SI-MAG2SM W/30 BANNER ENGINEERING, SI-MAG2SM W/30 Datasheet - Page 3
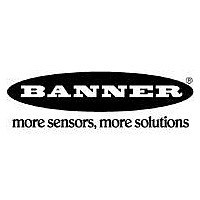
SI-MAG2SM W/30
Manufacturer Part Number
SI-MAG2SM W/30
Description
Switch, Safety, Magnet Sensor, 30' Cable(Used w/SI-MAG2MM Magnet, GM-FA-10J Ctrl)
Manufacturer
BANNER ENGINEERING
Datasheet
1.SI-MAG1SM_W30.pdf
(8 pages)
Specifications of SI-MAG2SM W/30
Actuator Type
Magnet
Brand/series
SI-MAG
Function
Safety
Ip Rating
IP67
Number Of Poles
1
Number Of Positions
2
Operation
On-Off
Range, Measurement
8 mm
Special Features
4-8 mm Distance
Technology
Reed
Termination
Cable
Voltage, Switching
30 VDC
Lead Free Status / Rohs Status
RoHS Exempt Product
opening) before hazardous machine
motion has completely stopped. Please
reference OSHA CFR 1910.217 and ANSI
B11 standards (see page 2) for
information on determining safety
distances and safe opening sizes for
your guarding devices.
!
Banner Engineering Corp.
www.bannerengineering.com • Tel: 763.544.3164
WARNING!
It must not be possible for
personnel to reach any
hazard point through an
opened guard (or any
•
Minneapolis, MN U.S.A.
Magnetic style safety switches are easily mounted on the inside edge of most guards.
Inside mounting can often hide them from view and discourage tampering.
All mounting hardware is supplied by the user. Use of permanent fasteners or locking
hardware is recommended to prevent loosening or displacement of the actuator and
switch body. Mounting holes in the magnet and sensor accept M4 (#6) hardware (see
drawings, on page 8).
Position the magnet and sensor in the mounting location with the magnet surface
directly opposite the sensing surface (see dimension drawings). Leave a slight gap (up
to 3 mm or 0.12") between the magnet and sensor surfaces, so that the magnet and
sensor do not act as an end stop when the guard is closed. Mark the mounting holes.
Fasten the magnet and sensor in place. After the mounting hardware is secure, check
the magnet and sensor alignment and sensing gap. Neither is critical, but the gap
should be less than 3 mm (0.12") for reliable sensor actuation.
Route the sensor cable to the controller location. The controller must be installed
inside an enclosure. It is not designed for exposed wiring. It is the user’s responsibility
to house the controller in an enclosure with NEMA (or IEC) rating which is suitable for
the operating environment. The controller mounts onto standard 35 mm DIN rail.
Note: The typical direction of approach of a magnet to its corresponding sensor is
normally perpendicular to the sensing face and the magnet surface (see dimensional
drawings on page 8 and Figures 2a, 2b and 2c, “Direction of Approach on page 6).
Alternate directions are possible (e.g., sideways or parallel), though the speed of
approach must be fast enough to meet the simultaneity-monitoring period of 0.5
seconds. This speed is approximately equal to or greater than 0.2 m (8"/s). If the
simultaneity is not met, the MAG1C controller will not close its safety output contacts,
even if the “sensor” indicator is OFF.
IMPORTANT NOTE: If the sensor or magnet is mounted on a material that can be
magnetized (e.g., ferrous metal, such as iron), the switching distance will be affected.
The sensor and magnet must be mounted a minimum distance of 15 mm (0.6") from
magnetized or ferrous materials for proper operation.
IMPORTANT NOTE: The magnet and sensor are coded to minimize the possibility of
false actuation. Nevertheless, they should not be used within known fields of high-
level electromagnetic radiation. The magnet and sensor must never be used as a
mechanical stop.
Each controller is powered by 24V dc (at less than 100 mA). The controller, in turn,
supplies power to the sensor.
As illustrated in Figure 1, the safety output (terminals 71 and 76) from each of two
safety switches per interlock guard must connect to a 2-channel safety module or
safety interface in order to achieve a control reliable interface to the master stop control
elements of a machine. Examples of appropriate safety modules include 2-channel
emergency stop (E-stop) safety modules and gate monitor safety modules.
Two functions of the safety module or safety interface are:
1) to provide a means of monitoring the contacts of both safety switches for contact
failure, and to prevent the machine from restarting if either switch fails;
Machine Safety Switches –
Sensor and Magnet Installation
Electrical Installation
Magnet Style
page
3