AD815-EB Analog Devices, AD815-EB Datasheet - Page 11
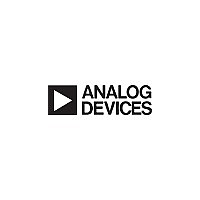
AD815-EB
Manufacturer Part Number
AD815-EB
Description
High Output Current Differential Driver
Manufacturer
Analog Devices
Datasheet
1.AD815-EB.pdf
(16 pages)
REV. B
DC ERRORS AND NOISE
There are three major noise and offset terms to consider in
a current feedback amplifier. For offset errors refer to the
equation below. For noise error the terms are root-sum-squared
to give a net output error. In the circuit below (Figure 42), they
are input offset (V
the noise gain of the circuit (1 + R
current (I
inverting input current, which when divided between R
and subsequently multiplied by the noise gain always appear at
the output as I
less than 2 nV/ Hz. At low gains though, the inverting input
current noise times R
layout and device matching contribute to better offset and
drift specifications for the AD815 compared to many other
current feedback amplifiers. The typical performance curves
in conjunction with the equations below can be used to predict
the performance of the AD815 in any application.
POWER CONSIDERATIONS
The 500 mA drive capability of the AD815 enables it to drive
a 50
driver. This implies a power dissipation, P
To ensure reliability, the junction temperature of the AD815
should be maintained at less than 175 C. For this reason,
the AD815 will require some form of heat sinking in most
applications. The thermal diagram of Figure 43 gives the
basic relationship between junction temperature (T
various components of
V
Figure 43. A Breakdown of Various Package Thermal
Resistances
OUT
T
J
load at 40 V p-p when it is configured as a differential
BN
T
V
P
IN
A
T
WHERE:
IO
A
Figure 42. Output Offset Voltage
P
T
T
R
BI
IN
A
J
JC
CA
N
= JUNCTION TEMPERATURE
P
= AMBIENT TEMPERATURE
= DEVICE DISSIPATION
) also multiplied by the noise gain, and the
T
= THERMAL RESISTANCE – JUNCTION TO CASE
IN
= THERMAL RESISTANCE – CASE TO AMBIENT
IO
R
R
1
R
J
T
N
G
J
) which appears at the output multiplied by
F
. The input voltage noise of the AD815 is
CASE
F
R
R
J
A
G
is the dominant noise source. Careful
F
JC
I
I
BN
BI
JA
.
JA
I
BN
R
F
A
F
+
/R
B
R
CA
B
N
G
(DIE MOUNT
TO CASE)
A
), noninverting input
=
(JUNCTION TO
DIE MOUNT)
JC
1
IN
T
A
, of nearly 5 watts.
R
R
V
OUT
G
F
Equation 1
I
J
) and
BI
F
and R
R
F
G
–11–
Figure 44 gives the relationship between output voltage swing
into various loads and the power dissipated by the AD815 (P
This data is given for both sine wave and square wave (worst
case) conditions. It should be noted that these graphs are for
mostly resistive (phase < 10 ) loads. When the power dissipation
requirements are known, Equation 1 and the graph on Figure 45
can be used to choose an appropriate heat sinking configuration.
Figure 44. Total Power Dissipation vs. Differential Output
Voltage
Normally, the AD815 will be soldered directly to a copper pad.
Figure 45 plots
to copper pads on both sides of G10 epoxy glass board connected
together with a grid of feedthroughs on 5 mm centers.
This data shows that loads of 100 ohms or less will usually not
require any more than this. This is a feature of the AD815’s
15-lead power SIP package.
An important component of
package to heatsink. The data given is for a direct soldered
connection of package to copper pad. The use of heatsink
grease either with or without an insulating washer will increase
this number. Several options now exist for dry thermal connec-
tions. These are available from Bergquist as part # SP600-90.
Consult with the manufacturer of these products for details of
their application.
Figure 45. Power Package Thermal Resistance vs. Heat
Sink Area
35
30
25
20
15
10
4
3
2
1
0
COPPER HEAT SINK AREA (TOP AND BOTTOM) – mm
f = 1kHz
JA
SQUARE WAVE
0.5k
against size of copper pad. This data pertains
10
AD815AVR, AY
1k
V
20
OUT
JA
is the thermal resistance of the
– Volts p-p
SINE WAVE
1.5k
30
JC
R
= 2 C/W)
R
R
L
L
L
= 200
= 100
= 50
2k
40
AD815
2
2.5k
IN
).