MAX16809EVKIT+ Maxim Integrated Products, MAX16809EVKIT+ Datasheet - Page 8
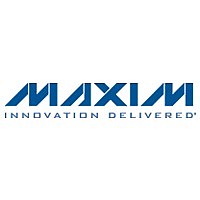
MAX16809EVKIT+
Manufacturer Part Number
MAX16809EVKIT+
Description
Power Management Modules & Development Tools EVAL KIT FOR MAX16809
Manufacturer
Maxim Integrated Products
Datasheet
1.MAX16809EVKIT.pdf
(17 pages)
Specifications of MAX16809EVKIT+
Lead Free Status / RoHS Status
Lead free / RoHS Compliant
MAX16809 Evaluation Kit
calculate the value of R6 to get the required LED sup-
ply voltage during PWM off time:
where 2.5V is the feedback-reference voltage, 0.4V is
the total voltage dropped by D4 and PWM input, and
VLED
PWM off time. VLED
LED string voltage plus some additional headroom for
the LED drivers (0.8V), as well as a reserve voltage
(approximately 1V). The reserve voltage allows the
MAX16809 to provide current for very short PWM dim-
ming on-pulses. With pulses as low as 2µs, the VLED
control loop is not able to react, and the output capaci-
tors provide all the current. For longer PWM dimming
pulses, the control loop reacts and the supply operates
at the adaptive voltage level.
During an open LED condition, the 33V zener diode
(D1) limits the maximum LED supply voltage to 35.5V. If
VLED attempts to increase beyond this level, D1 con-
ducts in reverse direction and pulls the FB pin high,
which causes the boost regulator to cut back on the
PWM signal and reduce the output voltage.
The PWM dimming controls the LED brightness by
adjusting the duty cycle of the PWM input signal. A
high voltage at the PWM input enables the output cur-
rent; a low voltage turns off the output current. Connect
a signal with peak amplitude of 3V to 5V and with fre-
quency from 100Hz to 2kHz to the PWM input and vary
the duty cycle to adjust the LED brightness. The LED
brightness increases when the duty cycle increases
and vice versa. If an inverted PWM signal is available,
use that signal to implement PWM dimming, as shown
in Figure 1.
Like any other circuit with feedback, the boost convert-
er that generates the supply voltage for the LED strings
needs to be compensated for stable control of its out-
put voltage. As the boost converter is operated in con-
tinuous-conduction mode, there exists a right-half-
plane (RHP) zero in the power-circuit transfer function.
This zero adds a 20dB/decade gain together with a 90-
degree phase lag, which is difficult to compensate. The
easiest way to avoid this zero is to roll off the loop gain
8
_______________________________________________________________________________________
OFF
is the desired LED supply voltage during
R6 =
OFF
VLED
R2
Feedback Compensation
should be set to the worst-case
×
(
2.5 - 0.4
OFF
- 2.5
)
PWM Dimming
to 0dB at a frequency less than half of the RHP zero fre-
quency with a -20dB/decade slope. For a boost con-
verter, the worst-case RHP zero frequency (F
given by the following equation:
where D
tance of the inductor, and I
which is the sum of all the LED string currents.
The boost converter used in the MAX16809 EV kit is
operated with current-mode control. There are two
feedback loops within a current-mode-controlled con-
verter: an inner loop that controls the inductor current
and an outer loop that controls the output voltage. The
amplified voltage error produced by the outer voltage
loop is the input to the inner current loop that controls
the peak inductor current.
The internal current loop converts the double-pole 2nd-
order system, formed by the inductor and the output
capacitor C
pole consisting of the output filter capacitor and the out-
put load. As the output load is a constant current (i.e.,
very high Thevenin impedance), this pole is located near
the origin (0Hz). The phase lag created by the output
pole for any frequency will be 90 degrees. Since the
power-circuit DC gain is limited by other factors, the gain
starts falling at -20dB/decade from a non-zero frequency
before which the power-circuit gain stabilizes.
Total gain of the feedback loop at DC is given by the
following equation:
where G
error-amplifier open-loop DC gain, typically 100dB. G
is the gain of the feedback network for adaptive control
of the VLED, which is seen from VLED to the error-
amplifier input (FB pin). The adaptive control senses
the voltages at the 16 constant-current-sink outputs
and adjusts the feedback to control these voltages to a
minimum value (Figure 2). As the LEDs carry constant
current, the voltage across the LEDs does not change
with variations in VLED. Any change in VLED directly
reflects to the constant-current-sink outputs and to the
error-amplifier input, making G
MAX
P
is the power-circuit DC gain, and G
OUT
is the maximum duty cycle, L is the induc-
F
ZRHP
, to a 1st-order system having a single
G
TOT
=
=
G
VLED
P
×
2
G
π
(
1
× ×
O
EA
FB
−
L I
D
is the output current,
×
equal to unity.
MAX
G
O
FB
)
2
EA
ZRHP
is the
) is
FB