LIS344ALH STMicroelectronics, LIS344ALH Datasheet - Page 10
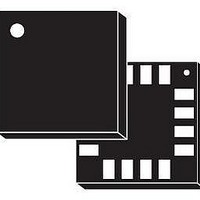
LIS344ALH
Manufacturer Part Number
LIS344ALH
Description
Board Mount Accelerometers MEMS Inertial High Pef 3-Axis
Manufacturer
STMicroelectronics
Datasheet
1.LIS344ALH.pdf
(19 pages)
Specifications of LIS344ALH
Sensing Axis
X, Y, Z
Acceleration
2 g, 6 g
Supply Voltage (max)
3.6 V
Supply Voltage (min)
2.4 V
Supply Current
680 uA
Maximum Operating Temperature
+ 85 C
Minimum Operating Temperature
- 40 C
Shutdown
Yes
Sensitivity
500 mV/g, 15000 mV/g
Package / Case
LGA-16
Output Type
Analog - Voltage
Lead Free Status / RoHS Status
Lead free / RoHS Compliant
Available stocks
Company
Part Number
Manufacturer
Quantity
Price
Part Number:
LIS344ALH
Manufacturer:
ST
Quantity:
20 000
Part Number:
LIS344ALHTR
Manufacturer:
ST
Quantity:
20 000
Mechanical and electrical specifications
2.4
10/19
Terminology
Sensitivity describes the gain of the sensor and can be determined by applying 1g
acceleration to it. As the sensor can measure DC accelerations this can be done easily by
pointing the axis of interest towards the center of the Earth, note the output value, rotate the
sensor by 180 degrees (point to the sky) and note the output value again thus applying ±1g
acceleration to the sensor. Subtracting the larger output value from the smaller one, and
dividing the result by 2, will give the actual sensitivity of the sensor. This value changes very
little over temperature (see sensitivity change vs temperature) and also very little over time.
The Sensitivity tolerance describes the range of sensitivities of a large population of
sensors.
Zero-g level describes the actual output signal if there is no acceleration present. A sensor
in a steady state on a horizontal surface will measure 0 g in X axis and 0 g in Y axis whereas
the Z axis will measure 1g. The output is ideally for a 3.3 V powered sensor Vdd/2 = 1650
mV. A deviation from ideal 0-g level (1650 mV in this case) is called Zero-g offset. Offset of
precise MEMS sensors is to some extend a result of stress to the sensor and therefore the
offset can slightly change after mounting the sensor onto a printed circuit board or exposing
it to extensive mechanical stress. Offset changes little over temperature - see “Zero-g level
change vs temperature” - the Zero-g level of an individual sensor is very stable over lifetime.
The Zero-g level tolerance describes the range of Zero-g levels of a population of sensors.
Self test allows to test the mechanical and electric part of the sensor, allowing the seismic
mass to be moved by means of an electrostatic test-force. The Self Test function is off when
the ST pin is connected to GND. When the ST pin is tied at Vdd an actuation force is applied
to the sensor, simulating a definite input acceleration. In this case the sensor outputs will
exhibit a voltage change in their DC levels which is related to the selected full-scale and
depending on the supply voltage through the device sensitivity. When ST is activated, the
device output level is given by the algebraic sum of the signals produced by the acceleration
acting on the sensor and by the electrostatic test-force. If the output signals change within
the amplitude specified inside
parameters of the interface chip are within the defined specification.
Output impedance describes the resistor inside the output stage of each channel. This
resistor is part of a filter consisting of an external capacitor of at least 1 nF and the internal
resistor. Due to the high resistor level, only small inexpensive external capacitors are
needed to generate low corner frequencies. When interfacing with an ADC it is important to
use high input impedance input circuitries to avoid measurement errors. Note that the
minimum load capacitance forms a corner frequency close to the resonance frequency of
the sensor. In general the smallest possible bandwidth for a particular application should be
chosen to get the best results.
Table
3, then the sensor is working properly and the
LIS344ALH