AN1627 Freescale Semiconductor / Motorola, AN1627 Datasheet - Page 16
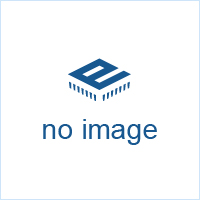
AN1627
Manufacturer Part Number
AN1627
Description
Low Cost High Efficiency Sensorless Drive for Brushless dc Motor Using MC68HC (7)05MC4
Manufacturer
Freescale Semiconductor / Motorola
Datasheet
1.AN1627.pdf
(28 pages)
The following formula is then used to evaluate if
if (((Rising edge is expected) AND (TCAP2 pin is Hi)) OR ((Falling edge is expected) AND (TCAP2 pin
is Lo))) then
if (((Rising edge is expected) AND (TCAP2 pin is Lo)) OR ((Falling edge is expected) AND (TCAP2 pin
is Hi))) then
All three cases (
counters) during one revolution (18 commutations per revolution). The results are then used in the PLL
Controller.
The stall detection is performed using another formula:
if (EMF_Lo>Stall limit) then call Emergency Service routine.
5.2.3.1
Based on above counters values the PLL Controller changes PWM duty cycle (PWMA and PWMB
registers)
if (EMF_OK>6) then stay with the same PWM duty cycle
The PLL Controller can be more sophisticated for other applications (the time window can be divided
into several subintervals etc.). In any case some kind of statistical evaluation is strongly recommended.
If the current is higher, then the alignment of electrical and magnetic fields should be adjusted. The
best
Explanation: When load torque is increased, the phase current is also increased automatically and the
fly-back diodes are open for a longer time. Thus the time window (when zero crossing can be sensed)
is shrunk. This reduction can be so big that the time window becomes less than 30° long (also
If the previously explained control algorithm is applied, then the switching angle is increased so that the
alignment of electrical and magnetic fields is improved (see Figure 2-3., Figure 2-4. and Figure 2-5.).
5.2.4
5.2.4.1
This routines turns OFF all PWM outputs and waits. After some time the drive tries to start again
(optional).
5.2.4.2
The result from an A/D conversion of either the Speed Setting or the DC-Bus voltage is stored into
memory. The successive A/D channel is selected and an A/D conversion is started.
5.2.4.3
The Current controller subroutine is called every 512
based on the required and measured values of the DC-Bus current. The result from the PI controller is
a scaled value of the duty cycle which is directly used by the PWM registers.
5.2.4.4
The values for the PWM control registers and the MUX command are found in look-up tables. The MUX
command is a three bit word which controls the multiplexer (MUX). The multiplexer handles the phase
MOTOROLA
16
is no longer 90° but higher. The used algorithm does this improvement automatically.
PLL Controller
Subroutines
Emergency Stop Subroutine
Speed Setting & DC-Bus Voltage Measurement
Current Controller Subroutine
Commutation Subroutine
> 180°
< 90°
< 90°,
else if (EMF_Lo
90°<
Freescale Semiconductor, Inc.
For More Information On This Product,
< 180° and
Go to: www.freescale.com
E MF_Hi)
> 180°) are counted (by EMF_Lo, EMF_OK and EMF_Hi
NOTE
< 90° or
then decrease PWM duty cycle
else increase PWM duty cycle
s . The PI controller calculates the PWM value
> 180°:
REV 0.2
AN1627
> 90°).