MIC2179-5.0BSM TR Micrel Inc, MIC2179-5.0BSM TR Datasheet - Page 11
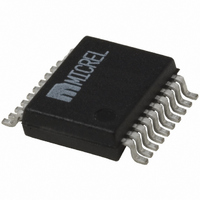
MIC2179-5.0BSM TR
Manufacturer Part Number
MIC2179-5.0BSM TR
Description
1.5A 200kHz Synchronous Switcher In SSOP Pkg
Manufacturer
Micrel Inc
Type
Step-Down (Buck)r
Datasheet
1.MIC2179YSM_TR.pdf
(13 pages)
Specifications of MIC2179-5.0BSM TR
Internal Switch(s)
Yes
Synchronous Rectifier
Yes
Number Of Outputs
1
Voltage - Output
5V
Current - Output
1.5A
Frequency - Switching
200kHz
Voltage - Input
4.5 ~ 16.5 V
Operating Temperature
-40°C ~ 85°C
Mounting Type
Surface Mount
Package / Case
20-SSOP
Lead Free Status / RoHS Status
Contains lead / RoHS non-compliant
Power - Output
-
Lead Free Status / RoHS Status
Contains lead / RoHS non-compliant
Other names
MIC2179-5.0BSMTR
MIC2179-5.0BSMTR
MIC2179-5.0BSMTR
Application Information
Feedback Resistor Selection (Adjustable Version)
The output voltage is programmed by connecting an external
resistive divider to the FB pin as shown in “MIC2179 Block
Diagram.” The ratio of R1 to R2 determines the output voltage.
To optimize efficiency during low output current operation, R2
should not be less than 20kΩ. However, to prevent feedback
error due to input bias current at the FB pin, R2 should not
be greater than 100kΩ. After selecting R2, calculate R1 with
the following formula:
Input Capacitor Selection
The input capacitor is selected for its RMS current and voltage
rating and should be a low ESR (equivalent series resistance)
electrolytic or tantalum capacitor. As a rule of thumb, the
voltage rating for a tantalum capacitor should be twice the
value of V
be 40% higher than V
equal or greater than the maximum RMS input ripple cur-
rent. A simple, worst case formula for calculating this RMS
current is:
Tantalum capacitors are a better choice for applications that
require the most compact layout or operation below 0°C.
The input capacitor must be located very close to the VIN
pin (within 0.2in, 5mm). Also, place a 0.1µF ceramic bypass
capacitor as close as possible to VIN.
Inductor Selection
The MIC2179 is a current-mode controller with internal slope
compensation. As a result, the inductor must be at least a
minimum value to prevent subharmonic oscillations. This
minimum value is calculated by the following formula:
In general, a value at least 20% greater than L
be selected because inductor values have a tolerance of
±20%.
Two other parameters to consider in selecting an inductor
are winding resistance and peak current rating. The inductor
must have a peak current rating equal or greater than the
peak inductor current. Otherwise, the inductor may satu-
rate, causing excessive current in the output switch. Also,
the inductor’s core loss may increase significantly. Both of
these effects will degrade efficiency. The formula for peak
inductor current is:
Where:
June 2009
R1 = R2
L
I
∆I
I
L(peak)
RMS(max)
MIN
L(max)
IN
= V
, and the voltage rating for an electrolytic should
= I
= V
OUT
=
((
LOAD(max)
OUT
1.245V
x 3.0 µH/V
I
LOAD(max)
V
OUT
(
2
1 -
IN.
+
)
V
The RMS current rating must be
∆I
V
IN(max)
-1
OUT
L(max)
2
)
)
x
L • f
1
MIN
should
11
To maximize efficiency, the inductor’s resistance must
be less than the output switch on-resistance (preferably,
50mΩ or less).
Output Capacitor Selection
Select an output capacitor that has a low value of ESR.
This parameter determines a regulator’s output ripple volt-
age (V
ESR must be equal or less than a maximum value calculated
for a specified V
voltage) and ∆I
Typically, capacitors in the range of 100 to 220µF have ESR
less than this maximum value. The output capacitor can be
a low ESR electrolytic or tantalum capacitor, but tantalum is
a better choice for compact layout and operation at tempera-
tures below 0°C. The voltage rating of a tantalum capacitor
must be 2 × V
must be 1.4 × V
Output Diode Selection
In PWM operation, inductor current flows through the output
diode approximately 50ns during the dead time when one
output MOSFET turns off the other turns on. In skip mode,
the inductor current flows through the diode during the entire
P-channel off time. The correct diode for both of these condi-
tions is a 1A diode with a reverse voltage rating greater than
V
(t
reverse-recovery charge.
Compensation
Compensation is provided by connecting a series RC load
to the COMP pin. This creates a pole-zero pair in the regu-
lator control loop, allowing the regulator to remain stable
with enough low frequency loop-gain for good load and line
regulation. At higher frequencies, the pole-zero reduces
loop-gain to a level referred to as the mid-band gain. The
mid-band gain is low enough so that the loop gain crosses
0db with sufficient phase margin. Typical values for the RC
load are 4.7nF to 10nF for the capacitor and 5kΩ to 20kΩ
for the resistor.
Printed Circuit Board Layout
A well designed PC board will prevent switching noise and
ground bounce from interfering with the operation of the
MIC2179. A good design takes into consideration component
placement and routing of power traces.
The first thing to consider is the locations of the input ca-
pacitor, inductor, output diode, and output capacitor. The
input capacitor must be placed very close to the VIN pin,
the inductor and output diode very close to the SW pin, and
the output capacitor near the inductor. These components
pass large high-frequency current pulses, so they must use
short, wide power traces. In addition, their ground pins and
PGND are connected to a ground plane that is nearest the
power supply ground bus.
R
IN
. It must be a schottky or ultrafast-recovery diode
< 100ns) to minimize power dissipation from the diode’s
ESR
RIPPLE
MAX
) which is generated by ∆I
OUT
=
L(max)
OUT
RIPPLE
V
∆I
, and the voltage rating of an electrolytic
RIPPLE
L(max)
.
:
(typically less than 1% of the output
L
× ESR. Therefore,
M9999-063009