ACPM-7886-BLK AVAGO [AVAGO TECHNOLOGIES LIMITED], ACPM-7886-BLK Datasheet - Page 8
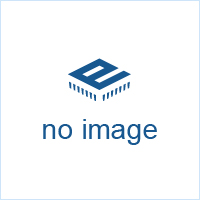
ACPM-7886-BLK
Manufacturer Part Number
ACPM-7886-BLK
Description
TD-SCDMA Power Amplifier
Manufacturer
AVAGO [AVAGO TECHNOLOGIES LIMITED]
Datasheet
1.ACPM-7886-BLK.pdf
(14 pages)
Suggested Board Implementation
Notes:
1. All decoupling capacitors should be placed as close to the power module as possible.
2. RFin (Pin 2) has a grounded inductor inside package as a matching element. An external series capacitor is needed if a DC voltage is
3. An additional battery bypass capacitor should be placed on bias line before the battery terminal, but does not need to be immediately
4. Trace impedance on RF lines should be 50Ω.
200
150
100
8
Solder Reflow Profile
The most commonly used solder reflow method is
accomplished in a belt furnace using convection heat
transfer. This profile is designed to ensure reliable
finished joints. However, the profile indicated will vary
among different solder pastes from different
manufacturers and is shown here for reference only.
Other factors that can affect the profile include the
density and types of components on the board, type
of solder used and type of board or substrate material
being used. The profile shows the actual temperature
that should occur on the surface of a test board at or
near the central of the solder joint. For this type of
reflow soldering, the circuit board and solder joints
are first to get heated up. The components on the
250
50
present.
adjacent to the PA module. The bypass capacitor should be a large value, nominally between 2.2uF and 4.7uF.
0
Ramp 1
C2 (4700pF)
C1 (4700pF)
Suggested Lead Free Reflow Profile For SnAgCu Solder Paste
50
Preheat
Peak = 250 ± 5˚C
100
Ramp 2
Seconds
150
Reflow
GND
C5 (10,000pF)
200
Melting point = 218˚C
Cooling
250
C4 (33pF)
C3 (33pF)
board are then heated by conduction. The circuit
board, because it has a large surface area, absorbs
thermal energy efficiently and distributes this heat to
the components.
Reflow temperature profiles designed for tin/lead alloys
will need to be revised accordingly to cater for the
melting point of the lead free solder being 34°C (54°F)
higher than that of tin/lead eutectic or near-eutectic
alloys. In addition, the surface tension of molten lead
free solder alloys is significantly higher than the surface
tension for tin/lead alloys and this can reduce the
spread of lead free solder during reflow.
Lead Free Reflow Profile General Guidelines
i. Ramp 1
Ramp to 100°C. Maximum slope for this zone is limited
to 2°C/sec. Faster heating with ramp higher than 2°C
may result in excessive solder balling and slump.
ii. Preheat
Preheat setting should range from 100 to 150°C over a
period of 60 to 120 seconds depending on the
characteristics of the PCB components and the thermal
characteristics of the oven. If possible, do not prolong
preheat as it will cause excessive oxidation to occur to
the solder powder surface.