BGA-K3 OKI METCAL, BGA-K3 Datasheet - Page 3
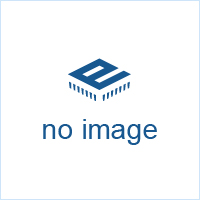
BGA-K3
Manufacturer Part Number
BGA-K3
Description
KIT BGA DEMO BOARD W/BARE PCB
Manufacturer
OKI METCAL
Series
3500r
Datasheet
1.BGA-SPAT-L.pdf
(6 pages)
Specifications of BGA-K3
Accessory Type
BGA Demo Board Kit
For Use With
CSP-C10 - COMP DUMMY BGA FOR BGAK3 KIT(10)
For Use With/related Products
-
Other names
BGAK3
visionary
www.metcal.com
Metcal BGA/CSP Rework Systems
The rework of an array package requires process control and repeatability, to
replicate the original assembly thermal process. When reworking BGA, a greater level
Metcal Vision System
integral vision system for accurate component and stencil alignment. The vision
system utilizes a prism that allows the user to look simultaneously at the topside of
magnification and greater clarity for smaller components with reduced ball pitches.
The vision systems include facilities for either solder paste or flux application to the
rework area — without the need to remove the board from the machine. Consistent
solder paste deposits can be printed using the vision-mounted stencils that allow
accurate alignment and co-planarity adjustment.
I
I
I
Improved ergonomics and simplified controls make using the system easy
and natural for the operator.
Improved vision clarity provides better control of component placement.
Larger pre-heater provides increased power for thermally demanding boards.
the printed circuit board (PCB), and a superimposed image of the
underside of the component.
Using micrometer adjustment, the images can be accurately
aligned in the X, Y & Theta axis, prior to placement. The BGA
3590 incorporates a corner overlay mechanism to facilitate
alignment on large components, while the CSP 3500 offers higher
The BGA-3590 and CSP-3500 both offer an
of process control is required to reduce
the risk of a defect and to ensure the per-
fect result: right first time.
To enhance performance, the newly
redesigned Metcal BGA and CSP Rework
Systems have incorporated new features
that facilitate easier use and improve
process control.
Dip Transfer
with a British university and a major industrial partner. The process involves dipping
the component into a known depth of gel flux, depositing an exact amount onto
each solder ball. The process is quick, consistent, clean, and negates the need for
cleaning after reflow. Both processes have proven successful, even on fine pitch CSP.
Reflow Profiling
technology, both Metcal Rework Systems use low airflow forced
convection heating. The Patented Micro Oven reflow head delivers
temperature uniformity, assuring safe and simultaneous reflow
of the component being removed — without disruption to
adjacent parts.
The systems are fitted with an under-board heater. The CSP
version has a 1000W convection heater suitable for smaller PCBs, while the BGA
version is fitted with a 1400W large area heater with the capacity to work with
thermally demanding multi-layer boards. This eliminates problems associated with
warped boards.
Windows Based Software
controls both heaters, making profile set up simple. Using closed loop
feedback monitoring, the user-friendly software controls the four
stages of the reflow profile: Preheat, Soak, Reflow and Cooling.
The board temperature can be monitored using the integrated flying
thermocouple, and real time adjustments can be made to the times
and temperatures — while the profile is running.
Metcal Soldering System
preparation, all units are supplied with a Metcal MX Direct Power
Soldering System that reduces the risk of track and pad damage
caused by overheating.
Flux dipping is a process pioneered by Metcal in conjunction
As with production reflow oven
innovation
To assist with pad cleaning and
This interactive software precisely
www.metcal.com