LM621N NSC [National Semiconductor], LM621N Datasheet - Page 5
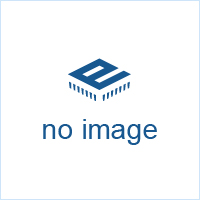
LM621N
Manufacturer Part Number
LM621N
Description
LM621 Brushless Motor Commutator
Manufacturer
NSC [National Semiconductor]
Datasheet
1.LM621N.pdf
(12 pages)
Available stocks
Company
Part Number
Manufacturer
Quantity
Price
Company:
Part Number:
LM621N
Manufacturer:
HITACHI
Quantity:
6 263
Functional Description
The commutation decoder receives Hall-sensor inputs HS1
HS2 and HS3 and a 30 60 SELECT input This block de-
codes the gray-code sequence to the required motor-drive
sequence
The dead-time generator monitors the DIRECTION input
and inhibits the outputs (pins 11 thru 16) for a time sufficient
to prevent current-spiking in the external power switches
when the direction is reversed
The six chip outputs drive external power switching devices
which drive the motor Three outputs source current the
remaining three sink current The output transistors provide
up to 50 mA outputs for driving devices or up to 40V output
swings for driving MOSFETs The LM621 logic is powered
from 5V
The undervoltage lockout section monitors the V
and if the voltage is not sufficient to permit reliable logic
operation the outputs are shutdown
Three-Phase Motor Commutation
There are two popular conventions for establishing the rela-
tive phasing of rotor-position signals for three-phase mo-
tors While usually referred to as 30-degree and 60-degree
sensor placements this terminology refers to mechanical
degrees of sensor placement not electrical degrees The
electrical angular resolution is the required 60 degrees in
both cases The phasing differences can be noted by com-
paring the sequences of HS1 through HS3 entries in Table I
FIGURE 1 Commutation Waveforms for 60-degree Phasing
CC
supply
5
Figure 1 shows the waveforms associated with the commu-
LM621 Commutation Decoder Truth Table which shows
both the 30- and 60-degree phasings (and the 90-degree
phasing for four-phase motors) and their required decoder
logic truth tables respectively Table I shows the phasing
(or codes) of the Hall-effect sensors for each 60-degree
(electrical) position range of the rotor and correlates these
data to the commutator sink and source outputs required to
drive the power switches These phasings are common to
several motor manufacturers The 60-degree phasing is pre-
ferred to 30-degree phasing because the all-zeros and all-
ones codes are not generated The 60-degree phasing is
more failsafe because the all-zeros and all-ones codes
could be inadvertently generated by things like disconnect-
ed or shorted sensors
Because the above terminology is not used consistently
among all motor manufacturers Table II Alternative Sen-
sor-phasing Names will hopefully clarify some of the differ-
ences Table II shows a different 60-degree phasing and
120- 240- and 300-degree phasings Comparison with Ta-
ble I will show that these four phasings are essentially shift-
ed and or reversed-order versions of those used with the
LM621
tation decoder logic for a motor which has 60-degree rotor-
position phasing along with the generated motor-drive
waveforms As can be seen in the drawing Hall-effect sen-
sor signals HS1 through HS3 are separated by 60 electrical
degrees which is the required angular resolution for three-
phase motors
TL H 8679– 6