NCP1212 ON Semiconductor, NCP1212 Datasheet
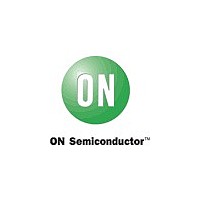
NCP1212
Available stocks
Related parts for NCP1212
NCP1212 Summary of contents
Page 1
... Current Mode PWM Controller for Both Forward and Flyback Converters NCP1212 is a high performance current mode PWM controller specifically designed for off−line and DC−to−DC converter applications. The device requires very few external components and offers designer additional protection for better system reliability. The ...
Page 2
... NCP1212 Figure 1. Typical Application Circuit http://onsemi.com 2 ...
Page 3
... NCP1212 CLK Figure 2. Simplified Functional Block Diagram http://onsemi.com 3 CLK ...
Page 4
... Machine Model (MM) v200 V per JEDEC standard: JESD22−A115. 2. Latchup Current Maximum Rating: "150 mA per JEDEC standard: JESD78. NCP1212 Á Á Á Á Á Á Á Á Á Á Á Á Á Á Á Á Á Á Á Á Á Á Á Á Á Á Á Á Á Á Á Á Á Á Á Á Á Á Á Á Á Á Á Á ...
Page 5
... V) DMAX Maximum Duty Cycle at Soft−Start Pin Voltage Higher than 3 3 DMAX internal current source not accessible externally The output voltage is internally clamped by 13.5 V Zener. NCP1212 = 25°C, DMAX = 48%, for min/max values 1.0 nF 1.0 nF 1.0 V DRV = 5.0 V (Note 4) DRV ° ...
Page 6
... Figure 5. Frequency Change against Supply Voltage vs. Junction Temperature 200 160 120 − JUNCTION TEMPERATURE (°C) J Figure 7. Propagation Delay vs. Junction Temperature NCP1212 TYPICAL CHARACTERISTICS 100 DMAX = 48 105 −25 Figure 4. Oscillator Frequency with 82% Duty Cycle vs. Junction Temperature 1 ...
Page 7
... Figure 11. 82% Duty Cycle Selection Input Voltage Threshold vs. Junction Temperature 350 300 250 200 150 100 DRV 50 − JUNCTION TEMPERATURE (°C) J Figure 13. Gate Drive Source Capability vs. Junction Temperature NCP1212 105 −25 Figure 10. Overload Timing Discharge Current 1.2 1.1 1 0.9 0.8 0.7 79 105 − ...
Page 8
... Figure 17. Brownout Input Threshold Voltage vs. Junction Temperature 60 2.1V ≤ − JUNCTION TEMPERATURE (°C) J Figure 19. Maximum Duty Cycle, DMAX Junction Temperature NCP1212 105 − Figure 16. Gate Drive Voltage Fall Time vs ...
Page 9
... JUNCTION TEMPERATURE (°C) J Figure 23. V Startup Threshold Voltage vs. CC Junction Temperature 5.0 4.0 3.0 2.0 1.0 0.0 − JUNCTION TEMPERATURE (°C) J Figure 25. Power Supply Operating Current vs. Junction Temperature NCP1212 105 − JUNCTION TEMPERATURE (°C) J Figure 22. V vs. Junction Temperature 200 150 100 50 0 ...
Page 10
... SUPPLY VOLTAGE (V) CC Figure 29. Supply Current vs. Supply Voltage (Duty Cycle = 82% and Output Load = 1 nF) 300 250 200 150 100 50 0 400 Figure 31. Switch Frequency vs. C NCP1212 Figure 28. Fall Time of Gate Drive Waveform 4 Ramp 3.5 Ramp down from 2.5 2 1.5 1 0.5 0 −0.5 ...
Page 11
... C shown in Figure 32. Figure 32. C PWM Latch Section NCP1212 works in current mode. The power switch current is converted to a positive voltage by inserting a sensing resistor R the ground. The power switch peak current is compared with the level shifted control input voltage on a cycle−by−cycle basis ...
Page 12
... In normal operation, voltage developed at the current sense input is compared with the level shifted control input voltage and an internal Current Limit Threshold, V case the CS input exceeds the Current Limit Threshold, which is 1.0 V (typ.) in NCP1212, the gate driver output will be forced to turn off immediately. F/F Overload ...
Page 13
... Overload shutdown is no longer bothered by leakage spike hence a reliable overload protection system can be easily constructed by NCP1212 for both forward and fly−back configuration. Overload detection block is shown in Figure 38. Overload condition is signified by current sense voltage hitting the maximum SS allowable voltage, 1 ...
Page 14
... V − Brownout Protection NCP1212 has a built−in comparator for brownout detection as shown in Figure 39. Positive terminal of the comparator is connected to a +1.21 V bandgap reference. The IC is prohibited from switching until Brownout Detect pin exceeds 1.21 V. Once the brownout detect threshold is exceeded flows out of the pin and the voltage at this pin is further pushed up to provide hysteresis effect ...
Page 15
... UVLO threshold. If the fault condition CC persists, NCP1212 will enter hi−cup operation. In case system latchoff is required in fault conditions, a smaller startup resistance can be used to sustain the device operation. NCP1212 will remain in shutdown mode as long as V maintained above UVLO threshold after fault is detected. http://onsemi.com 15 Brownout Shutdown reaches 15 V ...
Page 16
... APPLICATION INFORMATION AND TYPICAL WAVEFORMS The NCP1212 is an ideal choice for next generation isolated fix switching frequency forward mode converters that only need few external components to complete the system. Converting your existing application from using UC384X controllers to NCP1212 is easy and simple. In below is a description on how to determine external components value for a typical application example ...
Page 17
... Duty Cycle and 3.8 V for 82% Maximum Duty Cycle. The Switching Frequency against C Figure 31 to help the designers to determine the capacitance for their selected switching frequency. NCP1212 discharging, The discharging waveform on SS/DMAX pin is shown in SS Figure 41. The discharging time from 4 0 measured from Figure 41. By interpolation, discharging time can be estimated as about 41 ...
Page 18
... At light load or no load conditions, the primary current is very small and as the current NCP1212 Switching Waveform DS Figure 42. Brownout Detect Waveforms sensing resistor is also small for high power applications, the current sense feedback voltage will be much smaller than 0 ...
Page 19
... Figure 43. Suggested Solution for Better Light Load Regulation The skip mode operation waveform at light load is shown in Figure 44. Where Channel 1 is the gate drive pin waveform and Channel 2 is the CS input pin waveform. Figure 44. Skip Mode Switching Waveform at Light Load NCP1212 3 R − Output ...
Page 20
... H D 0.25 (0.010 *For additional information on our Pb−Free strategy and soldering details, please download the ON Semiconductor Soldering and Mounting Techniques Reference Manual, SOLDERRM/D. NCP1212 PACKAGE DIMENSIONS SOIC−8 D SUFFIX CASE 751−07 ISSUE ...
Page 21
... F −A− NOTE 2 C −T− N SEATING PLANE 0.13 (0.005) M NCP1212 PACKAGE DIMENSIONS PDIP−8 N SUFFIX CASE 626−05 ISSUE http://onsemi.com 21 NOTES: 1. DIMENSION L TO CENTER OF LEAD WHEN FORMED PARALLEL. 2. PACKAGE CONTOUR OPTIONAL (ROUND OR SQUARE CORNERS) ...
Page 22
... The product described herein (NCP1212), may be covered by one or more of the following U.S. patents: 6,385,060, 6,385,061, and 6,271,735. There may be other patents pending. ON Semiconductor and are registered trademarks of Semiconductor Components Industries, LLC (SCILLC). SCILLC reserves the right to make changes without further notice to any products herein. SCILLC makes no warranty, representation or guarantee regarding the suitability of its products for any particular purpose, nor does SCILLC assume any liability arising out of the application or use of any product or circuit, and specifically disclaims any and all liability, including without limitation special, consequential or incidental damages. “ ...