LTC1878 LINER [Linear Technology], LTC1878 Datasheet - Page 8
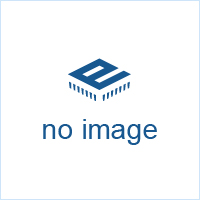
LTC1878
Manufacturer Part Number
LTC1878
Description
High Efficiency Monolithic Synchronous Step-Down Regulator
Manufacturer
LINER [Linear Technology]
Datasheet
1.LTC1878.pdf
(16 pages)
Available stocks
Company
Part Number
Manufacturer
Quantity
Price
Company:
Part Number:
LTC1878EMS8
Manufacturer:
LT
Quantity:
5 321
Company:
Part Number:
LTC1878EMS8#TR
Manufacturer:
LT
Quantity:
3 000
Part Number:
LTC1878EMS8#TRPBF
Manufacturer:
LT/凌特
Quantity:
20 000
OPERATIO
APPLICATIO S I FOR ATIO
LTC1878
Dropout Operation
When the input supply voltage decreases toward the
output voltage, the duty cycle increases toward the maxi-
mum on-time. Further reduction of the supply voltage
forces the main switch to remain on for more than one
cycle until it reaches 100% duty cycle. The output voltage
will then be determined by the input voltage minus the
voltage drop across the internal P-channel MOSFET and
the inductor.
Low Supply Operation
The LTC1878 is designed to operate down to an input
supply voltage of 2.65V although the maximum allowable
output current is reduced at this low voltage. Figure 1
shows the reduction in the maximum output current as a
function of input voltage for various output voltages.
The basic LTC1878 application circuit is shown on the first
page. External component selection is driven by the load
requirement and begins with the selection of L followed by
C
Inductor Value Calculation
The inductor selection will depend on the operating fre-
quency of the LTC1878. The internal nominal frequency is
550kHz, but can be externally synchronized from 400kHz
to 700kHz.
8
IN
and C
Figure 1. Maximum Output Current vs Input Voltage
1200
1000
OUT
800
600
400
200
0
2.5
.
L = 10 H
V
OUT
U
V
3.5
= 1.5V
OUT
U
= 2.5V
INPUT VOLTAGE (V)
4.5
U
V
OUT
5.5
= 3.3V
W
6.5
1878 F01
7.5
U
Another important detail to remember is that at low input
supply voltages, the R
increases. Therefore, the user should calculate the power
dissipation when the LTC1878 is used at 100% duty cycle
with a low input voltage (see Thermal Considerations in
the Applications Information section).
Slope Compensation and Inductor Peak Current
Slope compensation provides stability in constant fre-
quency architectures by preventing subharmonic oscilla-
tions at high duty cycles. It is accomplished internally by
adding a compensating ramp to the inductor current
signal at duty cycles in excess of 40%. As a result, the
maximum inductor peak current is reduced for duty cycles
> 40%. This is shown in the decrease of the inductor peak
current as a function of duty cycle graph in Figure 2.
The operating frequency and inductor selection are inter-
related in that higher operating frequencies allow the use
of smaller inductor and capacitor values. However, oper-
ating at a higher frequency generally results in lower
efficiency because of increased internal gate charge losses.
The inductor value has a direct effect on ripple current. The
ripple current I
frequency and increases with higher V
Figure 2. Maximum Inductor Peak Current vs Duty Cycle
1100
1000
900
800
700
600
0
V
IN
= 3.3V
L
20
decreases with higher inductance or
DUTY CYCLE (%)
DS(ON)
40
60
of the P-channel switch
80
IN
1878 F02
or V
100
OUT
.