NCP5392 ON Semiconductor, NCP5392 Datasheet - Page 24
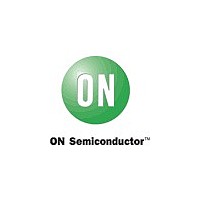
NCP5392
Manufacturer Part Number
NCP5392
Description
2/3/4-Phase Controller
Manufacturer
ON Semiconductor
Datasheet
1.NCP5392.pdf
(32 pages)
Available stocks
Company
Part Number
Manufacturer
Quantity
Price
Company:
Part Number:
NCP5392EMNR2G
Manufacturer:
ON Semiconductor
Quantity:
1 500
Part Number:
NCP5392EMNR2G
Manufacturer:
ON/安森美
Quantity:
20 000
Part Number:
NCP5392MNR2G
Manufacturer:
ON/安森美
Quantity:
20 000
Part Number:
NCP5392P
Manufacturer:
ON/安森美
Quantity:
20 000
Part Number:
NCP5392PMNR2G
Manufacturer:
ON/安森美
Quantity:
20 000
Part Number:
NCP5392Q
Manufacturer:
ON/安森美
Quantity:
20 000
Company:
Part Number:
NCP5392QMNR2G
Manufacturer:
ON Semiconductor
Quantity:
1 800
Company:
Part Number:
NCP5392TMNR2G
Manufacturer:
ON Semiconductor
Quantity:
500
www.DataSheet4U.com
Final Equations for the Current Limit Threshold
I
I
N is the number of phases involved in the circuit.
0.6 mW. Selecting the closest available values of 21.3 kW
for R
operating frequency of 330 kHz. Select R
= 1 k, R
application diagram). That results to an approximate
current limit of 133 A at 100°C for a four phase operation
and 131 A at 25°C. The total sensed current can be
observed as a scaled voltage at the VDRP with a positive
no−load offset of approximately 1.3 V.
Inductor Selection
that the inductor does not saturate by more than 10% at
maximum load. The inductor also must not go into hard
saturation before current limit trips. The demo board
includes a four phase output filter using the T44−8 core
from Micrometals with 3 turns and a DCR target of 0.6 mW
@ 25°C. Smaller DCR values can be used, however,
current sharing accuracy and droop accuracy decrease as
DCR decreases. Use the NCP5392 design aide for
regulation accuracy calculations for specific value of DCR.
LIMIT
LIMIT
Final equations are described based on two conditions: normal mode and PSI mode.
The inductors on the demo board have a DCR at 25°C of
When using inductor current sensing it is recommended
(normal) ^
(PSI) ^
LIM1
T2
and 9.28 kW for R
= 10 K (25°C), R
4 @
4 @
(R
NOR
R
(R
NOR
NOR
)R
R
NOR
@(R
ISO1
)R
ISO1
@(R
ISO1
)R
ISO1
)R
ISO2
)R
NOR
ISO2
)R
LIM2
ISO2
)R T2 )@R
ISO2
)R T2 )
/R
)R T2 )@R
SUM
R LIM1 )R LIM2
)R T2 )
yields a nominal
2V@R LIM2
SUM
ISO
SUM
= 2, (refer to
1 = 1 k, R
@ DCR
R LIM1 )R LIM2
@ DCR
2V@R LIM2
@ COEpsi
25C
http://onsemi.com
(1 ) 0.00393 @ (T
ISO2
25C
(1 ) 0.00393 @ (T
24
Inductor Current Sensing Compensation
An RC filter is selected to cancel out the impedance from
inductor and recover the current information through the
inductor’s DCR. This is done by matching the RC time
constant of the sensing filter to the L/DCR time constant.
The first cut approach is to use a 0.1 mF capacitor for C and
then solve for R.
inductor temperature final selection of R is best done
experimentally on the bench by monitoring the V
and performing a step load test on the actual solution.
R
The NCP5392 uses the inductor current sensing method.
Because the inductor value is a function of load and
sense
inductor
(T) +
inductor
0.1 @ mF @ DCR
* 25))
* 25))
* 0.5 @
* 0.5 @
25C
(V
in
L @ F
(V
@ (1 ) 0.00393(T * 25))
* V
L
in
* N @ V
SW
L @ F
out
@ V
) @ V
SW
in
out
out
@ V
) @ V
in
droop
(eq. 7)
(eq. 8)
(eq. 9)
out
pin