SCA21X0 VTI [VTI technologies], SCA21X0 Datasheet - Page 8
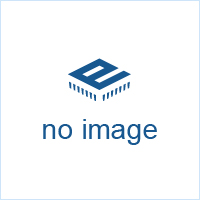
SCA21X0
Manufacturer Part Number
SCA21X0
Description
VTI Automotive Digital Accelerometer Platform
Manufacturer
VTI [VTI technologies]
Datasheet
1.SCA21X0.pdf
(35 pages)
2
2.1 Measurement mode
2.2 Temperature output
2.3 Self-diagnostic functions
2.3.1
2.3.2
2.3.2.1
2.3.2.2
2.3.2.2.1
2.3.2.2.2
VTI Technologies Oy
www.vti.fi
Operation Modes
Memory self-diagnostic
Signal path self-diagnostic
SCA8X0 – single axis accelerometers
SCA21X0 and SCA31X0 – multi axis accelerometers
Start-up Self Test (STS)
Continuous Self Test (STC)
After the startup the acceleration data is immediately available through the SPI registers. There is
no need to initialize the accelerometer before starting to use of it. If the application is requiring
monitoring of the correctness of the operation there are several options available to monitor the
operation status.
The devices include a temperature measurement function. Temperature data can be read through
the SPI interface. Temperature measurement is not calibrated for absolute accuracy. If absolute
accuracy is needed, it can be achieved through measuring the temperature value in two
temperature points in final application and storing them as a calibration value and calculating the
absolute temperature value by using the two points.
VTI Automotive Digital Accelerometer Platform has a set of built-in self-diagnostic functions to
support the application fail safety. The diagnostic functions cover the accelerometer sensing
element functionality, accelerometer internal operation and signal path functionality
Factory calibrated values of the accelerometer are stored in a non-volatile memory. The calibrated
values are read during the device power on into volatile registers that control the operation of the
device. During the startup of the device the calculated sum of non-volatile registers is compared to
the factory calibrated value. The test is done automatically after supplies are set on, after any reset
state of component and after return from power-down mode. Test can also be started by a CTRL-
register command.
Sensor element and signal path is tested by deflecting the proof mass of the sensing element to
both directions over a predefined dynamic range. The test is done automatically during start-up and
it can be repeated by a CTRL-register command. The result of the test is a momentary mass
deflection seen in the output of the device. During the test the accelerometer performs a
comparison of the deflection result to a pre-defined threshold value. When the needed dynamics
have been detected the device will return the result of a passed test in a register. By following the
output of the device on SPI interface it is possible to detect failures through the signal path.
During the application start up or when the accelerometer is affected by the gravity force only it is
possible to detect possible sensing element anomalies by applying a start up self test. The test is
done in a following way: a digitally calculated resultant acceleration of x, y and z-axis is compared
to predefined threshold value. Test is started by CTRL-register command and it is done once when
requested.
During device operation the continuous self test is monitoring the sensing element performance.
Digitally calculated self-diagnostic function is compared to predefined threshold value. Test is
started by CTRL-register command and it is calculated continuously on background until disabled.
Possible errors are indicated in an error status register and in SPI frame.
Doc. Nr. 82 694 00 C
SCA8X0/21X0/3100 Series
8/35