HCS200-I/SN Microchip Technology, HCS200-I/SN Datasheet - Page 10
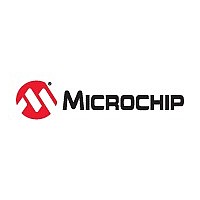
HCS200-I/SN
Manufacturer Part Number
HCS200-I/SN
Description
IC CODE HOPP ENCODER 7FUNC 8SOIC
Manufacturer
Microchip Technology
Type
Code Hopping Encoderr
Specifications of HCS200-I/SN
Package / Case
8-SOIC (3.9mm Width)
Applications
Remote Secure Access, Keyless Entry
Mounting Type
Surface Mount
Product
Encoder
Logic Family
HCS
Number Of Bits
32
Supply Voltage (max)
13 V
Supply Voltage (min)
3.5 V
Maximum Operating Temperature
+ 85 C
Minimum Operating Temperature
- 40 C
Mounting Style
SMD/SMT
Ic Function
Encoder IC
Supply Voltage Range
3.5V To 13V
Operating Temperature Range
-40°C To +85°C
Digital Ic Case Style
SOIC
No. Of Pins
8
Termination Type
SMD
Rohs Compliant
Yes
Filter Terminals
SMD
Leaded Process Compatible
Yes
Lead Free Status / RoHS Status
Lead free / RoHS Compliant
Lead Free Status / RoHS Status
Lead free / RoHS Compliant, Lead free / RoHS Compliant
Available stocks
Company
Part Number
Manufacturer
Quantity
Price
Company:
Part Number:
HCS200-I/SN
Manufacturer:
FSC
Quantity:
1 200
HCS200
6.0
When using the HCS200 in a system, the user will have
to program some parameters into the device, such as
the serial number and crypt key, before it can be used.
The programming cycle allows the user to input all 192
bits in a serial data stream, which are then stored inter-
nally in EEPROM. Programming will be initiated by
forcing the PWM line high, after the S2 line has been
held high for the appropriate length of time (Table 6-1
and Figure 6-1). After the Program mode is entered, a
delay must be provided for the automatic bulk write
cycle to complete. This will write all locations in the
EEPROM to zeros. The device can then be pro-
grammed by clocking in 16 bits at a time, using S2 as
the clock line and PWM as the data in line; data is
clocked in on the falling edge of S2. After each 16-bit
FIGURE 6-1:
FIGURE 6-2:
DS40138C-page 10
(Clock)
(Clock)
(Data)
PWM
(Data)
PWM
Note 1: Unused button inputs to be held to ground during the entire programming sequence.
S2
S2
Note: If a Verify operation is to be done, then it must immediately follow the Program cycle.
End of Programming Cycle
2: The V
PROGRAMMING THE HCS200
Enter Program
Bit190
T
PS
Mode
Bit191
T
DD
PH
pin must be taken to ground after a Program/Verify cycle.
1
PROGRAMMING WAVEFORMS
VERIFY WAVEFORMS
T
PH
T
2
WC
T
PBW
T
Bit 0
Beginning of Verify Cycle
CLKH
Bit 0
T
CLKL
Bit 1
Bit 1 Bit 2
T
Bit 2
DS
T
DV
Repeat for each word (12 times)
T
Bit 3
DH
Data for Word 0 (KEY_0)
Data from Word 0
Bit 3
word is sent, a programming delay of TWC is required
for the internal program cycle to complete. At the end
of the programming cycle, the device can be verified
(Figure 6-2) by reading back the EEPROM. Reading is
done by clocking the S2 line and reading the data bits
on PWM. The falling edge of S2 initiates the reading.
For security reasons, it is not possible to execute a Ver-
ify function without first programming the EEPROM. A
Verify operation can only be done immediately fol-
lowing the Program cycle.
Bit 14
Note:
Bit 14
Bit 15
To ensure that the device does not acci-
dentally enter Programming mode (result-
ing in a bulk erase), PWM should never be
pulled high by the circuit connected to it.
Special care should be taken when driving
PNP RF transistors.
Bit 15
T
WC
Bit 16 Bit 17
2002 Microchip Technology Inc.
Data for Word 1
Bit 16
Bit190 Bit191
Bit 17