lb11610p Sanyo Semiconductor Corporation, lb11610p Datasheet - Page 11
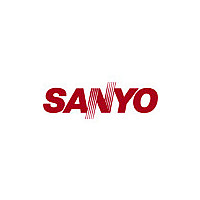
lb11610p
Manufacturer Part Number
lb11610p
Description
Three-phase Brushless Motor Driver
Manufacturer
Sanyo Semiconductor Corporation
Datasheet
1.LB11610P.pdf
(18 pages)
LB11610 Operation Description
(1) PWMRE Circuit
(2) Low-voltage protection circuit
(3) Thermal protection circuit
(4) Forward/reverse operation
(5) Motor constraint protection circuit
At V CC power supply startup, a reset period created by a resistor and capacitor connected to the PWMRE pin is set up
(the outputs are turned off for the CSD pin rapid charge time). This is to prevent incorrect operation of the motor
constraint protection circuit when the motor is stopped (in particular, to prevent the motor constraint protection circuit
from operating immediately since the CSD pin voltage is low) by assuring that the CSD pin voltage is reliably set high
(which requires waiting for the capacitor charge time). The outputs are set to the off state in the reset period, the period
until the PWMRE pin voltage due to the PWMRE pin charge current and capacitor/resistor reaches 1.25V (typical).
The LB11610P switches to normal operating mode when the PWMRE potential exceeds 1.25V (typical), and the
outputs will be once again set to the off state (reset state) if the PWMRE potential falls to under 0.55V (typical).
The LB11610P outputs operate when the PWMRE potential is over 1.25V (typical) and the CSD pin potential is over
0.76 × V CC (3.8V typical when V CC is 5V).
The following equation is used to set the PWMRE reset time (Treset).
Treset = -RC×ln{1-V O /(Ipwmre×R)}
PWMRE reset time setup example
When V CC = 5V, PWMRE: C = 0.068µF, R = 220kΩ:
This IC starts up (output operation turns on) when the V CC voltage is 4.3V (typical) or higher and stops (output
operation is turned off) when the V CC voltage falls below 3.8V (typical).
If the junction temperature (Tj) exceeds a stipulated level (TSD = 180°C, typical), the outputs are turned off.
This IC is designed assuming that the forward/reverse (F/R) direction will not be switched while the motor is turning.
We recommend that the F/R pin be held fixed at either high (forward) or low (reverse) during use.
Although this pin will go to the high level due to an internal pull-up resistor (about 50kΩ) if left open, this pull-up
operation should be strengthened with an external resistor or other means if there large fluctuations in voltage or
current levels during IC operation.
The LB11610P includes a built-in motor constraint protection circuit to protect the IC itself and the motor if the motor
is physically constrained from moving. If the Hall sensor input signals do not switch states for a period in excess of a
certain fixed time with the motor in the driven state, the outputs are turned off. This time is set by the discharge time of
the capacitor and resistor connected to the CSD pin.
The rotation detection pulse signal is detected with the timing of the falling edge (high to low) of the FG signal.
This rotation pulse detection signal time is set by the discharge time of the capacitor connected to the CSDEG pin.
The charge current is supplied to the CSD pin during the rotation detection pulse signal time.
When the motor is constrained and the CSD potential discharges to under 0.6V, the outputs are turned off.
After motor constraint protection circuit operation, the outputs are latched in the off state.
Either of the following operations must be performed to release this latched state.
Ipwmre: PWMRE pin charge current − 200µA (typical)
VO: The PWMRE initial potential − 0V
C: The PWMRE pin external capacitor
R: The PWMRE pin external resistor (It is desirable that this resistor value be 30kΩ or higher.)
• Set the IC to the reset state by setting the CTL pin voltage to under 1V and the PWMRE potential to under 0.55V
(typical).
Treset = -RC×ln{1-VO/(Ipwmre×R)}
= -220kΩ × 0.068μF × ln{1-1.25/(200μA × 220kΩ)}
≅ 431μ(s)
LB11610P
No.A0345-11/18