AD598 Analog Devices, AD598 Datasheet - Page 12
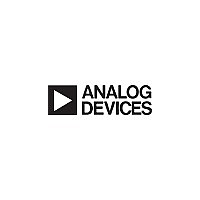
AD598
Manufacturer Part Number
AD598
Description
LVDT Signal Conditioner
Manufacturer
Analog Devices
Datasheet
1.AD598.pdf
(16 pages)
Available stocks
Company
Part Number
Manufacturer
Quantity
Price
Part Number:
AD598AD
Manufacturer:
ADI/亚德诺
Quantity:
20 000
Part Number:
AD598JRZ
Manufacturer:
ADI/亚德诺
Quantity:
20 000
Company:
Part Number:
AD598SD883B
Manufacturer:
ADI
Quantity:
743
AD598
The V/F converter is currently set up for unipolar operation.
The AD652 data sheet explains how to set up for bipolar opera-
tion. Note that when the LVDT core is centered, the output fre-
quency is zero. When the LVDT core is positioned off center,
and to one side, the frequency increases to a full-scale value.
To introduce bipolar operation to this circuit, an offset must be
introduced at the LVDT as shown in Step 10 of the design
procedures.
LOW COST SET-POINT CONTROLLER
A low cost set-point controller can be implemented with the cir-
cuit shown in Figure 23. Such a circuit could possibly be used
in automobile fuel control systems. The potentiometer, P1, is
attached to the gas pedal, and the LVDT is attached to the but-
terfly valve of the fuel injection system or carburetor. The posi-
tion of the butterfly valve is electronically controlled by the
position of the gas pedal, without mechanical linkage.
This circuit is a simple two IC closed loop servo-controller. It is
simple because the LVDT circuit is functioning as the loop inte-
grator. By putting a capacitor in the feedback path (normally oc-
cupied by R2), the output signal from the AD598 corresponds
to the time integral of the position being measured by the
LVDT. The LVDT position signal is summed with the offset
signal introduced by the potentiometer, P1. Since this sum is in-
tegrated, it must be forced to zero. Thus the LVDT position is
forced to follow the value of the input potentiometer, P1. The
output signal from the AD598 drives the LM675 power ampli-
fier, which in turn drives the solenoid.
This circuit has dual advantages of being both low cost and high
accuracy. The high accuracy results from avoiding the offset er-
rors normally associated with converting the LVDT signal to a
voltage and then subsequently integrating that voltage.
MECHANICAL FOLLOWER SERVO-LOOP
Figure 24 shows how two Schaevitz E100 LVDTs may be com-
bined with two AD598s in a mechanical follower servo-loop
configuration. One of the LVDTs provides the mechanical input
position signal, while the other LVDT mimics the motion.
The signal from the input position circuit is fed to the output as
a current so that voltage offset errors are avoided. This current
OUTPUT
POSITION
SCHAEVITZ E 100
LVDT
INPUT
MECHANICAL
POSITION
0.015 F
0.1 F
10
2
3
4
5
6
7
8
9
1
Figure 23. Low Cost Set-Point Controller
LEV 2
–V
EXC 1
EXC 2
LEV 1
FREQ 1
FREQ 2
B1 FILT
B2 FILT
V
B
S
AD598
0.1 F
FEEDBACK
OFFSET 2
OFFSET 1
OUT FILT
SIG OUT
SIG REF
A1 FILT
A2 FILT
+V
V
A
S
19
18
16
14
13
12
20
17
15
11
–12–
+ V
signal is summed with the signal from the output position
LVDT; this summed signal is integrated such that the output
position is now equal to the input position. This circuit is an
efficient means of implementing a mechanical servo-loop since
only three ICs are required.
This circuit is similar to the previous circuit (Figure 23) with
one exception: the previous circuit uses a potentiometer instead
of an LVDT to provide the input position signal. Replacing the
potentiometer with an LVDT offers two advantages. First, the
increased reliability and robustness of the LVDT can be ex-
ploited in applications where the position input sensor is located
in a hostile environment. Second, the mechanical motions of the
input and output LVDTs are guaranteed to be identical to
within the matching of their individual scale factors. These
particular advantages make this circuit ideal for application as a
hydraulic actuator controller.
DIFFERENTIAL GAGING
LVDTs are commonly used in gaging systems. Two LVDTs
can be used to measure the thickness or taper of an object. To
measure thickness, the LVDTs are placed on either side of the
object to be measured. The LVDTs are positioned such that
there is a known maximum distance between them in the fully
retracted position.
This circuit is both simple and inexpensive. It has the advantage
that two LVDTs may be driven from one AD598, but the disad-
vantage is that the scale factor of each LVDT may not match
exactly. This causes the workpiece thickness measurement to
vary depending upon its absolute position in the differential
gage head.
This circuit was designed to produce a 10 V signal output
swing, composed of the sum of the two independent 5 V
swings from each LVDT. The output voltage swing is set with
an 80.9 k resistor. The output voltage V
given by:
0.33 F
0.1 F
INPUT PI
50k
MASS ON SPRING
V
1 F
OUT
33 GRAMS
0.01 F
620 N/m
30k
(V
(V
A
A
–V
100
0.068 F
10k
V
49.9k
B
B
)
)
IN4740A
0.33 F
(V
(V
10V
C
C
4.99k
–V
+ V
V
POWER SUPPLY
20k
D
D
1000pF
LM675
150k
)
)
+ V
OUT
500 A R2.
47 F
47 F
0.1 F
for this circuit is
GUARDIAN SOLENOID
12 VDC 2–INT–12D
62 CONE
33 F
+ 25V
GND
REV. A