MDC3105LT1G ON Semiconductor, MDC3105LT1G Datasheet - Page 8
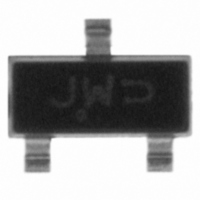
MDC3105LT1G
Manufacturer Part Number
MDC3105LT1G
Description
IC RELAY/DRVR INDUCT LOAD SOT23
Manufacturer
ON Semiconductor
Type
Relay/Load Driverr
Specifications of MDC3105LT1G
Input Type
Non-Inverting
Number Of Outputs
1
Current - Output / Channel
400mA
Current - Peak Output
500mA
Voltage - Supply
6V
Operating Temperature
-40°C ~ 85°C
Mounting Type
Surface Mount
Package / Case
SOT-23-3, TO-236-3, Micro3™, SSD3, SST3
Supply Voltage Max
6V
No. Of Outputs
1
Output Current
400mA
Driver Case Style
SOT-23
Device Type
Relay
Filter Terminals
SMD
No. Of Pins
3
Rohs Compliant
Yes
Leaded Process Compatible
Yes
Lead Free Status / RoHS Status
Lead free / RoHS Compliant
On-state Resistance
-
Lead Free Status / Rohs Status
Lead free / RoHS Compliant
Other names
MDC3105LT1GOS
MDC3105LT1GOS
MDC3105LT1GOSTR
MDC3105LT1GOS
MDC3105LT1GOSTR
Available stocks
Company
Part Number
Manufacturer
Quantity
Price
Company:
Part Number:
MDC3105LT1G
Manufacturer:
ON Semiconductor
Quantity:
127 439
Company:
Part Number:
MDC3105LT1G
Manufacturer:
ON Semiconductor
Quantity:
2 500
Part Number:
MDC3105LT1G
Manufacturer:
ON/安森美
Quantity:
20 000
allows one to increase a device’s peak power dissipation
rating above the average rating by dividing by the duty cycle
of the repetitive pulse train. Thus, a continuous rating of 200
mW of dissipation is increased to 1.0 W peak for a 20% duty
cycle pulse train. However, this only holds true for pulse
widths which are short compared to the thermal time
constant of the semiconductor device to which they are
applied.
thermal time constant of the device, the peak operating
condition begins to look more like a continuous duty
operating condition over the time duration of the pulse. In
these cases, the peak power dissipation rating cannot be
merely time averaged by dividing the continuous power
rating by the duty cycle of the pulse train. Instead, the
average power rating can only be scaled up a reduced
amount in accordance with the device’s transient thermal
response, so that the device’s max junction temperature is
not exceeded.
thermal resistance, r(t) as a function of pulse width in ms for
various pulse train duty cycles as well as for a single pulse
and illustrates this effect. For short pulse widths near the left
side of the chart, r(t), the factor, by which the continuous
duty thermal resistance is multiplied to determine how much
the peak power rating can be increased above the average
power rating, approaches the duty cycle of the pulse train,
which is the expected value. However, as the pulse width is
increased, that factor eventually approaches 1.0 for all duty
cycles indicating that the pulse width is sufficiently long to
appear as a continuous duty condition to this device. For the
MDC3105LT1, this pulse width is about 100 seconds. At
this and larger pulse widths, the peak power dissipation
capability is the same as the continuous duty power
capability.
a specific application, enter the chart with the worst case
pulse condition, that is the max pulse width and max duty
cycle and determine the worst case r(t) for your application.
Then calculate the peak power dissipation allowed by using
the equation,
yields r(t) = 0.3 and when entered in the above equation, the
max allowable Pd(pk) = 390 mW for a max T
For a repetitive pulse operating condition, time averaging
For pulse widths which are significant compared to the
Figure 12 of the MDC3105 data sheet plots its transient
To use Figure 12 to determine the peak power rating for
Thus for a 20% duty cycle and a PW = 40 ms, Figure 12
Using TTR Designing for Pulsed Operation
Pd(pk) = (150°C − T
Pd(pk) = (T
Jmax
− T
Amax
Amax
) ÷ (556°C/W * r(t))
) ÷ (R
qJA
* r(t))
A
= 85°C.
http://onsemi.com
8
pulse shape for which the rise and fall times are insignificant
compared to the pulse width. If this is not the case in a
specific application, then the V
be multiplied together and the resulting power waveform
integrated to find the total dissipation across the device. This
then would be the number that has to be less than or equal
to the Pd(pk) calculated above. A circuit simulator having a
waveform calculator may prove very useful for this purpose.
MDC3105. Device instantaneous operation should never be
pushed beyond these limits. It shows the SOA for the
Transistor “ON” condition as well as the SOA for the Zener
during the turn−off transient. The max current is limited by
the Izpk capability of the Zener as well as the transistor in
addition to the max input current through the resistor. It
should not be exceeded at any temperature. The BJT power
dissipation limits are shown for various pulse widths and
duty cycles at an ambient temperature of 25°C. The voltage
limit is the max V
the input to the device is switched off, the BJT “ON” current
is instantaneously dumped into the Zener diode where it
begins its exponential decay. The Zener clamp voltage is a
function of that BJT current level as can be seen by the
bowing of the V
addition to the Zener’s current limit impacting this device’s
500 mA max rating, the clamping diode also has a peak
energy limit as well. This energy limit was measured using
a rectangular pulse and then translated to an exponential
equivalent using the 2:1 relationship between the L/R time
constant of an exponential pulse and the pulse width of a
rectangular pulse having equal energy content. These L/R
time constant limits in ms appear along the V
curve for the various values of I
intersect the V
load should not exceed these limits at their respective
currents. Precise L/R limits on Zener energy at intermediate
current levels can be obtained from Figure 11.
Also note that these calculations assume a rectangular
Figure 10 is the Safe Operating Area (SOA) for the
Notes on SOA and Time Constant Limitations
CC
Z
CC
versus I
limit. The L/R time constant for a given
that can be applied to the device. When
Z
curve at the higher currents. In
O
and I
Z
at which the Pd lines
O
waveforms should
Z
versus I
Z