sc656 Semtech Corporation, sc656 Datasheet - Page 13
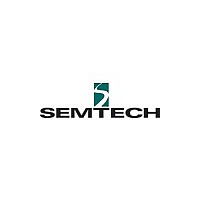
sc656
Manufacturer Part Number
sc656
Description
Backlight Driver For 7 Leds With Charge Pump And Pwm Control
Manufacturer
Semtech Corporation
Datasheet
1.SC656.pdf
(17 pages)
Applications Information (continued)
LED Backlight Current Sinks
The full scale backlight current (I
through the ISET pin controlling the corresponding LED
bank (ISETM or ISETS) . The I
of the ISETM or ISETS pin current multiplied by an internal
gain of 00A/A. R
current into the ISETM and ISETS pins. The relationship
between each resistance R
current is:
All backlight current sinks have matched currents, even
when there is a variation in the forward voltages (∆V
the LEDs. A ∆V
voltage is at 2.9V. Higher ∆V
when V
compared and the lowest output is used for setting the
voltage regulation at the OUT pin. This is done to ensure
that sufficient bias exists for all LEDs.
Any unused LED driver outputs must be left open for
normal operation.
PWM Operation
A PWM signal on the ENM or ENS pin can be used to
adjust the DC current through the LEDs. When the duty
cycle is 00%, the backlight current through each LED (I
equals the full scale current set by the corresponding ISET
pin. As the duty cycle decreases, the ENM or ENS input
samples the control signal and converts the duty cycle to
a DC current level. In conventional PWM controlled
systems, the output current pulses on and off with the
PWM input to achieve an average output current.
Providing a DC current through the LEDs instead of a
pulsed current provides an efficiency advantage over
other PWM controlled systems by allowing the charge
pump to remain in x mode longer since the maximum
current is equal to the average current.
Bank 2
Table 2 — Backlight Bank Configuration Settings
R
ISETx
0
0
IN
= 00/I
is higher than 2.9V. All current sink outputs are
Bank 1
FS_BL
0
0
F
of .0V is supported when the input
ISETM
and R
Main Bank
BL — BL7
BL2 — BL7
BL3 — BL7
BL4 — BL7
ISETx
F
FS_BL
ISETS
LED mis-match is supported
and the full scale backlight
FS_BL
is regulated to the value
are used to control the
) is set via the current
Sub Bank
BL — BL2
BL — BL3
none
BL
F
) of
BL
)
PWM Sampling
The sampling system that translates the PWM signal to
a DC current requires the ENM and ENS pins to have a
minimum high time t
time less than t
I
minimum high time specification varies with the applied
PWM frequency (see figure ). Note that use of a lower
PWM frequency, from 200Hz to 0kHz, will support
lower minimum duty cycle and an extended backlight
dimming range.
Shutdown Mode
Shutdown occurs after ENM and ENS are both held low
for an interval of 5ms or more. When the ENM and ENS
pins are both held low for 5ms or less, the device will not
shutdown.
Protection Features
The SC656 provides several protection features to safe-
guard the device from catastrophic failures. These features
include:
BL
•
•
•
•
. The minimum duty cycle needed to support the
5
4
3
2
1
0
0.2
t
Output Open Circuit Protection
Over-Temperature Protection
Charge Pump Output Current Limit
LED Float Detection
HIGH_MIN
= 1µs
Figure 1 — Minimum Duty Cycle
10
HIGH_MIN
impacts the accuracy of the target
HIGH_MIN
PWM Frequency (kHz�
20
to set the DC level. High
30
40
SC656
3
50