LM3430_07 NSC [National Semiconductor], LM3430_07 Datasheet - Page 13
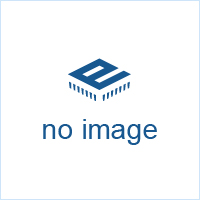
LM3430_07
Manufacturer Part Number
LM3430_07
Description
LED Backlighting Solution with LM3430 and LM3432
Manufacturer
NSC [National Semiconductor]
Datasheet
1.LM3430_07.pdf
(16 pages)
Design Hints
The schematic of the demonstration board is shown in page
2. Some hints on selection of the key parameters and com-
ponents will be described in below. For full details of the
design equations and theories, please refer to the LM3430
and LM3432 datasheets.
BOOST CONVERTER DESIGN WITH LM3430
The function of the boost converter is to step up the input
voltage to a higher LED rail voltage to drive strings of twelve
LEDs connected in series.
Determination of the Worst Case LED Rail Voltage, V
The diode forward voltage, V
to 4.0V that varies from vendor to vendor. Considering only
the worst case situation, i.e. V
nected in series, a minimum of 48V is required to put the LED
strings in proper operation. On the top of this voltage, addi-
tional control headroom for the constant current regulators is
needed. The suggested start up LED rail voltage is 50V and
this is also the ceiling of the boost converter output voltage,
i.e. in case the load is disconnected, the boost converter out-
put will stay at this voltage, no risk of over-voltage need to be
considered. Once the demonstration board is in operation, the
LM3432 will communicate with the LM3430 to lower the LED
rail voltage to an appropriate level. This feature makes the
LM3430 with LM3432 a robust and efficient LED driver solu-
tion.
Selecting the Switching Frequency, F
The selection of switching frequency is a trade off between
size, cost and efficiency. In general, a lower switching fre-
quency requires larger and more expansive external compo-
nents. For some of the applications, space is one of the key
considerations. A higher switching frequency can fulfill the
space requirement, however the switching losses will go up
and the overall system efficiency will be lowered. In this
demonstration board, a switching frequency of 1MHz was se-
lected.
Selection of the Power MOSFET
The power MOSFET plays a key role in system efficiency. An
ideal power MOSFET should be low gate capacitance, C
low gate charge, Q
Drain-Source breakdown voltage, V
the required V
drop, typically its about 0.5~0.7V. The average load current
with all LED strings fully ON is 120 mA, by quick estimation;
the worst case peak switch current is about 0.9A. The tiny
MOSFET selected can operate up to 60V and 2A with R
(ON)
Selecting the Boost Schottky Diode
The boost Schottky diode current equals to the average load
current. The forward voltage drop and reverse recovery time
determines the power loss with this component. The lower the
= 125 mΩ, Q
DS(BD)
g
g
= 4.8 nC and C
, low ON resistance, R
is 50V plus the Schottky diode voltage
F
of HB-WLED ranges from 3.5V
F
= 4.0V, for twelve LEDs con-
iss
DS(BD)
= 240 pF.
SW
DS(ON)
. In this application,
and sufficient
LED
iss
DS
,
13
forward voltage drop and faster reverse recovery time always
results in better performance. The Schottky diode must also
be rated to handle the maximum output voltage plus any ring-
ing at the switching node caused by the diode parasitic ca-
pacitance and lead inductance.
Selection of Power Inductor
In fixed switching frequency boost converter applications, the
inductance is determined by the allowable peak-to-peak in-
ductor ripple current, Δi
the switching frequency. The duty cycle, D is evaluated first
at both V
ductor current is calculated at both voltages respectively. With
the maximum average inductor current, the allowable induc-
tor ripple current is determined. Finally, the inductance value
can be calculated and an off-the-shelf inductance value clos-
est to the calculated value must be selected. The calculation
only gives the inductance required but not the size of the in-
ductor, the inductor selected must be capable to handle the
maximum peak inductor current without saturating the induc-
tor even at high temperature. The maximum peak inductor
current is equal to the maximum average inductor current plus
one half of the maximum allowable inductor ripple current,
Δi
Selection of Output Capacitor
The output capacitor in a boost converter supplies current to
the load during the MOSFET on-time and filters the AC com-
ponents of the load current during the off-time. The selection
of this capacitor determines the steady state output voltage
ripple, ΔV
prised of three components. The first part of the ripple voltage
is the surge current created during the boost diode turns on.
The second part is due to the charging and discharging of the
output capacitor through the boost diode and the final part is
caused by the flow of inductor current through the output
capacitor's Equivalent Series Resistance, ESR. Both part 1
and part 3 are related to ESR, in case low ESR ceramic ca-
pacitors are used, the contribution of these two parts be-
comes insignificant. The output voltage ripple can be
estimated by the equation in below.
Where I
the converter switching frequency.
From the equation in above, the relationships between differ-
ent parameters are obvious. A higher output capacitance can
reduce the output voltage ripple; however this can slow down
the power-up time and the system transient respond. The
choice of the output capacitor depends mainly on the appli-
cation specifications. For most of the cases, multiple itera-
tions are required to come up with an appropriate value.
L(p-p)
.
OUT
IN(MIN)
OUT
is the load current, D is the duty ratio and F
. The magnitude of this voltage ripple is com-
and V
IN(MAX)
L(p-p)
of the maximum load current and
. Then the full load average in-
www.national.com
SW
is