FLS3217 FAIRCHILD [Fairchild Semiconductor], FLS3217 Datasheet - Page 9
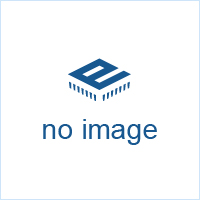
FLS3217
Manufacturer Part Number
FLS3217
Description
Single-Stage PFC Primary-Side-Regulation Offline LED Driver with Integrated Power MOSFET
Manufacturer
FAIRCHILD [Fairchild Semiconductor]
Datasheet
1.FLS3217.pdf
(14 pages)
© 2012 Fairchild Semiconductor Corporation
FLS3217 / FLS3247 • Rev. 1.0.0
Functional Description
FLS3217 / FLS3247 is an AC-DC PWM controller for
LED lighting applications. TRUECURRENT
regulate accurate LED current independent of input
voltage, output voltage, and magnetizing inductance
variations. The linear frequency control in the oscillator
reduces conduction loss and maintains DCM operation
in the wide range of output voltage, which implements
high power factor correction in a single-stage flyback
topology. A variety of protections, such as short/open-
LED protection, over-temperature protection, and cycle-
by-cycle current limitation stabilize system operation
and protect external components.
Startup
Powering at startup is slow due to the low feedback-loop
bandwidth in the PFC converter. To increase power
during startup, the internal oscillator counts 12ms to
define Startup Mode. During Startup Mode, turn-on time
is determined by current-mode control with 0.2V voltage
limit. Transconductance becomes 14 times bigger, as
shown in Figure 15. After Startup Mode, turn-on time is
controlled by Voltage Mode, using the COMI voltage. The
error amplifier transconductance is reduced to 85µmho.
Constant Current Regulation
The output current can be estimated using the peak
drain current and inductor current discharge time
because output current is same as the average of the
diode current in steady state. The peak value of the
drain current is determined by the CS pin and the
inductor discharge time (t
By using three pieces of information (peak drain current,
inductor discharging time, and operating switching
period); the TRUECURRENT block calculates estimates
the output current. The output of the TRUECURRENT
calculation is compared with an internal precise
reference to generate an error voltage, V
determines the turn-on time in Voltage-Mode control.
With Fairchild’s innovative technique, constant current
output can be precisely controlled.
V
0.2V
COMI
V
I
LED
V
CS
IN
Figure 15. Startup Sequence
14gm gm
V
DD
= V
Startup Mode: 12ms
DD_ON
DIS
) is sensed by t
®
DIS
COMI
techniques
Time
detector.
, which
Power-Factor Controller (PFC) and Total
Harmonic Distortion (THD)
In a conventional boost converter, Boundary Conduction
Mode (BCM) is generally used to keep input current in
phase with input voltage for Power Factor (PF) and
Total Harmonic Distortion (THD). In flyback / buck boost
topology, constant turn-on time and constant frequency I
Discontinuous Conduction Mode (DCM) can implement
high PF and low THD as shown in Figure 16. Constant
turn-on time is maintained by the internal error amplifier
and a large external capacitor (typically over 1µF) at the
COMI pin. Constant frequency and DCM operation is
managed by linear frequency control.
Linear Frequency Control
DCM should be guaranteed for high power factor in
flyback topology. To maintain DCM in the wide range of
output voltage, frequency is linearly changed by output
voltage in linear frequency control. Output voltage is
detected by auxiliary winding and a resistive divider
connected to the VS pin, as shown in Figure 17.
When the output voltage decreases, the secondary
diode conduction time is increased and the linear
frequency control lengthens the switching period. This
maintains DCM operation in the wide output voltage
range, as shown in Figure 18. The frequency control
also lowers primary rms current with better power
efficiency in full-load condition.
GATE
9
I
Figure 16. Input Current and Switching
IN
Figure 17. Linear Frequency Control
Constant Frequency
www.fairchildsemi.com
I
IN_AVG