MAX17061AEVKIT+ Maxim Integrated Products, MAX17061AEVKIT+ Datasheet - Page 20
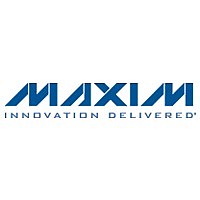
MAX17061AEVKIT+
Manufacturer Part Number
MAX17061AEVKIT+
Description
Power Management Modules & Development Tools MAX17061A EVAL KIT MAX17061A EVAL KIT
Manufacturer
Maxim Integrated Products
Datasheet
1.MAX17061AETI.pdf
(24 pages)
Specifications of MAX17061AEVKIT+
Lead Free Status / RoHS Status
Lead free / RoHS Compliant
The output current capability of the step-up converter is
a function of current limit, input voltage, operating fre-
quency, and inductor value. Because the slope com-
pensation is used to stabilize the feedback loop, the
inductor current limit depends on the duty cycle, and is
determined with the following equation:
where 24.7mV is the scale factor from the slope com-
pensation, 1.9A is a typical current limit at 75% duty
cycle, and D is the duty cycle.
The output current capability depends on the current-
limit value and operating mode. The maximum output
current in CCM is governed by the following equation:
where I
nominal regulator efficiency (85%), and D is the duty
cycle. The corresponding duty cycle for this current is:
where V
diode and R
(0.15Ω typ).
The maximum output current in DCM is governed by
the following equation:
The inductance, peak current rating, series resistance,
and physical size should all be considered when selecting
an inductor. These factors affect the converter’s operating
mode, efficiency, maximum output load capability, tran-
sient response time, output voltage ripple, and cost.
The maximum output current, input voltage, output volt-
age, and switching frequency determine the inductor
value. Very high inductance minimizes the current rip-
ple, and therefore reduces the peak current, which
decreases core losses in the inductor and I
the entire power path. However, large inductor values
also require more energy storage and more turns of
wire, which increases physical size and I
losses. Low inductor values decrease the physical size,
but increase the current ripple and peak current.
8-String White LED Driver with
SMBus for LCD Panel Applications
20
______________________________________________________________________________________
I
OUT DCM MAX
LIM
DIODE
I
OUT CCM MAX
_
is the current limit calculated above,
I
D
LIM
ON
_
is the forward voltage of the rectifier
V
is the internal MOSFET’s on-resistance
(
OUT
1 9
.
(
V
A
OUT
)
I
LIM
)
2
24 7
.
V
L I
I
IN
V
LIM
mV
R
OUT
ON
LIM
Inductor Selection
V
R
DIODE
S
. 0 5
2
0 75
V
V
f
.
OSC
DIODE
DIODE
f
OSC
D V
D
L
IN
2
R losses in
2
V
R copper
IN
is the
Finding the best inductor involves the compromises
among circuit efficiency, inductor size, and cost.
In choosing an inductor, the first step is to determine
the operating mode: continuous conduction mode
(CCM) or discontinuous conduction mode (DCM). The
MAX17061A has a fixed internal slope compensation
that requires minimum inductor value. When CCM
mode is chosen, the ripple current and the peak cur-
rent of the inductor can be minimized. If a small-size
inductor is required, DCM mode can be chosen. In
DCM mode, the inductor value and size can be mini-
mized, but the inductor ripple current and peak current
are higher than those in CCM. The controller can be
stable, independent of the internal slope compensation
mode, but there is a maximum inductor value require-
ment to ensure the DCM operating mode.
The equations used here include a constant LIR, which
is the ratio of the inductor peak-to-peak ripple current
to the average DC inductor current at the full load cur-
rent. The controller operates in DCM mode when LIR is
higher than 2.0, and it works in CCM mode when LIR is
lower than 2.0. The best trade-off between inductor size
and converter efficiency for step-up regulators generally
has an LIR between 0.3 and 0.5. However, depending
on the AC characteristics of the inductor core material
and ratio of inductor resistance to other power-path
resistances, the best LIR can shift up or down. If the
inductor resistance is relatively high, more ripples can
be accepted to reduce the number of required turns and
increase the wire diameter. If the inductor resistance is
relatively low, increasing inductance to lower the peak
current can reduce losses throughout the power path. If
extremely thin high-resistance inductors are used, as is
common for LCD panel applications, LIR higher than 2.0
can be chosen for DCM operating mode.
Once a physical inductor is chosen, higher and lower val-
ues of the inductor should be evaluated for efficiency
improvements in typical operating regions. The detail
design procedure for CCM can be described as follows:
1) Calculate the approximate inductor value using the
typical input voltage (V
rent (I
taken from an appropriate curve in the Typical
Operating Characteristics , and an estimate of LIR
based on the above discussion:
L
Inductor Selection in CCM Operation
OUT(MAX)
V
IN MIN
V
OUT
_
), the expected efficiency (
2
I
OUT MAX
V
OUT
IN
(
), the maximum output cur-
V
IN MIN
)
_
f
OSC
LIR
TYP
TYP
)