TC110 Microchip Technology, TC110 Datasheet - Page 6
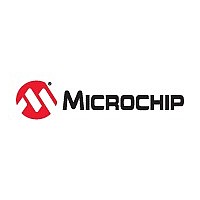
TC110
Manufacturer Part Number
TC110
Description
PFM/PWM Step-Up DC/DC Controller
Manufacturer
Microchip Technology
Datasheet
1.TC110.pdf
(16 pages)
Available stocks
Company
Part Number
Manufacturer
Quantity
Price
Company:
Part Number:
TC1101
Manufacturer:
Transcom
Quantity:
5 000
Company:
Part Number:
TC1101V
Manufacturer:
Eudyna
Quantity:
5 000
Company:
Part Number:
TC1102
Manufacturer:
M/A-COM
Quantity:
5 000
Part Number:
TC110301ECT
Manufacturer:
MICROCHIP/微芯
Quantity:
20 000
Company:
Part Number:
TC110301ECTTR
Manufacturer:
MICROCHIP
Quantity:
12 000
Part Number:
TC110303ECT
Manufacturer:
MICROCHIP/微芯
Quantity:
20 000
Part Number:
TC110303ECTTR
Manufacturer:
MICROCHIP/微芯
Quantity:
20 000
Part Number:
TC110331ECT
Manufacturer:
MICROCHIP/微芯
Quantity:
20 000
Part Number:
TC110333ECT
Manufacturer:
MICROCHIP/微芯
Quantity:
20 000
Company:
Part Number:
TC110333ECTTR
Manufacturer:
MICROCHIP
Quantity:
12 000
TC110
3.5
The effective series resistance of the output capacitor
directly affects the amplitude of the output voltage
ripple. (The product of the peak inductor current and
the ESR determines output ripple amplitude.) There-
fore, a capacitor with the lowest possible ESR should
be selected. Smaller capacitors are acceptable for light
loads or in applications where ripple is not a concern.
The Sprague 595D series of tantalum capacitors are
among the smallest of all low ESR surface mount
capacitors
components and suppliers.
3.6
Selecting the proper inductor value is a trade-off
between physical size and power conversion require-
ments. Lower value inductors cost less, but result in
higher ripple current and core losses. They are also
more prone to saturate since the coil current ramps
faster and could overshoot the desired peak value. This
not only reduces efficiency, but could also cause the
current rating of the external components to be
exceeded. Larger inductor values reduce both ripple
current and core losses, but are larger in physical size
and tend to increase the start-up time slightly.
A 22µH inductor is recommended for the 300kHz
versions and a 47µH inductor is recommended for the
100kHz versions. Inductors with a ferrite core (or
equivalent) are also recommended. For highest
efficiency, use inductors with a low DC resistance (less
than 20 mΩ).
The inductor value directly affects the output ripple
voltage. Equation 3-3 is derived as shown below, and
can be used to calculate an inductor value, given the
required output ripple voltage and output capacitor
series resistance:
EQUATION 3-1:
where ESR is the equivalent series resistance of the
output filter capacitor, and V
Expressing di in terms of switch ON resistance and
time:
EQUATION 3-2:
Solving for L:
EQUATION 3-3:
DS21355B-page 6
Output Capacitor
Inductor Selection
V
RIPPLE
available.
L
≈
V
RIPPLE
≈
ESR [(V
ESR [(V
Table 4-1
≈ ESR(di)
V
IN
RIPPLE
RIPPLE
IN
– V
L
– V
SW
is in volts.
SW
)t
lists
ON
)t
ON
]
]
suggested
Care must be taken to ensure the inductor can handle
peak switching currents, which can be several times
load currents. Exceeding rated peak current will result
in core saturation and loss of inductance. The inductor
should be selected to withstand currents greater than
I
Calculating the peak inductor current is straightforward.
Inductor current consists of an AC (sawtooth) current
centered on an average DC current (i.e., input current).
Equation 3-6 calculates the average DC current. Note
that minimum input voltage and maximum load current
values should be used:
EQUATION 3-4:
Re-writing in terms of input and output currents and
voltages:
EQUATION 3-5:
Solving for input curent:
EQUATION 3-6:
The sawtooth current is centered on the DC current
level; swinging equally above and below the DC current
calculated in Equation 3-6. The peak inductor current is
the sum of the DC current plus half the AC current.
Note that minimum input voltage should be used when
calculating the AC inductor current (Equation 3-9).
EQUATION 3-7:
EQUATION 3-8:
EQUATION 3-9:
where: V
switch is used substitute V
Combining the DC current calculated in Equation 3-6,
with half the peak AC current calculated in Equation 3-
9, the peak inductor current is given by:
EQUATION 3-10:
PK
(Equation 3-10) without saturating.
(V
SW
IN
Input Power
MIN
= V
I
IN
di =
) (I
MAX
I
CESAT
PK
IN
=
MAX
[(V
= I
di
V
) =
IN
(V
(Efficiency)(V
of the switch (note if a CMOS
©
IN
=
MIN
=
=
OUT
MAX
2002 Microchip Technology Inc.
(V
CESAT
V(dt)
– V
Output Power
OUT
L(di)
L
MAX
+ 0.5(di)
dt
dt
Efficiency
SW
Efficiency
)(I
MAX
for r
)t
OUT
) (I
ON
IN
DS
MAX
MAX
]
OUT
ON
)
)
x I
MAX
IN
)
)