LTC3731 Linear Technology, LTC3731 Datasheet - Page 13
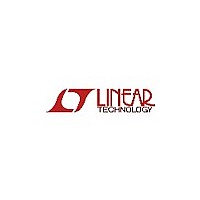
LTC3731
Manufacturer Part Number
LTC3731
Description
Synchronous Buck Switching Regulator Controller
Manufacturer
Linear Technology
Datasheet
1.LTC3731.pdf
(32 pages)
Available stocks
Company
Part Number
Manufacturer
Quantity
Price
Part Number:
LTC3731CG
Manufacturer:
LINEAR/凌特
Quantity:
20 000
Part Number:
LTC3731CG#PBF
Manufacturer:
LINEAR/凌特
Quantity:
20 000
Part Number:
LTC3731CG-AE
Manufacturer:
LINEAR/凌特
Quantity:
20 000
Company:
Part Number:
LTC3731CUH
Manufacturer:
Linear Technology
Quantity:
135
Company:
Part Number:
LTC3731CUH
Manufacturer:
LT
Quantity:
10 000
Part Number:
LTC3731CUH
Manufacturer:
LINEAR/凌特
Quantity:
20 000
Part Number:
LTC3731CUH#PBF
Manufacturer:
LINEAR/凌特
Quantity:
20 000
Company:
Part Number:
LTC3731HUH
Manufacturer:
LT
Quantity:
10 000
Company:
Part Number:
LTC3731HUH#PBF/C
Manufacturer:
MAX
Quantity:
753
Company:
Part Number:
LTC3731IUH
Manufacturer:
LT
Quantity:
10 000
www.DataSheet4U.com
APPLICATIO S I FOR ATIO
current and low current operation must also be consid-
ered. The PolyPhase approach reduces both input and
output ripple currents while optimizing individual output
stages to run at a lower fundamental frequency, enhancing
efficiency.
The inductor value has a direct effect on ripple current. The
inductor ripple current ∆I
decreases with higher inductance or frequency and in-
creases with higher V
where f is the individual output stage operating frequency.
In a PolyPhase converter, the net ripple current seen by the
output capacitor is much smaller than the individual
inductor ripple currents due to the ripple cancellation. The
details on how to calculate the net output ripple current
can be found in Application Note 77.
Figure 4 shows the net ripple current seen by the output
capacitors for the different phase configurations. The
output ripple current is plotted for a fixed output voltage as
the duty factor is varied between 10% and 90% on the
x-axis. The output ripple current is normalized against the
inductor ripple current at zero duty factor. The graph can
be used in place of tedious calculations. As shown in
Figure 4, the zero output ripple current is obtained when:
So the number of phases used can be selected to minimize
the output ripple current and therefore the output ripple
voltage at the given input and output voltages. In applica-
tions having a highly varying input voltage, additional
phases will produce the best results.
Accepting larger values of ∆I
inductances but can result in higher output voltage ripple.
A reasonable starting point for setting ripple current is
∆I
I
∆I
inductor ripple currents are constant determined by the
inductor, input and output voltages.
OUT
L
L
∆I
V
= 0.4(I
occurs at the maximum input voltage. The individual
V
OUT
L
is the total load current. Remember, the maximum
IN
=
V
=
OUT
OUT
fL
N
k
)/N, where N is the number of channels and
⎛
⎜
⎝
where k
1
−
U
V
V
OUT
IN
IN
or V
= 1 2
⎞
⎟
⎠
U
, , ..., –
L
OUT
per individual section, N,
L
:
allows the use of low
N
W
1
U
Kool Mµ is a registered trademark of Magnetics, Inc.
Inductor Core Selection
Once the value for L1 to L3 is determined, the type of
inductor must be selected. High efficiency converters
generally cannot afford the core loss found in low cost
powdered iron cores, forcing the use of ferrite, molyper-
malloy or Kool Mµ
of core size for a fixed inductor value, but it is very
dependent on inductance selected. As inductance in-
creases, core losses go down. Unfortunately, increased
inductance requires more turns of wire and therefore
copper losses will increase.
Ferrite designs have very low core loss and are preferred
at high switching frequencies, so design goals can
concentrate on copper loss and preventing saturation.
Ferrite core material saturates “hard,” which means that
inductance collapses abruptly when the peak design
current is exceeded. This results in an abrupt increase in
inductor ripple current and consequent output voltage
ripple. Do not allow the core to saturate!
Molypermalloy (from Magnetics, Inc.) is a very good, low
loss core material for toroids, but it is more expensive than
ferrite. A reasonable compromise from the same manu-
facturer is Kool Mµ. Toroids are very space efficient,
especially when you can use several layers of wire. Be-
cause they lack a bobbin, mounting is more difficult.
However, designs for surface mount are available which
do not increase the height significantly.
Figure 4. Normalized Peak Output Current
vs Duty Factor [I
1.0
0.9
0.8
0.7
0.6
0.5
0.4
0.3
0.2
0.1
0
0.1
0.2
®
cores. Actual core loss is independent
0.3
DUTY FACTOR (V
0.4
RMS
0.5
= 0.3(I
OUT
0.6
/V
O(P-P)
IN
0.7
1-PHASE
2-PHASE
3-PHASE
4-PHASE
6-PHASE
12-PHASE
)
]
0.8
3731 F04
LTC3731
0.9
13
3731fa