MAX1887EEE Maxim Integrated Products, MAX1887EEE Datasheet - Page 19
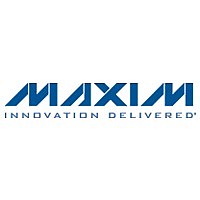
MAX1887EEE
Manufacturer Part Number
MAX1887EEE
Description
Current Mode PWM Controllers
Manufacturer
Maxim Integrated Products
Specifications of MAX1887EEE
Number Of Outputs
1
Mounting Style
SMD/SMT
Package / Case
QSOP-16
Switching Frequency
550 KHz
Maximum Operating Temperature
+ 85 C
Minimum Operating Temperature
- 40 C
Synchronous Pin
No
Topology
Boost
Available stocks
Company
Part Number
Manufacturer
Quantity
Price
Company:
Part Number:
MAX1887EEE
Manufacturer:
MAXIM
Quantity:
6 237
Part Number:
MAX1887EEE
Manufacturer:
MAXIM/美信
Quantity:
20 000
in MOSFET technology that are making higher frequen-
cies more practical.
Setting Switch On Time: The constant on-time control
algorithm in the master results in a nearly constant
switching frequency despite the lack of a fixed-frequen-
cy clock generator. In the slave, the high-side switch on
time is inversely proportional to V+ and directly propor-
tional to the compensation voltage (V
where K is internally preset to 3.3µs for the MAX1887 or
externally set by the TON pin-strap connection for the
MAX1897 (Table 3)
Set the nominal on time in the slave to match the on
time in the master. An exact match is not necessary
because the MAX1887/MAX1897 have wide t
ment ranges (±40%). For example, if t
is set to 250kHz, the slave can be set to either 200kHz
or 300kHz and still achieve good performance. Care
should be taken to ensure that the COMP voltage
remains within its output voltage range (0.42V to
2.80V).
Inductor Operating Point: This choice provides trade-
offs between size vs. efficiency and transient response
vs. output noise. Low inductor values provide better
transient response and smaller physical size, but also
result in lower efficiency and higher output noise due to
increased ripple current. The minimum practical induc-
tor value is one that causes the circuit to operate at the
edge of critical conduction (where the inductor current
just touches zero with every cycle at maximum load).
Inductor values lower than this grant no further size-
reduction benefit. The optimum operating point is usu-
ally found between 20% and 50% ripple current.
The switching frequency and operating point (% ripple
or LIR) determine the inductor value as follows:
where
I
30% ripple current or LIR = 0.3:
LOAD
= 40A, V
η
L
is the number of phases. Example:
L
=
=
12
V xf
1 3
V x
IN
.
IN
V
V x
OUT
t
______________________________________________________________________________________
300
= 12V, V
ON
SW
(
12
kHz x
x V
=
xI
(
V
K
LOAD MAX
IN
−
1 3
V
40
OUT
−
.
COMP
V
V
V x
(
A x
IN
OUT
)
Inductor Selection
= 1.3V, f
0 3
2
.
)
)
x
xLIR
η
=
COMP
Quick-PWM Slave Controllers for
Multiphase, Step-Down Supplies
0 64
ON
.
SW
in the master
):
µ
H
= 300kHz,
ON
adjust-
η
= 2,
Find a low-loss inductor having the lowest possible DC
resistance that fits in the allotted dimensions. Ferrite
cores are often the best choice, although powdered
iron is inexpensive and can work well at 200kHz. The
core must be large enough not to saturate at the peak
inductor current (I
where
The inductor ripple current affects transient-response
performance, especially at low V
Low inductor values allow the inductor current to slew
faster, replenishing charge removed from the output fil-
ter capacitors by a sudden load step. The amount of
output sag also is a function of the maximum duty fac-
tor, which can be calculated from the on time and mini-
mum off time:
where t
Electrical Characteristics section),
phases, and K is from Table 3.
The amount of overshoot due to stored inductor energy
can be calculated as:
The master and slave current-limit thresholds must be
great enough to support the maximum load current,
even under worst-case operating conditions. Since the
master’s current limit determines the maximum load
(see the Current-Limit Circuitry section), the procedure
for setting the current limit is sequential. First, the mas-
ter’s current limit is set based on the operating condi-
tions and the characteristics of the low-side MOSFETs.
Then the slave controller is configured to adjust the
master’s current-limit threshold based on the precise
current-sense resistor value and variation in the MOS-
FET characteristics. Finally, the resulting valley current
limit for the slave’s inductor occurs above the master’s
V
SAG
η
=
OFF(MIN)
is the number of phases.
2η
L I
I
PEAK
(
C
∆
V
OUT OUT
SOAR
LOAD MAX
PEAK
V
=
is the minimum off time (see the
I
(
LOAD MAX
≈
Setting the Current Limits
):
(
∆
2η
I
)
LOAD MAX
(
)
(
V
2
C
IN
OUT OUT
Transient Response
−
)
V
(
V
V
OUT
IN
V
2
OUT
IN
V
IN
+
2η
)
- V
LIR
K
η
)
)
2
+
K
is the number of
OUT
L
t
−
OFF MIN
t
OFF MIN
differentials.
(
(
)
)
19