ltc1709eg-trpbf Linear Technology Corporation, ltc1709eg-trpbf Datasheet - Page 14
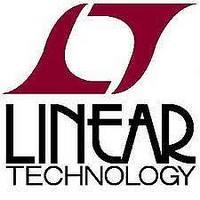
ltc1709eg-trpbf
Manufacturer Part Number
ltc1709eg-trpbf
Description
2-phase, 5-bit Adjustable,high Efficiency, Synchronous Step-down Switching Regulator
Manufacturer
Linear Technology Corporation
Datasheet
1.LTC1709EG-TRPBF.pdf
(28 pages)
APPLICATIO S I FOR ATIO
LTC1709
of the bottom MOSFET from turning on, storing charge
during the dead-time, and requiring a reverse recovery
period which would reduce efficiency. A 1A to 3A Schottky
(depending on output current) diode is generally a good
compromise for both regions of operation due to the
relatively small average current. Larger diodes result in
additional transition losses due to their larger junction
capacitance.
C
In continuous mode, the source current of each top
N-channel MOSFET is a square wave of duty cycle V
V
RMS current must be used. The details of a closed form
equation can be found in Application Note 77. Figure 4
shows the input capacitor ripple current for a 2-phase
configuration with the output voltage fixed and input
voltage varied. The input ripple current is normalized
against the DC output current. The graph can be used in
place of tedious calculations. The minimum input ripple
current can be achieved when the input voltage is twice the
output voltage
In the graph of Figure 4, the 2-phase local maximum input
RMS capacitor currents are reached when:
where k = 1, 2.
14
IN
IN
. A low ESR input capacitor sized for the maximum
V
and C
V
OUT
IN
Figure 4. Normalized RMS Input Ripple Current vs
Duty Factor for 1 and 2 Output Stages
OUT
2
k
Selection
4
0.6
0.5
0.4
0.3
0.2
0.1
0
0.1
1
U
0.2
0.3
DUTY FACTOR (V
U
0.4
1-PHASE
2-PHASE
0.5
OUT
0.6
W
/V
IN
0.7
)
0.8
1709 F04
0.9
U
OUT
/
These worst-case conditions are commonly used for
design because even significant deviations do not offer
much relief. Note that capacitor manufacturer’s ripple
current ratings are often based on only 2000 hours of life.
This makes it advisable to further derate the capacitor, or
to choose a capacitor rated at a higher temperature than
required. Several capacitors may also be paralleled to
meet size or height requirements in the design. Always
consult the capacitor manufacturer if there is any
question.
It is important to note that the efficiency loss is propor-
tional to the input RMS current squared and therefore a
2-phase implementation results in 75% less power loss
when compared to a single phase design. Battery/input
protection fuse resistance (if used), PC board trace and
connector resistance losses are also reduced by the re-
duction of the input ripple current in a 2-phase system. The
required amount of input capacitance is further reduced by
the factor, 2, due to the effective increase in the frequency
of the current pulses.
The selection of C
series resistance (ESR). Typically once the ESR require-
ment has been met, the RMS current rating generally far
exceeds the I
output ripple ( V
Where f = operating frequency of each stage, C
output capacitance and I
ripple currents.
The output ripple varies with input voltage since I
function of input voltage. The output ripple will be less than
50mV at max V
The emergence of very low ESR capacitors in small,
surface mount packages makes very physically small
implementations possible. The ability to externally com-
pensate the switching regulator loop using the I
LOOP compensation) allows a much wider selection of
C
C
OUT
OUT
V
OUT
required ESR < 4(R
> 1/(16f)(R
RIPPLE(P-P)
I
RIPPLE
IN
OUT
with I
OUT
SENSE
) is determined by:
is driven by the required effective
ESR
)
requirements. The steady state
L
= 0.4I
SENSE
RIPPLE
16
fC
OUT(MAX)
) and
1
OUT
= combined inductor
/2 assuming:
TH
pin(OPTI-
OUT
L
is a
=