pbl37761 ETC-unknow, pbl37761 Datasheet - Page 5
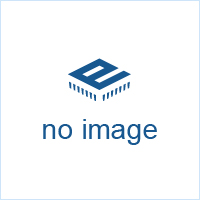
pbl37761
Manufacturer Part Number
pbl37761
Description
Dual Controller High Current Stepper Motor Applications
Manufacturer
ETC-unknow
Datasheet
1.PBL37761.pdf
(8 pages)
Functional Description
Each channel of the PBL 3776/1
consists of the following sections:
•
•
•
by switching the output current to the
windings. This is done by sensing the
peak current through the winding via a
current-sensing resistor R
connected in series with the motor
winding. As the current increases, a
voltage develops across the sensing
resistor, which is fed back to the
comparator. At the predetermined level,
defined by the voltage at the reference
input V
flop, which turns off the sourcing output
transistor in the circuit. Consequently the
Figure 5. Typical 5 A stepper motor driver application with PBL 3776/1. One channel shown.
Constant current control is achieved
PHASE CH 2
DISABLE CH 2
REFERENCE VOLTAGE CH 2
+5 V
An output section with four output
transistors, two sourcing and two
sinking, intended to drive the four
transistors in an external H-bridge.
Each transistor is capable of driving
up to 200 mA continuous current.
A logic section that controls the
output transistors.
An S-R flip-flop, and a comparator.
The clock-oscillator is common to
both channels.
R
, the comparator resets the flip-
12 k
4700 pF
Ct
Rt
V
RC
CC
13
12
PBL
3776/1
V
S
CC
+
–
, effectively
Phase 2
Phase 1
15
10
14
Dis 1
Dis
11
2
V
8
17
V
R1
R2
C 1
C 2
9
16
+
–
+
–
correspond-ing lower external transistor,
in the H-bridge, is turned off. The turn-off
of one channel is independent of the
other channel. The current decreases
until the clock oscillator triggers the flip-
flops of both channels simultaneously,
which turns on the output transistors
again, and the cycle is repeated.
switching transients at turn-on, the PBL
3776/1 includes a digital filter. The clock
oscillator provides a blanking pulse
which is used for digital filtering of the
voltage transient across the current
sensing resistor during turn-on. Due to
the high output drive capability, this
transient might exceed the max. allowed
voltage on the C inputs and damage the
circuit. A resistor is placed in the
feedback loop in order to prevent this
transient from damaging the circuit.
off and phase shift are shown in figure 6.
Applications Information
Output current
The maximum peak output, sink/source,
current is 500 mA. But due to the power
handling capacity of the package this
SGND 1
To prevent erroneous switching due to
The current paths during turn-on, turn-
SGND 2
7
18
R Q
S
S
R
Q
Pwr GND 1
1
24
Pwr GND 2
19
22
20
21
23
6
2
4
5
3
T1BL
T1AL
T1AU
T1BU
T2BU
T2AU
T2AL
T2BL
V
V
1000pF
BB1
BB2
R8
1k
R5
390
390
R2
R6
270
270
R1
current can only be used for a short
period of time (1mS). Recommended
max continuous output current is 200
mA/output transistor. This is practical
when driving MOS FET power
transistors, since a high peak output
current capability will rapidly charge/
discharge the gate capacitance, while
the continuous current usage is very
small.
Current control
The regulated output current level to the
motor winding is determined by the
voltage at the reference input and the
value of the sensing resistor, R
peak current through the sensing
resistor (and the motor winding) can be
expressed as:
I
With a recommended value of 0.1 ohm
for the sense resistor R
ce voltage will produce an output current
of approximately 5 A. R
selected for maximum motor current.
Chopping frequency, winding inductance
and supply voltage also affect the
current, but to much less extent.
M,peak
Q1
IRF9Z34
Q3
IRFZ34
= 0.1·V
R
/ R
Vmm
Rs
0.11
S
390
R7
390
R4
[A]
R8
270
PBL 3776/1
R3
270
S
S
, a 5 V referen-
should be
Q2
IRF9Z34
Q4
IRFZ34
S
. The
5
+