467MP (12 IN X 60 YD) 3M, 467MP (12 IN X 60 YD) Datasheet - Page 6
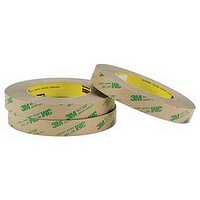
467MP (12 IN X 60 YD)
Manufacturer Part Number
467MP (12 IN X 60 YD)
Description
TAPE, ADHESIVE ACRYLIC CLR/TAN 12INX60YD
Manufacturer
3M
Datasheet
1.467MP_12_IN_X_60_YD.pdf
(8 pages)
Specifications of 467MP (12 IN X 60 YD)
Tape Backing Material
Acrylic
Roll Length
60yard
Features
3M Adhesive 200MP
Tape Type
Graphic/Overlay Attachment
Width
12"
Color
Clear W/Tan Liner
Rohs Compliant
Yes
3M
467MP • 468MP • 467MPF • 468MPF • 7952MP • 7955MP
7962MP • 7965MP • 9172MP • 9185MP • 9667MP • 9668MP
Available
Sizes
Application
Techniques
™
High Performance Adhesive Transfer Tapes with Adhesive 200MP
3M™ Adhesive Transfer Tape 467MP
3M™ Adhesive Transfer Tape 468MP
3M™ Adhesive Transfer Tape 467MPF
3M™ Adhesive Transfer Tape 468MPF
3M™ Adhesive Transfer Tape 7952MP
3M™ Adhesive Transfer Tape 7955MP
3M™ Adhesive Transfer Tape 7962MP
3M™ Adhesive Transfer Tape 7965MP
3M™ Adhesive Transfer Tape 9172MP
3M™ Adhesive Transfer Tape 9185MP
3M™ Adhesive Transfer Tape 9667MP
3M™ Adhesive Transfer Tape 9668MP
9
For maximum bond strength (during installation of the final part) the surface should be thoroughly
cleaned and dried. Typical cleaning solvents are heptane* (for oily surfaces) or isopropyl alcohol*
for plastics. Use reagent grade solvents since common household materials like rubbing alcohol
frequently contain oils to minimize the drying affect on skin and can interfere with the performance
of a pressure-sensitive adhesive.
*Note: Carefully read and follow the manufacturer’s precautions and directions for use when
It is necessary to provide pressure during lamination (1.5-20 pli recommended) and during final
part installation (10-15 psi) to allow the adhesive to come into direct contact with the substrate.
Using a hard edged plastic tool, which is the full width of the laminated part, helps to provide the
necessary pressure at the point of lamination. Heat can increase bond strength when bonding to
metal parts (generally this same increase is observed at room temperature over longer times,
weeks). For plastic parts, the bond strength is not enhanced with the addition of heat.
The ideal adhesive application temperature range is 60°F (15.6°C) to 100°F (38°C). Application is
not recommended if the surface temperature is below 50°F (10°C) because the adhesive becomes
too firm to adhere readily. Once properly applied, at the recommended application temperature,
low temperature holding is generally satisfactory (please refer to section VII of the Typical
Physical Properties and Performance Characteristics).
When bonding a thin, smooth, flexible material to a smooth surface, it is generally acceptable to
use 2 mils of 3M™ Adhesive 200MP. If a texture is visible on one or both surfaces, the 5 mil
3M adhesive 200MP would be suggested. If both materials are rigid, it may be necessary to use a
thicker adhesive to successfully bond the components. 3M™ VHB™ Acrylic Foam Tapes may be
required (please refer to the data page 70-0709-3830-6).
Roll lengths vary by product slit width (the customer service department has more detailed information,
1-800-328-1681).
working with solvents. These cleaning recommendations may not be in compliance with the
rules of certain air quality management districts in California; consult applicable rules
before use.
48", 54"
Master
Size
60"
54"
48"
48"
54"
- 6 -
(minimum)
Slit Width
(100/case)
24" x 36"
sheets
1/2"
1/2"
1"
1"
Roll Length
60-360 yards
60-360 yards
60-360 yards
60-360 yards
If roll form:
360 yards
9
If roll form:
6" cores
Core
Size
3"
3"
3"
3"
Tolerance
If roll form:
± 1/32"
± 1/32"
± 1/32"
± 1/32"
± 1/32"
Slit