DK-RV-1.8-TRK-33 austriamicrosystems, DK-RV-1.8-TRK-33 Datasheet - Page 16
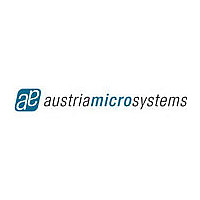
DK-RV-1.8-TRK-33
Manufacturer Part Number
DK-RV-1.8-TRK-33
Description
EVAL KIT SQUIGGLE MOTOR + SENSOR
Manufacturer
austriamicrosystems
Series
SQUIGGLE®, TRACKER™r
Specifications of DK-RV-1.8-TRK-33
Main Purpose
Power Management, Motor Control
Utilized Ic / Part
SQL-RV-1.8-6-12, NSE-5310, MC-3300-RV, NSD-2101
Primary Attributes
Linear Motor, Driver and Position Encoder
Lead Free Status / RoHS Status
Lead free / RoHS Compliant
Embedded
-
Secondary Attributes
-
NSD-2101
Data Sheet - A p p l i c a t i o n I n f o r m a t i o n
Directing the NSD-2101.
The basic command that is sent to the NSD-2101 is the pulse count (with direction). When a non-zero value is written to registers 02 and 03 by
the host microprocessor, the NSD-2101 begins generating pulses on the output pins at the interval defined by the period register (01). For each
pulse, the specified pulse count is decremented. Pulse generation continues until the pulse count reaches zero or the host writes a zero to
registers 02 and 03. See
Since the pulse counter is limited to 2047 (11 bits), the maximum duration of motion is the 2047 x period. If the period were 5.8 µsec (172.4 kHz),
then the duration would be ~11.8 msec. Therefore to produce continuous motion, the pulse count must be reloaded by the host before the
previous pulse count expires (in this case - at least every 11.7 msec - but every 10 msec would provide more margin allowing for variations in
motor frequency and overhead in the host processer handling I²C traffic).
Given the nominal 25MHz power-up frequency of the VCO within the NSD-2101, the motor period is specified in units of 40 nsec. Therefore the
period value necessary to generate a frequency of 172.4 kHz is 145 (or 91 hexadecimal).
As indicated in the previous section, to generate motion, the pulse period must be very near the interval of the mechanical resonant frequency of
the motor. However, for a given motor type, manufacturing tolerances, ambient temperature and mounting have an affect on this resonant
frequency. To cancel out these affects, the NSD-2101 supports a frequency tuning (or calibration) feature.
Therefore on power-up, it is recommended that after an appropriate default period count for the given motor type is loaded, a frequency sweep
calibration is performed followed by an incremental calibration. See
(for a given power cycle); After that, the incremental calibration will keep the motor in tune.
Note: While performing the frequency calibration, the NSD-2101 is adjusting the trimming of its internal VCO to maximize the performance of
Furthermore, it is recommended that frequency calibration be performed in a direction that is against the load (typically forward). The reason is
that, depending on the mass being moved (i.e. the inertia), there may be chatter (intermittent contact between the load and the screw) when
moving with the load. This chatter can affect the calibration.
Starting a frequency sweep calibration (assuming an SQL-RV-1.8 motor):
Starting a frequency incremental calibration:
www.austriamicrosystems.com/NSD-2101
Reg
00
01
02
03
Actual data stream: A8006B9177FF (the host should wait at least 10 msec after start)
Reg
00
01
02
03
Actual data stream: A800679177FF (the host should wait at least 10 msec after start)
the motor (not the period count itself).
Value (hex)
6B
91
77
FF
Value (hex)
67
91
77
FF
Register Map (page 10)
Comment
Enables sweep calibration using both motor phases
172.4 kHz
Fwd, DT=11*, Upper 3 bits of pulse count set
Lower 8 bits of pulse count set
Comment
Enables inc. calibration using both motor phases
172.4 kHz
Fwd, DT=11*, Upper 3 bits of pulse count set
Lower 8 bits of pulse count set
and
Pulse Counter (page
Frequency Tracking (page
Revision 0.4
12).
9). The sweep needs to be performed only once
16 - 22