UDQ2916B-T ALLEGRO [Allegro MicroSystems], UDQ2916B-T Datasheet - Page 7
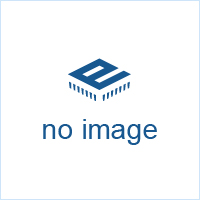
UDQ2916B-T
Manufacturer Part Number
UDQ2916B-T
Description
DUAL FULL-BRIDGE PWM MOTOR DRIVER
Manufacturer
ALLEGRO [Allegro MicroSystems]
Datasheet
1.UDQ2916B-T.pdf
(10 pages)
APPLICATION NOTES
Current Sensing
To minimize current sensing inaccuracies caused by ground
trace IR drops, each current-sensing resistor should have a
separate return to the ground terminal of the device. For low-
value sense resistors, the IR drops in the PCB can be significant
and should be taken into account. The use of sockets should be
avoided as their contact resistance can cause variations in the
effective value of R S .
Generally, larger values of R S reduce the aforementioned effects
but can result in excessive heating and power loss in the sense
resistor. The selected value of R S should not cause the absolute
maximum voltage rating of 1.5 V, for the SENSE terminal, to be
exceeded. The recommended value of R S is in the range of:
If desired, the reference input voltage can be filtered by placing
a capacitor from REFIN to ground. The ground return for this
capacitor as well as the bottom of any resistor divider used
should be independent of the high-current power-ground trace to
avoid changes in REFIN due to IR drops.
Thermal Considerations
For reliable operation, it is recommended that the maximum
junction temperature be kept below 110°C to 125°C. The
junction temperature can be measured best by attaching a
thermocouple to the power tab or batwing of the device and
www.allegromicro.com
R
S
= 0.75 / I
TRIP
(max) ± 50% .
measuring the tab temperature, T TAB . The junction temperature
can then be approximated by using the formula:
where V F can be chosen from the electrical specification table
for the given level of I LOAD . The value for R θJT is approximately
6°C/W for both package styles.
The power dissipation of the batwing packages can be improved
20% to 30% by adding a section of printed circuit board copper
(typically 6 to 18 square centimeters) connected to the batwing
terminals of the device.
The thermal performance in applications that run at high load
currents, high duty cycles, or both can be improved by adding
external diodes from each output to ground in parallel with the
internal diodes. Fast-recovery ( ≤200 ns) diodes should be used
to minimize switching losses.
Load Supply Terminal
The load supply terminal, VBB, should be decoupled with an
electrolytic capacitor ( ≥47µF is recommended), placed as close
to the device as is physically practical. To minimize the effect of
system ground IR drops on the logic and reference input signals,
the system ground should have a low-resistance return to the
load supply voltage.
Fixed Off-Time Selection
With increasing values of t OFF , switching losses decrease, low-
level load current regulation improves, EMI reduces, PWM
frequency decreases, and ripple current increases. The value of
t OFF can be chosen for optimization of these parameters. For
applications where audible noise is a concern, typical values of
t OFF should be chosen in the range of 15 to 35 µs.
T
J
= T
TAB
DUAL FULL-BRIDGE
+ (2 × I
MOTOR DRIVER
LOAD
× V
F
× R
θJT
) ,
2916
7