M27C512-10C1 STMicroelectronics, M27C512-10C1 Datasheet - Page 6
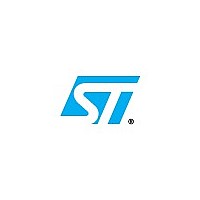
M27C512-10C1
Manufacturer Part Number
M27C512-10C1
Description
Manufacturer
STMicroelectronics
Datasheet
1.M27C512-10C1.pdf
(22 pages)
Specifications of M27C512-10C1
Density
512Kb
Organization
64Kx8
Interface Type
Parallel
Bus Type
Parallel
In System Programmable
External
Access Time (max)
100ns
Package Type
PLCC
Reprogramming Technique
OTP
Operating Supply Voltage (typ)
5V
Operating Supply Voltage (min)
4.5V
Operating Supply Voltage (max)
5.5V
Supply Current
50mA
Pin Count
32
Mounting
Surface Mount
Operating Temp Range
0C to 70C
Operating Temperature Classification
Commercial
Lead Free Status / Rohs Status
Not Compliant
Available stocks
Company
Part Number
Manufacturer
Quantity
Price
Company:
Part Number:
M27C512-10C1
Manufacturer:
PL
Quantity:
101
Part Number:
M27C512-10C1
Manufacturer:
ST
Quantity:
20 000
Device operation
2.3
2.4
6/22
Two line output control
Because EPROMs are usually used in larger memory arrays, the product features a 2 line
control function which accommodates the use of multiple memory connection. The two line
control function allows:
For the most efficient use of these two control lines, E should be decoded and used as the
primary device selecting function, while G should be made a common connection to all
devices in the array and connected to the READ line from the system control bus. This
ensures that all deselected memory devices are in their low power standby mode and that
the output pins are only active when data is required from a particular memory device.
System considerations
The power switching characteristics of Advanced CMOS EPROMs require careful
decoupling of the devices. The supply current, I
the system designer: the standby current level, the active current level, and transient current
peaks that are produced by the falling and rising edges of E. The magnitude of the transient
current peaks is dependent on the capacitive and inductive loading of the device at the
output. The associated transient voltage peaks can be suppressed by complying with the
two line output control and by properly selected decoupling capacitors. It is recommended
that a 0.1µF ceramic capacitor be used on every device between V
be a high frequency capacitor of low inherent inductance and should be placed as close to
the device as possible. In addition, a 4.7µF bulk electrolytic capacitor should be used
between V
power supply connection point.The purpose of the bulk capacitor is to overcome the voltage
drop caused by the inductive effects of PCB traces.
The lowest possible memory power dissipation,
Complete assurance that output bus contention will not occur.
CC
and V
SS
for every eight devices. The bulk capacitor should be located near the
CC
, has three segments that are of interest to
CC
and V
SS
. This should
M27C512