IRADK10PBF International Rectifier, IRADK10PBF Datasheet - Page 5
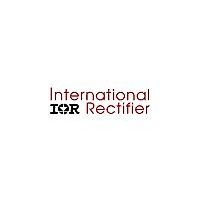
IRADK10PBF
Manufacturer Part Number
IRADK10PBF
Description
Manufacturer
International Rectifier
Datasheet
1.IRADK10PBF.pdf
(11 pages)
Specifications of IRADK10PBF
Lead Free Status / Rohs Status
Compliant
PWM phase command signals
This carries the signals as shown below. Note that these
signals are referenced to the negative DC power rail which
is not at ground potential. Beware of electric shock haz-
ard and do not connect any grounded test equipment
such as an oscilloscope to these test pins.
Pin 1: Phase A upper switch ON command, inverted
Pin 2: Phase B upper switch ON command, inverted
Pin 3: Phase C upper switch ON command, inverted
Pin 4: Phase A lower switch ON command, inverted
Pin 5: Phase B lower switch ON command, inverted
Pin 6: Phase C lower switch ON command, inverted
Pin 7: ITRIP signal
Pin 8: SP1 spare digital input
Pin 9: SP2 spare digital input
Pin 10: GROUND (0V) referred to - DC bus
Pin 11: Spare analog input referred to -DC bus rail
Pin 12: +5V auxiliary power supply referred to - DC bus
High voltage signals J2
This connector J2 carries the motor drive voltages and the
DC bus voltage. Use the same cautions as referenced
above for the PWM phase command signals.
Pin 1: Phase A motor voltage
Pin 3: Phase B motor voltage
Pin 5: Phase C motor voltage
Pin 7: MINUS DC bus rail
Pin 10: PLUS DC bus rail
Power Connector J1
Power connector provides the input AC power and the
motor connections.
Pin 1: Input AC voltage (115V or 220V) phase
Pin 2: Input AC voltage (115V or 220V) neutral
Pin 3: Ground connection ( has to be connected to
Pin 4: Ground connection
Pin 5: Phase C motor connection
Pin 6: Phase B motor connection
Pin 7: Phase A motor connection
110V/220V selector switch S3
S3 is the selector switch to set the correct rectifier configu-
ration to the AC input.. Prior to connecting the system to the
AC input, carefully check the position of S3. Operate the
switch only when the AC is OFF. The drive will be dam-
aged and the user could be injured by ignoring this warning.
www.irf.com
reduce the EMI noise)
rail
Use a 3-phase 115V Y connected or 220V delta connected
induction
Provide a 3 wire, 2A minimum rated cable for the motor con-
nection, and a 3 wire 2A minimum rated cable for the AC
mains connections. Make sure you also attach the ground
connection. The motor phase connections can be connected
in any sequence, only the rotation direction will be affected.
Make all the necessary connections, including the serial link
with the PC before applying AC power.
Operating the motor via the GUI tool.
After connecting all the cables and selecting the desired
settings in the GUI, apply the AC power via S2 in position 1.
After a few seconds, provided the main voltage is within tol-
erances, the yellow LED diode will flash denoting the pres-
ence of the DC-bus voltage.
Start the GUI tool. The first screen will prompt you for the
COM port used for PC to DEMO board communication as
is showed in the figure 4. Select either COM1 or COM2 for
this purpose.
This will lead you to the next screen. Observe at the top-left
a white field with the “DRIVE STATUS” label. Pressing the
“REFRESH SCREEN” button will read the drive status (ON,
OFF, eventual SC, OV, UV, I2T, and heat sink over tempera-
ture) and print a message in the top-left white field. Below
the “DRIVE STATUS” field, another white field is observed
with the caption “DC-link current average value over 5 sec-
onds”. Pressing the “REFRESH SCREEN” button will read
the drive DC-link current averaged over 5 seconds and dis-
play the value in mA units. Further below, in the same far left
column, another white field is observed with the caption “Heat
sink temperature”. Pressing the “REFRESH SCREEN” but-
ton will read the drive heat sink temperature and display the
value in degrees Centigrade.
Connecting the inverter to the motor.
motor
Figure 4. GUI serial connection selections
rated
at
IRADK10
½
HP
or
less.
5