NJU39610 New Japan Radio, NJU39610 Datasheet - Page 9
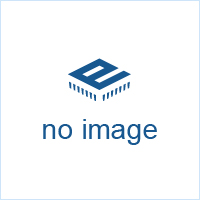
NJU39610
Manufacturer Part Number
NJU39610
Description
MICROSTEPPING MOTOR CONTROLLER WITH DUAL DAC
Manufacturer
New Japan Radio
Datasheet
1.NJU39610.pdf
(11 pages)
Available stocks
Company
Part Number
Manufacturer
Quantity
Price
Part Number:
NJU39610D2
Manufacturer:
JRC
Quantity:
20 000
Company:
Part Number:
NJU39610D2-#ZZZB
Manufacturer:
ST
Quantity:
6 700
Company:
Part Number:
NJU39610FM2
Manufacturer:
NJR
Quantity:
907
Company:
Part Number:
NJU39610FM2
Manufacturer:
CONEXANT
Quantity:
120
Part Number:
NJU39610FM2
Manufacturer:
JRC
Quantity:
20 000
Part Number:
NJU39610FN2
Manufacturer:
PBL
Quantity:
20 000
How Many Microsteps?
The number of true microsteps that can be obtained depends upon many different variables, such as the number of
data bits in the Digital-to-Analog converter, errors in the converter, acceptable torque ripple, single- or double-pulse
programming, the motor’s electrical, mechanical and magnetic characteristics, etc. Many limits can be found in the
motor’s ability to perform properly; overcome friction, repeatability, torque linearity, etc. It is important to realize that
the number of current levels, 128 (2
(reference voltage levels) available from each driver stage. Combining a current level in one winding with any of
128 other current levels in the other winding will make up 128 current levels. So expanding this, it is possible to get
16,384 (128 • 128) combinations of different current levels in the two windings. Remember that these 16,384 micro-
positions are not all useful, the torque will vary from 100% to 0% and some of the options will make up the same
position. For instance, if the current level in one winding is OFF (0%) you can still vary the current in the other
winding in 128 levels. All of these combinations will give you the same position but a varying torque.
Typical Application
The microstepper solution can be used in a system with or without a micro-processor.
Without a microprocessor, a counter addresses a ROM where appropriate step data is stored. Step and Direction
are the input signals which represent clock and up / down of counter. This is the ideal solution for a system where
there is no microprocessor or it is heavily loaded with other tasks.
With a microprocessor, data is stored in ROM / RAM area or each step is successively calculated. NJU39610 is
connected like any peripheral addressable device. All parts of stepping can be tailored for specific damping needs
etc. This is the ideal solution for a system where there is an available microprocessor with extra capacity and low
cost is more essential than simplicity. See typical application, figure 14.
Never disconnect ICs or PC Boards when power is supplied.
better stepping performance even if the motor is not rated for the V
will take care of it. A normal stepper motor might give satisfactory result, but while microstepping, a “microstepping-
adapted” motor is recommended. This type of motor has smoother motion due to two major differences, the stator /
rotor teeth relationship is non-equal and the static torque is lower.
stepping, half stepping, full stepping, and wave drive.
Fast or Slow Current Decay?
There is a difference between static and dynamic operation of which the actual application must decide upon when
to use fast or slow current decay. Generally slow decay is used when stepping at slow speeds. This will give the
benefits of low current ripple in the drive stage, a precise and high overall average current, and normal current
increase on the positive edge of the sine-cosine curves. Fast current decay is used at higher speeds to avoid
current dragging with lost positions and incorrect step angles as a result.
Ramping
Every drive system has inertia which must be considered in the drive system. The rotor and load inertia play a big
role at higher speeds. Unlike the DC motor, the stepper motor is a synchronous motor and does not change its
speed due to load variations. Examining a typical stepper motor’s torque-versus-speed curve indicates a sharp
torque drop-off for the “start-stop without error” curve. The reason for this is that the torque requirements increase
by the cube of the speed change. For good motor performance, controlled acceleration and deceleration should be
considered even though microstepping will improve overall performance.
Choose a motor that is rated for the current you need to establish desired torque. A high supply voltage will gain
The NJU39610 can handle programs which generate microsteps at a desired resolution as well as quarter
APPLICATIONS INFORMATION
User Hints
7
), is not the number of steps available. 128 is the number of current levels
MM
voltage, the current regulation in NJM3771
NJU39610