A4403 ALLEGRO [Allegro MicroSystems], A4403 Datasheet
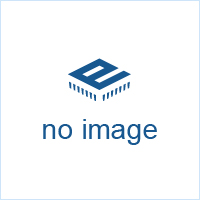
A4403
Available stocks
Related parts for A4403
A4403 Summary of contents
Page 1
... Resistors R3 and R4 should be surface mount, low inductance type, rated at 250 mW at 70°C 4403-DS, Rev. 1 Description The A4403 is a buck converter that uses valley current-mode control. This control scheme allows very short switch on-times to be achieved, making it ideal for applications that require high switching frequencies combined with high input voltages and low output voltages ...
Page 2
... A4403 Selection Guide Part Number A4403GEU-T 92 pieces per tube A4403GEUTR-T 1500 pieces per 7-in. reel Absolute Maximum Ratings (reference to GND) Characteristic VIN Pin Supply Voltage LX Pin Switching Node Voltage ISEN Pin Current Sense Voltage DIS Pin Disable Voltage TON Pin On-Time Voltage ...
Page 3
... A4403 44 2.2 μF R2 Sleep R1 Not Circuit 68 kΩ Fitted TON On Timer Off Timer DIS Switch Closed = On VIN UVLO Linear OK Fault TSD Switching Frequency = 1 MHz All capacitors are X5R or X7R ceramic Resistors R3 and R4 should be surface mount, low inductance type, rated at 250 mW at 70°C ...
Page 4
... A4403 ELECTRICAL CHARACTERISTICS Characteristic General V Quiescent Current IN Feedback Voltage Feedback Input Bias Current 2 Output Voltage Tolerance On-Time Tolerance Minimum On-Time Period Minimum Off-Time Period Buck Switch On-Resistance Current Limit Threshold Soft Start Current Source Input DIS Input Voltage Threshold DIS Open-Circuit Voltage ...
Page 5
... A4403 Basic Operation The A4403 is a buck converter that utilizes valley current-mode control. The on-time is set by the amount of current that flows into the TON pin. This is determined by the value of the TON resistors chosen (R1 and R2 in the Functional Block diagram) and the magnitude of the input voltage, V Under a specific set of conditions, an on-time can be set that then dictates the switching frequency ...
Page 6
... A4403 In general, the feedback resistors should have the lowest resis- tance possible, to minimize any noise pick-up effects and to minimize voltage offsets on the output caused by the bias current flowing out of the FB node into R6. Reducing the feedback BIAS resistances does introduce another loading effect on the output, which has an effect on the standby current ...
Page 7
... Depending on the values selected, this network may provide all least some, of the minimum loading requirement. Control Loop The process of closing the control loop for the A4403 has been greatly simplified through the integration of the compensation components into the device. The control loop , ...
Page 8
... A4403 When the output voltage is set for 0.8 V, the typical bandwidth is 90 kHz with a phase margin of 45° at full load. As the load is reduced, the bandwidth remains largely constant; however, the phase margin tends to reduce slightly because the output power pole is shifted down in frequency, introducing the phase lag sooner. At light loads, before pulse frequency modulation occurs, the phase margin reduces to approximately 40° ...
Page 9
... A4403 current, with perhaps some margin to allow for overloads, and so forth. • saturation current. The worst case maximum peak current should not exceed the saturation current and indeed some mar- gin should be allowed. The maximum peak current can be found to ensure the saturation current level of the chosen inductor is ...
Page 10
... To minimize the heating effects from the A4403 on the diode and vice-versa recommended that the diode be mounted on the reverse side of the printed circuit board. ...
Page 11
... PCB may influence the thermal performance of the A4403. For example, the power loss contribution from the recirculation diode and the sense resistor may cause the junction temperature of the A4403 to be higher than expected.) It should be noted that this process is usually an iterative one to achieve the optimum solution. ...
Page 12
... For maximum effectiveness, the PCB area underneath the thermal pad of the A4403 should be flooded with copper. Several thermal vias (say between 4 and 8) should be used to connect the thermal pad to the internal ground plane. If possible, a further thermal copper plane should be applied to the bottom side of the PCB and connected to the thermal pad of the A4403 through the vias ...
Page 13
... To avoid ground offset issues in the output voltage highly recommended that the ground-referenced feedback resistor R6 should be connected directly to the GND connection of the A4403. In other words, the R6 ground return should avoid the use of the internal ground plane. All ground-referenced support components (C5 and the DIS switch) should also be located as close to the GND connection as possible. A “ ...
Page 14
... A4403 In terms of grounding the power components, a star connection should be made to minimize the ground loop impedances. Note that, although a ground plane may be required to meet the ther- mal characteristics of the solution still imperative to imple- ment a star ground connection for the power components. ...
Page 15
... A4403 4.00 ±0. 17X 0.08 C 0.30 ±0.05 0.65 0.40 ±0. 2.70 Copyright ©2008-2009, Allegro MicroSystems, Inc. The products described here are manufactured under one or more U.S. patents or U.S. patents pending. Allegro MicroSystems, Inc. reserves the right to make, from time to time, such de par tures from the detail spec tions as may be required to per- mit improvements in the per for mance, reliability, or manufacturability of its products ...