TDA1400 Tripath Technology, TDA1400 Datasheet - Page 15
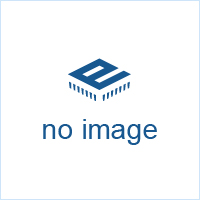
TDA1400
Manufacturer Part Number
TDA1400
Description
MONO CLASS-T DIGITAL AUDIO AMPLIFIER DRIVER
Manufacturer
Tripath Technology
Datasheet
1.TDA1400.pdf
(25 pages)
www.DataSheet4U.com
Some components are not sensitive to location but are very sensitive to layout and trace routing.
TDA1400 Grounding
Proper grounding techniques are required to maximize TDA1400 functionality and performance.
Parametric parameters such as THD+N, Noise Floor and Crosstalk can be adversely affected if proper
grounding techniques are not implemented on the PCB layout. The following discussion highlights some
recommendations about grounding both with respect to the TDA1400 as well as general “audio system”
design rules.
The TDA1400 is divided into three sections: the input processor section, the FET driver section, and the
complementary output MOSFETs (high voltage) section. On the RB_TDA1400 evaluation board, the
ground is also divided into distinct sections, Analog Ground (AGND) and Power Ground (PGND). To
minimize ground loops and keep the audio noise floor as low as possible, the two grounds must be only
connected at a single point.
The ground for the 5V supply is referred to as the analog ground and must be connected to pins 5, 41
and 42 on the TDA1400. Additionally, any external input circuitry such as preamps, or active filters,
should be referenced to the pins 41 and 42.
For the power section, Tripath has traditionally used a “star” grounding scheme, though a solid ground
plane is also effective and used on the RB-TDA1400. Any type of shield or chassis connection would be
15
-
-
-
-
-
-
-
MOSFET or from the source of the p-channel MOSFET to the drain of the n-channel MOSFET.
The output over/undershoots are very high-speed transients. If these diodes are placed too far
away from the MOSFETs, they will be ineffective.
To minimize noise pickup and minimize THD+N, R
close to the TDA1400 as possible. Make sure that the routing of the high voltage feedback
lines is kept far away from the input op amps or significant noise coupling may occur.
The main supply decoupling capacitors, C
and Q
capacitors, C
For proper over-current detection, the sense lines connected to RS must be kelvin connected
directly from the terminals of R
(OCSN_NEG). The traces should be run in parallel back to the TDA1400 pins without
deviation. Improper layout with respect to R
to additional IR losses.
To maximize the damping factor and reduce distortion and noise, the modulator feedback
connections should be routed directly to the pins of the output inductors. L
The output filter capacitor, C
PGND.
The feedback signals that come directly from the output inductors are high voltage and high
frequency in nature. If they are routed close to the input nodes, INV_AMP, the high impedance
inverting op-amp pin will pick up noise. This coupling will result in significant background noise,
especially when the input is AC coupled to ground. Thus, care should be taken such that the
feedback lines are not routed near any of the input section.
To minimize the possibility of any noise pickup, the trace lengths of IINV_AMP should be kept
as short as possible. This is most easily accomplished by locating the input resistors, R
the input stage feedback resistors, R
offset trim resistor, R
TDA1400 input section.
P
. These will absorb energy when D
S
, will shunt energy generated by the main supply lead trace inductance.
OFB
, which connects to either INV_AMP, should be located close to the
O
, and zobel capacitor, C
S
back to OCSP_POS (OCSP_NEG) and OCSN_POS
F
as close to the TDA1400 as possible. In addition, the
SD
S
, should be located close to the output devices, Q
S
and D
will result in premature over-current detection due
T r i p a t h T e c h n o l o g y , I n c . - P r e l i m i n a r y I n f o r m a t i o n
FBA
DS
conduct. Also, the bulk decoupling
, R
Z
, should be star connected back to
FBB
, and R
T D A 1 4 0 0 – R e v . 0 . 6 5 / K L i / 0 2 . 0 6
FBC
should be located as
O
.
I
and
N