AS1324-AD EB austriamicrosystems, AS1324-AD EB Datasheet - Page 11
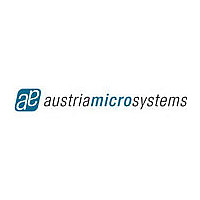
AS1324-AD EB
Manufacturer Part Number
AS1324-AD EB
Description
BOARD EVAL AS1324-AD
Manufacturer
austriamicrosystems
Specifications of AS1324-AD EB
Main Purpose
DC/DC, Step Down
Outputs And Type
1, Non-Isolated
Voltage - Output
1.8V
Current - Output
600mA
Voltage - Input
2.7 ~ 5.5 V
Regulator Topology
Buck
Frequency - Switching
1.5MHz
Board Type
Fully Populated
Utilized Ic / Part
AS1324-AD
Lead Free Status / RoHS Status
Lead free by exemption / RoHS compliant by exemption
Power - Output
-
AS1324
Datasheet - A p p l i c a t i o n I n f o r m a t i o n
Figure 25. Single Li-Ion 1.8V/600mA Regulator for Low Output Ripple
9.1 External Component Selection
9.2 Inductor Selection
For most applications the value of the external inductor should be in the range of 2.2 to 6.8µH as the inductor value has a direct effect on the
ripple current. The selected inductor must be rated for its DC resistance and saturation current. The inductor ripple current (ΔI
higher inductance and increases with higher V
In
should be rated higher than the maximum inductor current as calculated with
current will rise above the calculated value during heavy load transients.
Where:
f = Switching Frequency (1.5 MHz typical)
L = Inductor Value
I
Δ
The recommended starting point for setting ripple current is Δ
The DC current rating of the inductor should be at least equal to the maximum load current plus half the ripple current to prevent core saturation.
Thus, a 720mA rated inductor should be sufficient for most applications (600mA + 120mA). A easy and fast approach is to select the inductor
current rating fitting to the maximum switch current limit of the converter.
Note: For highest efficiency, a low DC-resistance inductor is recommended.
Accepting larger values of ripple current allows the use of low inductance values, but results in higher output voltage ripple, greater core losses,
and lower output current capability.
The total losses of the coil have a strong impact on the efficiency of the dc/dc conversion and consist of both the losses in the dc resistance and
the following frequency-dependent components:
www.austriamicrosystems.com/DC-DC_Step-Down/AS1324
Lmax
I
L =
Equation (EQ 2)
Peak to Peak inductor ripple current
= Maximum Inductor current
1. The losses in the core material (magnetic hysteresis loss, especially at high switching frequencies)
2. Additional losses in the conductor from the skin effect (current displacement at high frequencies)
3. Magnetic field losses of the neighboring windings (proximity effect)
4. Radiation losses
2.7 to 4.2V
the maximum inductor current in PWM mode under static load conditions is calculated. The saturation current of the inductor
V
IN
10µF
C
IN
IN
or V
OUT
V
EN
IN
4
1
ΔI
I
.
LMAX
L
AS1324-18
I
L
=
= 240mA (40% of 600mA).
V
=
2
OUT
Revision 1.05
I
GND
OUTMAX
×
1
----------------------- -
–
L
Equation (EQ
3
SW
5
V
V
--------------
+
×
V
OUT
OUT
f
ΔI
------- -
IN
2
L
4.7µH
3). This is recommended because the inductor
C
22µF
OUT
600mA
V
1.8V
OUT
L
) decreases with
11 - 20
(EQ 2)
(EQ 3)