MAX15031EVKIT+ Maxim Integrated Products, MAX15031EVKIT+ Datasheet - Page 14
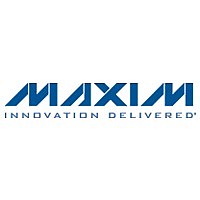
MAX15031EVKIT+
Manufacturer Part Number
MAX15031EVKIT+
Description
KIT EVALUATION FOR MAX15031
Manufacturer
Maxim Integrated Products
Specifications of MAX15031EVKIT+
Main Purpose
DC/DC, Step Up
Outputs And Type
1, Non-Isolated
Voltage - Output
70V
Current - Output
4mA
Voltage - Input
2.9 ~ 5.5V
Regulator Topology
Boost
Frequency - Switching
400kHz
Board Type
Fully Populated
Utilized Ic / Part
MAX15031
Lead Free Status / RoHS Status
Lead free / RoHS Compliant
Power - Output
-
Lead Free Status / Rohs Status
Lead free / RoHS Compliant
80V, 300mW Boost Converter and Current
Monitor for APD Bias Applications
Calculate the value of the monitor current-limit resistor,
R
lowing equation:
The R
for APD currents from 1mA to 5mA.
When using the MAX15031 to monitor APD or PIN pho-
todiode currents in fiber applications, several issues
must be addressed. In applications where the photodi-
ode must be fully depleted, keep track of voltages bud-
geted for each component with respect to the available
supply voltage(s). The current monitors require as
much as 1.1V between BIAS and APD, which must be
considered part of the overall voltage budget.
Additional voltage margin can be created if a negative
supply is used in place of a ground connection, as long
as the overall voltage drop experienced by the
MAX15031 is less than or equal to 76V. For this type of
application, the MAX15031 is suggested so the output
can be referenced to “true” ground and not the negative
supply. The MAX15031’s output current can be refer-
enced as desired with either a resistor to ground or a
transimpedance amplifier. Take care to ensure that out-
put voltage excursions do not interfere with the required
margin between BIAS and MOUT. In many fiber applica-
tions, MOUT is connected directly to an ADC that oper-
ates from a supply voltage that is less than the voltage
at BIAS. Connecting the MAX15031’s clamping diode
output, CLAMP, to the ADC power supply helps avoid
damage to the ADC. Without this protection, voltages
can develop at MOUT that might destroy the ADC. This
14
LIM
, for a given APD current limit, I
______________________________________________________________________________________
LIM
resistor, R
Determining Monitor Current Limit
Applications Information
R
Using APD or PIN Photodiodes
LIM
LIM
=
10
, ranges from 12.45kΩ to 2.5Ω
×
I
LIMIT
in Fiber Applications
1.245V
(mA)
LIMIT
, using the fol-
protection is less critical when MOUT is connected
directly to subsequent transimpedance amplifiers (linear
or logarithmic) that have low-impedance, near-ground-
referenced inputs. If a transimpedance amplfier is used
on the low side of the photodiode, its voltage drop must
also be considered. Leakage from the clamping diode
is most often insignificant over nominal operating condi-
tions, but grows with temperature.
To maintain low levels of wideband noise, lowpass filter-
ing the output signal is suggested in applications where
only DC measurements are required. Connect the filter
capacitor at MOUT. Determining the required filtering
components is straightforward, as the MAX15031
exhibits a very high output impedance of 890MΩ.
In some applications where pilot tones are used to identi-
fy specific fiber channels, higher bandwidths are desired
at MOUT to detect these tones. Consider the minimum
and maximum currents to be detected, then consult the
frequency response and noise typical operating curves.
If the minimum current is too small, insufficient bandwidth
could result, while too high a current could result in
excessive noise across the desired bandwidth.
Careful PCB layout is critical to achieve low switching
losses and clean and stable operation. Protect sensitive
analog grounds by using a star ground configuration.
Connect SGND and PGND together close to the device
at the return terminal of the output bypass capacitor.
Do not connect them together anywhere else. Keep all
PCB traces as short as possible to reduce stray capaci-
tance, trace resistance, and radiated noise. Ensure that
the feedback connection to FB is short and direct.
Route high-speed switching nodes away from the sen-
sitive analog areas. Use an internal PCB layer for SGND
as an EMI shield to keep radiated noise away from the
device, feedback dividers, and analog bypass capaci-
tors. Refer to the MAX15031 evaluation kit data sheet
for a layout example.
Layout Considerations