object's removal very quickly, usually
in only a few seconds.
With large values of Cs and small values of Cx, drift
compensation will appear to operate more slowly than with
the converse.
2.1.2 T
The internal threshold level is fixed at 6 counts for all
channels. These IC's employ a fixed hysteresis of 2 counts
below the threshold (33%).
2.1.3 M
If a sufficiently large object contacts a key for a prolonged
duration, the signal will trigger a detection output preventing
further normal operation. To cure such ‘stuck key’ conditions,
the sensor includes a timer on each channel to monitor
detection duration. If a detection exceeds the maximum timer
setting, the timer causes the sensor to perform a full
recalibration (if not set for infinite). This is known as the Max
On-Duration feature.
After the Max On-Duration interval, the sensor channel will
once again function normally, even if partially or fully
obstructed, to the best of its ability given electrode
lQ
RIFT
HRESHOLD
AX
O
C
N
OMPENSATION
-D
URATION
C
ALCULATION
T hre sh old
Ou tpu t
6
conditions. There are three timeout durations available via
strap option: 10s, 60s, and infinite (Table 2-1).
Max On-Duration works independently per channel; a
timeout on one channel has no effect on another channel
except when the AKS feature is impacted on an adjacent
key. Note also that the timings in Table 2-1 are dependent on
the oscillator frequency: Doubling the recommended
frequency will halve the timeouts.
Infinite timeout is useful in applications where a prolonged
detection can occur and where the output must reflect the
detection no matter how long. In infinite timeout mode, the
designer should take care to be sure that drift in Cs, Cx, and
Vdd do not cause the device to ‘stick on’ inadvertently even
when the target object is removed from the sense field.
The delay timings for Max On-Duration depend directly on
resonator frequency. Also, if the acquisition burst on one or
more channels lasts longer than 5.5ms per channel, the
specified timings may be longer.
2.1.4 D
It is desirable to suppress false detections due to electrical
noise or from quick brushes with an object. To this end,
these devices incorporate a per-key ‘Detection Integrator’
counter that increments with each signal detection exceeding
the signal threshold (Figure 2-1) until a limit count is
reached, after which an Out pin becomes active. If a ‘no
detect’ is sensed prior to the limit, this counter is reset to
zero. The required limit count is 3.
The Detection Integrator can also be viewed as a
'consensus' vote requiring a detection in three successive
samples to trigger an active output.
2.1.5 F
Pin 28 is a Reset pin, active-low, which in cases where
power is clean can be simply tied to Vdd. On power-up, the
device will automatically recalibrate all channels of sensing.
Pin 28 can also be controlled by logic or a microcontroller to
force the chip to recalibrate, by toggling it low for 5µs then
raising it high again.
2.1.6 R
Response time is fixed at 99ms at a 10MHz clock. Response
time can be altered by changing the clock frequency;
doubling the frequency to 20MHz will cut the response time
to 49ms.
Figure 2-1 Drift Compensation
ORCED
ETECTION
ESPONSE
S ig na l
S
ENSOR
T
I
NTEGRATOR
IME
R efer ence
R
ECALIBRATION
QT140/150 1.01/1102
H ys te res is