ADMC331-PB Analog Devices, ADMC331-PB Datasheet - Page 12
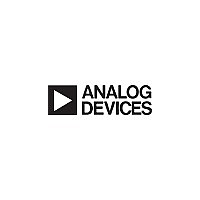
ADMC331-PB
Manufacturer Part Number
ADMC331-PB
Description
Single Chip DSP Motor Controller
Manufacturer
Analog Devices
Datasheet
1.ADMC331-PB.pdf
(36 pages)
ADMC331
Boot Loading
On power-up or reset, the ADMC331 is configured so that
execution begins at the internal PM ROM at address 0x0800.
This starts execution of the internal monitor function that first
performs some initialization functions and copies a default inter-
rupt vector table to addresses 0x0000–0x002F of program memory
RAM. The monitor next attempts to boot load from an external
SROM or E
tion of Figure 4. The monitor program first toggles the RFS1/
SROM pin of the ADMC331 to reset the serial memory device.
If an SROM or E
clocked into the ADMC331 at a rate CLKOUT/20. Both pro-
gram and data memory RAM can be loaded from the SROM or
E
begins at address 0x0030. This is where the first instruction of
the user code should be placed.
If boot loading from an E
code reconfigures SPORT1 as a UART and attempts to receive
commands from an external device on this serial port. The
monitor then waits for a byte to be received over SPORT1,
locks onto the baud rate of the external device (autobaud fea-
ture) and takes in a header word that tells it with what type of
device it is communicating. There are six alternatives:
• A UART boot loader such as a Motorola 68HC11SCI port.
• A synchronous slave boot loader (the clock is external).
• A synchronous master boot loader (the ADMC331 provides the
• A UART debugger interface.
• A synchronous master debugger interface.
• A synchronous slave debugger interface.
With the debugger interface, the monitor enters an interactive
mode in which it processes commands received from the exter-
nal device.
DSP Control Registers
The DSP core has a system control register, SYSCNTL, memory
mapped at DM (0x3FFF). SPORT0 is enabled when Bit 12 is
set, disabled when this bit is cleared. SPORT1 is enabled when
Bit 11 is set, disabled when this bit is cleared. SPORT1 is con-
figured as a serial port when Bit 10 is set, or as flags and inter-
rupt lines when this bit is cleared. For proper operation of the
ADMC331, all other bits in this register must be cleared (which
is their default).
The DSP core has a wait state control register, MEMWAIT,
memory mapped at DM (0x3FFE). For proper operation of the
ADMC331, this register must always contain the value 0x8000
(which is the default).
The configuration of both the SYSCNTL and MEMWAIT
registers of the ADMC331 is shown at the end of the data sheet.
THREE-PHASE PWM CONTROLLER
Overview
The PWM generator block of the ADMC331 is a flexible, pro-
grammable, three-phase PWM waveform generator that can be
programmed to generate the required switching patterns to drive
a three-phase voltage source inverter for ac induction (ACIM),
or permanent magnet synchronous (PMSM) or a switched or
variable reluctance (SRM) motor control. In addition, the
PWM block contains special functions that considerably sim-
plify the generation of the required PWM switching patterns for
2
clock).
PROM. After the boot load is complete, program execution
2
PROM on SPORT1 using the three wire connec-
2
PROM is connected to SPORT1, data is
2
PROM is unsuccessful, the monitor
control of the electronically commutated motor (ECM) or
brushless dc motor (BDCM).
The PWM generator produces three pairs of PWM signals on
the six PWM output pins (AH, AL, BH, BL, CH and CL). The
six PWM output signals consist of three high side drive signals
(AH, BH and CH) and three low side drive signals (AL, BL and
CL). The polarity of the generated PWM signals may be
programmed by the PWMPOL pin, so that either active HI or
active LO PWM patterns can be produced by the ADMC331.
The switching frequency, dead time and minimum pulsewidths
of the generated PWM patterns are programmable using respec-
tively the PWMTM, PWMDT and PWMPD registers. In addi-
tion, three duty cycle control registers (PWMCHA, PWMCHB
and PWMCHC) directly control the duty cycles of the three
pair of PWM signals.
When the PWMSR pin is pulled low, the PWM generator trans-
forms the six PWM output signals into six waveforms for
switched reluctance gate drive signals. The low side PWM
signals from the three-phase timing unit assume permanently
ON states, independent of the value written to the duty-cycle
registers. The duty cycles of the high side PWM signals from the
timing unit are still determined by the three duty-cycle registers.
Each of the six PWM output signals can be enabled or disabled
by separate output enable bits of the PWMSEG register. In
addition, three control bits of the PWMSEG register permit
crossover of the two signals of a PWM pair for easy control of
ECM or BDCM. In crossover mode, the PWM signal destined
for the high side switch is diverted to the complementary low
side output and the signal destined for the low side switch is
diverted to the corresponding high side output signal.
In many applications, there is a need to provide an isolation
barrier in the gate-drive circuits that turn on the power devices
of the inverter. In general, there are two common isolation
techniques, optical isolation using opto-couplers, and trans-
former isolation using pulse transformers. The PWM controller
of the ADMC331 permits mixing of the output PWM signals
with a high frequency chopping signal to permit easy interface to
such pulse transformers. The features of this gate-drive chop-
ping mode can be controlled by the PWMGATE register. There
is an 8-bit value within the PWMGATE register that directly con-
trols the chopping frequency. In addition, high frequency chopping
can be independently enabled for the high side and the low side
outputs using separate control bits in the PWMGATE register.
The PWM generator is capable of operating in two distinct
modes, single update mode or double update mode. In single
update mode, the duty cycle values are programmable only once
per PWM period, so that the resultant PWM patterns are sym-
metrical about the midpoint of the PWM period. In the double
update mode, a second updating of the PWM duty cycle values
is implemented at the midpoint of the PWM period. In this
mode, it is possible to produce asymmetrical PWM patterns,
that produce lower harmonic distortion in three-phase PWM
inverters. This technique also permits the closed loop controller
to change the average voltage applied to the machine winding at
a faster rate and so permits fast closed loop bandwidths to be
achieved. The operating mode of the PWM block (single or
double update mode) is selected by a control bit in MODECTRL
register.