EVB-EMC6D103S SMSC, EVB-EMC6D103S Datasheet - Page 6
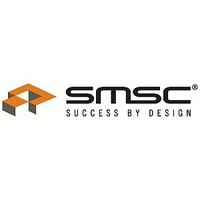
EVB-EMC6D103S
Manufacturer Part Number
EVB-EMC6D103S
Description
MCU, MPU & DSP Development Tools Evaluation Board
Manufacturer
SMSC
Datasheet
1.EVB-EMC6D103S.pdf
(8 pages)
Specifications of EVB-EMC6D103S
Processor To Be Evaluated
EMC6D103S
Interface Type
USB
Lead Free Status / RoHS Status
Lead free / RoHS Compliant
Revision 1.0 (12-14-06)
3.6
3.6.1
3.6.2
3.6.3
Fan#
Fan1
Fan2
Fan3
Fan Drive Circuits
The EMC6D103S has 3 PWM outputs for fan drive. This EVB has 3 different drive circuit types to
demonstrate various popular drive approaches.
characteristics for each fan drive circuit.
Fan1 Drive Circuit
This drive circuit linearizes the PWM output to convert a 0-100% duty cycle PWM signal into a 0-5V
voltage driver. Components R12 and C14 integrate the PWM signal and present 0-3.3V dc to the non-
inverting input of op-amp U4A. The op-amp output drives the gate of power FET Q1. Resistors R13
and R14 provide gain to scale the fan drive signal to a 0-5V range and the location of the feedback
tap compensates for the gate-source voltage required to turn on the drive FET.
Schottky diode D5 is included to clamp back EMF created by the fan and capacitor C15 smooths the
ripple caused by the fan motor switching. The op-amp’s V+ supply is set @ 10Vdc to provide enough
compliance voltage to allow Q1’s gate to be driven to the 7-8Vdc required to drive the source to +5V
to fully turn on the fan.
Note: In general, linear fan drive is audibly quieter than PWM drive because the PWM drive and the
Fan2 Drive Circuit
The Fan2 driver is designed to drive 3 wire, +12Vdc fans. When the PWM2 signal is high, FET Q2 is
ON and full voltage is applied to the fan. When the PWM2 signal is low, Q2 turns off, interrupting power
to the fan by removing the fan’s connection to ground. The frequency of this PWM signal may be set
to various rates from 11 to 87hz and also at 25khz.
Fan2 may be driven by either a +5V or +12V supply. The default setting is +12V; the voltage may be
changed to +5V by de-soldering thermal fuse F3 and re-positioning it at location F2.
Note: PWM control of the power leads of some fans can produce undesirable audible noise.
Fan3 Drive Circuit
The Fan3 circuit drives 4 wire fans that use the PWM signal as a speed control input. 4 wire fans
always have power available to the drive circuit. This results in quiet operation, good speed control
and a tachometer signal that is always valid.
Some 4 wire fans require a pullup to +12V on the PWM signal which would violate the maximum
voltage the PWM3 pin can tolerate so power FET Q5 is included to handle the higher voltage. Q5 may
not be needed for 4 wire fans that can be controlled with a PWM signal in the +3.3 to +5V range. Also,
Q5 can be used to drive the low side of a fan to ground if required.
Linear, 3 Wire
PWM, 3 Wire
PWM, 4 Wire
fan’s motor will interact to set up beat frequencies that can be quite annoying. Most +5V fans
require at least 2V to start up so the usable drive voltage range is about 2.5-5Vdc (50-100%).
PWM drive can generally control a fan over a wider speed range, often as low as 25%.
Disconnecting the low side also corrupts the tachometer signal to the extent that it is not usable
for accurate speed measurement. The tachometer signal may be usable for locked rotor/stall
detection. PWM control of 3 wire fans has the advantage of low cost and wide a speed control
range.
Table 3.1 Fan Drive Circuit Characteristics
Drive Type
12V (+5V Optional)
12V
5V
Voltage
6
Table 3.1
200mA
500mA
500mA
Current (max.)
summarizes the circuit type and
EVB-EMC6D103S User Manual
SMSC EVB-EMC6D103S