MAX9675EVKIT+ Maxim Integrated Products, MAX9675EVKIT+ Datasheet - Page 21
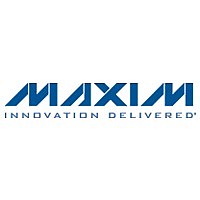
MAX9675EVKIT+
Manufacturer Part Number
MAX9675EVKIT+
Description
KIT EVAL FOR MAX9675
Manufacturer
Maxim Integrated Products
Specifications of MAX9675EVKIT+
Main Purpose
Interface, Crosspoint Switch/Multiplexer
Embedded
No
Utilized Ic / Part
MAX9675
Primary Attributes
16 x 16 Video Crosspoint Switch
Secondary Attributes
Graphical User Interface, USB Interface
Lead Free Status / RoHS Status
Lead free / RoHS Compliant
The MAX9675 features an asynchronous bidirectional
RESET with an internal 20kΩ pullup resistor to V
When RESET is pulled low, either by internal circuitry,
or driven externally, the analog output buffers are
latched into a high-impedance state. After RESET is
released, the output buffers remain disabled. The out-
puts may be enabled by sending a new 96-bit data
word or a 16-bit individual output address word. A reset
is initiated from any of three sources. RESET can be
driven low by external circuitry to initiate a reset, or
RESET can be pulled low by internal circuitry during
power-up (power-on reset) or thermal shutdown.
Since driving RESET low only clears the output buffer
enable bit in the matrix control latches, RESET can be
used to disable all outputs simultaneously. If no new
data has been loaded into the 96-bit complete matrix
mode register, a single UPDATE restores the previous
matrix control settings.
The power-on reset ensures all output buffers are in a
disabled state when power is initially applied. A V
voltage comparator generates the power-on reset.
When the voltage at V
on-reset comparator pulls RESET low through internal
circuitry. As the digital supply voltage ramps up cross-
ing 2.5V, the MAX9675 holds RESET low for 40ns (typ).
Connecting a small capacitor from RESET to DGND
extends the power-on-reset delay. See the RESET
Delay vs. RESET Capacitance graph in the Typical
Operating Characteristics.
The MAX9675 features thermal shutdown protection
with temperature hysteresis. When the die temperature
exceeds +150°C, the MAX9675 pulls RESET low, dis-
abling the output buffers. When the die cools by 20°C,
the RESET pulldown is deasserted, and output buffers
remain disabled until the device is programmed again.
The MAX9675 can be easily used to create larger
switching matrices. The number of ICs required to
implement the matrix is a function of the number of
input channels, the number of outputs required, and
whether the array needs to be nonblocking. The most
straightforward technique for implementing nonblock-
ing matrices is to arrange the building blocks in a grid.
The inputs connect to each vertical bank of devices in
parallel with the other banks. The outputs of each build-
ing block in a vertical column connect together in a
Building Large Video-Switching Systems
Applications Information
______________________________________________________________________________________
DD
is less than 2.5V, the power-
Thermal Shutdown
Power-On Reset
110MHz, 16 x 16 Video Crosspoint
Switch with Programmable Gain
RESET
DD
DD
.
wired-OR configuration. Figure 6 shows a 128-input,
32-output, nonblocking array using the MAX9675 16 x
16 crosspoint devices.
The wired-OR connection of the outputs shown in the
diagram is possible because the outputs of the IC
devices can be placed in a disabled or high-imped-
ance output state. This disable state of the output
buffers is designed for a maximum impedance vs. fre-
quency while maintaining a low-output capacitance.
These characteristics minimize the adverse loading
effects from the disabled outputs. Larger arrays are
constructed by extending this connection technique to
more devices.
Figure 6 shows an implementation requiring many out-
puts to be wired together. This creates a situation
where each output buffer sees not only the normal load
impedance, but also the disabled impedance of all the
other outputs. This impedance has a resistive and a
capacitive component. The resistive components
reduce the total effective load for the driving output.
Total capacitance is the sum of the capacitance of all
the disabled outputs and is a function of the size of the
matrix. Also, as the size of the matrix increases, the
length of the PCB traces increases, adding more
capacitance. The output buffers have been designed to
drive more than 30pF of capacitance while still main-
taining a good AC response. Depending on the size of
the array, the capacitance seen by the output can
exceed this amount. There are several ways to improve
the situation. The first is to use more building-block
crosspoint devices to reduce the number of outputs
that need to be wired together (Figure 7).
In Figure 7, the additional devices are placed in a sec-
ond bank to multiplex the signals. This reduces the
number of wired-OR connections. Another solution is to
put a small resistor in series with the output before the
capacitive load to limit excessive ringing and oscilla-
tions. Figure 8 shows the graph of the Optimal Isolation
Resistor vs. Capacitive Load. A lowpass filter is created
from the series resistor and parasitic capacitance to
ground. A single R-C does not affect the performance
at video frequencies, but in a very large system there
may be many R-Cs cascaded in series. The cumulative
effect is a slight rolling off of the high frequencies caus-
ing a "softening" of the picture. There are two solutions
to achieve higher performance. One way is to design
the PCB traces associated with the outputs such that
they exhibit some inductance. By routing the traces in a
repeating "S" configuration, the traces that are nearest
each other exhibit a mutual inductance increasing the
total inductance. This series inductance causes the
Driving a Capacitive Load
21