MAX4554 Maxim, MAX4554 Datasheet - Page 15
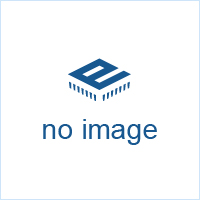
MAX4554
Manufacturer Part Number
MAX4554
Description
The MAX4554/MAX4555/MAX4556 are CMOS analog ICs configured as force-sense switches for Kelvin sensing in automated test equipment (ATE)
Manufacturer
Maxim
Datasheet
1.MAX4554.pdf
(28 pages)
Available stocks
Company
Part Number
Manufacturer
Quantity
Price
Part Number:
MAX4554CSE
Manufacturer:
MAXIM/美信
Quantity:
20 000
Company:
Part Number:
MAX4554CSE+
Manufacturer:
Maxim Integrated Products
Quantity:
135
Company:
Part Number:
MAX4554CSE+
Manufacturer:
MAX
Quantity:
50
When measuring a precise voltage from a high-resis-
tance source, or when measuring a very small current
or forcing it into a load, unwanted leakage currents can
degrade the results. These leakage currents may exist
in the insulation of wires connecting the source and the
measuring device. Higher source voltages, higher
source impedances, longer wires, lower currents, and
higher temperatures further degrade the measurement.
The effect has both DC and low-frequency AC compo-
nents; AC signals are generally capacitively coupled
into the high-impedance source and wiring. The AC
and DC effects are hard to separate, and are generally
grouped under the designation “low-frequency noise.”
This signal degradation can be overcome and the mea-
sured signal guaranteed by using a 3-wire technique
known as guarding.
A “guard,” “guard channel,” or “driven guard” is formed
by adding a third wire to a 2-wire measurement. It con-
sists of a physical barrier (generally the surrounding
shield of a coaxial cable) that is actively forced to the
same voltage as is being measured on its inner conduc-
tor. The forcing of the driven guard is from the output of
a low-impedance buffer amplifier whose high-imped-
ance input is connected to the source. The idea is not
just to buffer or shield the signal with a low-impedance
source but, by forcing the shield to the same potential
as the signal, to also force the leakage currents
between the signal and the outside world to extremely
small values. Any unwanted leakage current from the
source must first go through the coaxial-cable insulation
to the shield. Since the shield is at the same potential,
there is virtually no unwanted leakage current, regard-
less of the insulation resistance. The shield itself can
have significant leakage currents to the outside world,
but it is separated from the measured signal.
The physical positioning of the guard around the signal
is extremely important in maintaining low leakage.
Since the guard can be at potentials far from ground,
conventional coaxial cable is often replaced by triaxial
cable (i.e., cable with a center conductor and two sep-
arate inner and outer shields). The signal is the center
conductor, the inner shield is the guard, and the outer
shield is the chassis ground. The outer shield isolates
the inner driven guard from ground, physically protects
the driven guard, and acts as a secondary Faraday
shield for external noise.
The physical guard must be maintained continuously
from the source to the measuring device, including
paths on printed circuit boards, where the guard
becomes extra traces surrounding the signal traces on
both sides (and above and below the signal traces on
__________________Guard Philosophy
______________________________________________________________________________________
multilevel boards.) This is one case where a ground
plane is not appropriate. In extreme cases, such as
with nano-voltmeters and femto-ammeters, printed cir-
cuit boards cannot be adequately shielded and are
eliminated from the guarded signal paths altogether.
Figure 2 shows both the basic 3-wire guarded mea-
surement and a 5-wire variation, used for balanced sig-
nals that are elevated from ground potential. The 5-wire
configuration is really two 3-wire circuits sharing a com-
mon ground. Figure 2 also shows the configuration
using triaxial cable.
Force-sense measurements are combined with guard-
ed measurements when a wide range of voltages and
currents are encountered, or when voltage and current
must be accurately measured or controlled simultane-
ously. This frequently occurs in automatic test equip-
ment (ATE) and in some critical physical or chemical
sensor applications where voltage and/or current mea-
surements can span many decades. Two techniques
are used: 8-wire and 12-wire.
Figure 3 shows an 8-wire guarded force-sense power
supply. A precise voltage is forced to the load, and
load current is sensed without interacting with the out-
put voltage, and without unwanted leakage currents.
Separate twin-axial, or “twinax” cable is used for each
of the positive and negative wires. Each cable has a
twisted-pair of wires surrounded by a common shield,
which is connected as the driven guard. Since the
force and sense wires are at approximately the same
potential, they can be protected by the same driven
guard. In critical applications, two special 4-wire cables
and connectors are substituted for the two twinax
cables and separate ground wire. These cables add a
second shield, which replaces the chassis-to-chassis
ground wire and reduces noise.
Figure 3 shows current sensing with a fixed precision
resistor and voltmeter, but other methods (such as op
amps with feedback) are frequently employed, particu-
larly if current limiting is required. One of the advantages
of Figure 3’s circuit is that leakage in the current-sensing
path has no effect on the output voltage.
The two diodes in the force-sense feedback path pro-
tect the force-sense amplifier from operating open loop
if either the force or sense wires are disconnected from
the load. These diodes must have both lower forward
voltage and lower reverse leakage than the current
being measured.
____Force-Sense-Guard Philosophy
Force-Sense Switches
8-Wire Measurements
15