ES-FA-6G BANNER ENGINEERING, ES-FA-6G Datasheet - Page 3
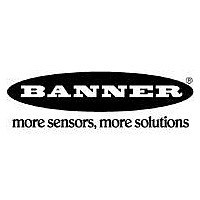
ES-FA-6G
Manufacturer Part Number
ES-FA-6G
Description
ES-FA-6G SINGLE OUTPUT E-STOP
Manufacturer
BANNER ENGINEERING
Datasheet
1.ES-FA-6G.pdf
(12 pages)
Specifications of ES-FA-6G
Relay Mounting
DIN Rail
Peak Reflow Compatible (260 C)
No
Coil Voltage Vdc Nom
24V
External Width
22.5mm
Contact Voltage Ac Nom
250V
External Depth
118.2mm
Coil Voltage Vac Nom
24V
Contact Current Max
6A
Contact Voltage Dc Nom
250V
External Height
82mm
Figure 1. ES-FA-6G status indicators
K1 Energized
K2 Energized
Power On
Input
ES-FA-6G
CH
CH
A1
13
41
14
Power
1
2
Y1
13
14
23
42
24
23
24
The purpose of an Emergency Stop Safety Module (E-Stop Safety Module) is to increase
the control reliability of an emergency stop circuit. The ANSI B11.19 standard states:
In a functional Category 0 emergency stop circuit, opening of the E-stop switch contact(s)
immediately removes power from the machine control elements, which react to arrest
machine hazards. As indicated in Figures 3, 4, and 5, the model ES-FA-6G E-Stop Safety
Module is designed for use with a 1-channel E-stop switch. A 1-channel E-stop switch has
one contact.
The customer-supplied E-stop switch must be a “positive-opening device.” This means
that its contact will open when the actuator is pushed with a certain minimum force,
even if that contact was welded in the closed state.
As shown in Figure 2, the E-stop switch becomes an input to the E-Stop Safety Module.
A short circuit between the two wires which connect the E-stop switch to the E-Stop
Safety Module results in a unsafe condition. To reduce the possibility of a short circuit,
the wires connecting the E-stop switch to the E-Stop Safety Module must be physically
separated from each other and run in separate wireways or conduit.
The output of the E-Stop Safety Module consists of three redundant output switching
channels, each of which is the series connection of two forced-guided relay contacts
(K1 and K2 in Figure 2).
33
34
33
Y2
41
42
A2
34
“Control reliability of electrical, electronic, or pneumatic systems
frequently consists of multiple, independent parallel or series circuitry
or components so arranged that any single failure ... either sends a
stop command to the machine tool or prevents a successive cycle
from being initiated.”
As recommended by the control reliability section of ANSI B11.19, relays
K1 and K2 in the output circuit of the E-Stop Safety Module have
mechanically linked contacts which allow the Safety Module circuitry to
monitor the contacts of K1 and K2 for failure. If the Safety Module detects
failure of any contact of the output relays, the Safety Module output is
disabled and cannot be reset.
The E-Stop Safety Module also provides a necessary reset function. ANSI
B11 and NFPA 79 standards require that a reset routine be performed after
returning the E-stop switch to its closed-contact position. This prevents the
controlled machinery from restarting by simply closing the E-stop switch.
Model ES-FA-6G may be configured for automatic reset by connecting
terminals Y1 and Y2 together (see Figure 2). The automatic reset mode is
useful for some automated processes. However, when automatic reset
is used, an alternate means must be established to require a reset
routine after the E-stop switch is returned to its closed contact position
(see WARNING on page 7).
The three switching output circuits of the E-Stop Safety Module are rated
for up to 250V ac at up to 6 amps. A normally closed non-safety auxiliary
contact (between terminals #41 and 42) provides a monitoring signal for a
process controller. This auxiliary contact is closed when the output circuits
are open, and it is open when the output circuits are closed.
E-Stop Safety Module
E-Stop Safety Module Description
– Model ES-FA-6G
page
3