T183E BANNER ENGINEERING, T183E Datasheet - Page 2
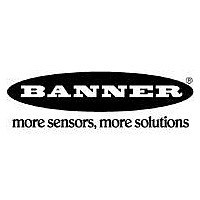
T183E
Manufacturer Part Number
T183E
Description
Photoelectric Sensor
Manufacturer
BANNER ENGINEERING
Type
Opposed Moder
Specifications of T183E
Output Current
300mA
Sensor Input
Optical
Sensing Range Max
20m
Contact Current Max
150mA
Switch Terminals
Cable
Sensing Mode
Opposed
Brand/series
T18
Current, Switching
300 mA
Humidity
90% @ 50 °C (Non-Condensing)
Ip Rating
IP69K
Length, Cable
6.5 ft.
Material, Housing
PBT Polyester
Material, Lens
Polycarbonate⁄Acrylic
Mounting Type
Threaded
Output
SPST
Primary Type
Photoelectric
Range, Measurement
66 mm
Response Time
3 ms (ON), 1.5 ms (OFF)
Standards
CE Mark, CSA Certified, UL Listed
Technology
Photoelectric
Temperature, Operating
-40 to +70 °C
Termination
Cable
Vibration
10 to 60 Hz (Max.)
Voltage, Supply
250 VAC
Lead Free Status / Rohs Status
RoHS Exempt Product
T18 Series self-contained fixed-field sensors are small, powerful, infrared diffuse mode
sensors with far-limit cutoff (a type of background suppression). Their high excess gain
and fixed-field technology allow them to detect objects of low reflectivity, while ignoring
background surfaces.
The cutoff distance is fixed. Backgrounds and background objects must always be placed
beyond the cutoff distance.
Fixed-Field Sensing – Theory of Operation
The T18FF compares the reflections of its emitted light beam (E) from an object back to the
sensor’s two differently aimed detectors, R1 and R2 (see Figure 1). If the near detector (R1)
light signal is stronger than the far detector (R2) light signal (see object A, closer than the
cutoff distance), the sensor responds to the object. If the far detector (R2) light signal is
stronger than the near detector (R1) light signal (see object B, beyond the cutoff distance),
the sensor ignores the object.
The cutoff distance for model T18FF sensors is fixed at 25, 50 or 100 millimeters (1", 2",
or 4"). Objects lying beyond the cutoff distance usually are ignored, even if they are highly
reflective. However, it is possible to falsely detect a background object, under certain
conditions (see Background Reflectivity and Placement).
In the drawings and discussion on these pages, the letters E, R1, and R2 identify how the
sensor’s three optical elements (Emitter “E”, Near Detector “R1”, and Far Detector “R2”)
line up across the face of the sensor. The location of these elements defines the sensing
axis (see Figure 2). The sensing axis becomes important in certain situations, such as those
illustrated in Figures 5 and 6.
Sensing Reliability
For highest sensitivity, position the target object for sensing at or near the point of
maximum excess gain. The excess gain curves for these products are shown on page 5.
They show excess gain vs. sensing distance for sensors with 25 mm, 50 mm, and 100 mm
(1", 2", and 4") cutoffs. Maximum excess gain for the 25 mm models occurs at a lens-to-
object distance of about 7 mm; for 50 mm models, at about 10 mm; and for the 100 mm
models, at about 20 mm. Sensing at or near this distance will make maximum use of
each sensor’s available sensing power. The background must be placed beyond the cutoff
distance. (Note that the reflectivity of the background surface also may affect the cutoff
distance.) Following these two guidelines will improve sensing reliability.
Background Reflectivity and Placement
Avoid mirror-like backgrounds that produce specular reflections. False sensor response will
occur if a background surface reflects the sensor’s light more strongly to the near detector,
or “sensing” detector (R1), than to the far detector, or “cutoff” detector (R2). The result
is a false ON condition (Figure 3). To cure this problem, use a diffusely reflective (matte)
background, or angle either the sensor or the background (in any plane) so the background
does not reflect light back to the sensor (see Figure 4). Position the background as far
beyond the cutoff distance as possible.
An object beyond the cutoff distance, either stationary (and when positioned as shown in
Figure 5), or moving past the face of the sensor in a direction perpendicular to the sensing
axis, can cause unwanted triggering of the sensor if more light is reflected to the near
detector than to the far detector. The problem is easily remedied by rotating the sensor
90° (Figure 6). The object then reflects the R1 and R2 fields equally, resulting in no false
triggering. A better solution, if possible, may be to reposition the object or the sensor.
2
P/N 121525
T18 Sensors – ac-Voltage Series
Fixed-Field Mode Overview
Sensor Setup
Banner Engineering Corp.
www.bannerengineering.com • Tel: 763.544.3164
Figure 1. Fixed-field concept
Figure 2. Fixed-field sensing axis
Detector
Detector
Emitter
As a general rule, the most reliable
sensing of an object approaching from the
side occurs when the line of approach is
parallel to the sensing axis.
Near
Far
Receiver
Elements
R1
R2
E
Object is sensed if amount of light at R1
is greater than the amount of light at R2
Lenses
•
R 1
R 2
Minneapolis, MN U.S.A.
Object
E
A
Sensing
Range
Sensing
Distance
Cutoff
Axis
Background
Object B
or