MAX17020ETJ+T Maxim Integrated Products, MAX17020ETJ+T Datasheet - Page 25
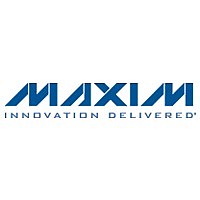
MAX17020ETJ+T
Manufacturer Part Number
MAX17020ETJ+T
Description
IC CTLR PWM DUAL STEP DN 32-TQFN
Manufacturer
Maxim Integrated Products
Series
Quick-PWM™r
Datasheet
1.MAX17020ETJT.pdf
(34 pages)
Specifications of MAX17020ETJ+T
Applications
Power Supplies
Current - Supply
1mA
Voltage - Supply
6 V ~ 24 V
Operating Temperature
-40°C ~ 85°C
Mounting Type
Surface Mount
Package / Case
32-TQFN Exposed Pad
Lead Free Status / RoHS Status
Lead free / RoHS Compliant
logic-level PGOOD_ output voltage, connect an external
pullup resistor between PGOOD_ and V
pullup resistor works well in most applications.
When the output voltage rises 16% above the fixed-reg-
ulation voltage or has risen 200mV above the dynamic
REFIN2 input voltage, the controller immediately pulls
the respective PGOOD_ low, sets the overvoltage fault
latch, and immediately pulls the respective DL_ high—
clamping the output to GND. Toggle either ON1 or ON2
input, or cycle V
clear the fault latch and restart the controller.
When the output voltage drops 30% below the fixed-
regulation voltage or has dropped 300mV below the
dynamic REFIN2 input voltage, the controller immedi-
ately pulls the respective PGOOD_ low, sets the under-
voltage fault latch, and begins the shutdown sequence.
After the output voltage drops below 0.1V, the synchro-
nous rectifier turns on, clamping the output to GND.
Toggle either ON1 or ON2 input, or cycle V
below its POR threshold to clear the fault latch and
restart the controller.
The MAX17020 features a thermal-fault protection circuit.
When the junction temperature rises above +160°C, a
thermal sensor activates the fault latch, pulls PGOOD1
and PGOOD2 low, enables the 10Ω discharge circuit,
and disables the controller—DH and DL are pulled low.
Toggle ONLDO or cycle IN power to reactivate the con-
troller after the junction temperature cools by 15°C.
Firmly establish the input-voltage range and maximum
load current before choosing a switching frequency and
inductor operating point (ripple-current ratio). The primary
Table 4. Fault Protection and Shutdown Operation Table
Shutdown (ON_ = High to Low);
Output UVP (Latched)
Output OVP (Latched)
V
Thermal Fault (Latched)
V
V
CC
CC
CC
UVLO Falling-Edge
UVLO Rising Edge
POR
MODE
CC
______________________________________________________________________________________
Thermal-Fault Protection (TSHDN)
power below its POR threshold to
Undervoltage Protection (UVP)
Dual Quick-PWM Step-Down Controller
Overvoltage Protection (OVP)
Design Procedure
with Low-Power LDO, RTC Regulator
Voltage soft-shutdown initiated. Internal error-amplifier target
slowly ramped down to GND and output actively discharged
(automatically enters forced-PWM mode).
Controller shuts down and EA target internally slewed down.
Controller remains off until ON_ toggled or V
SMPS controller disabled (assuming ON_ pulled high), 10
output discharge active.
SMPS controller enabled (assuming ON_ pulled high).
SMPS inactive, 10
DD
. A 100kΩ
CC
CONTROLLER STATE
output discharge active.
power
design trade-off lies in choosing a good switching fre-
quency and inductor operating point, and the following
four factors dictate the rest of the design:
•
•
•
•
Input Voltage Range: The maximum value
(V
AC-adapter voltage. The minimum value (V
must account for the lowest battery voltage after
drops due to connectors, fuses, and battery-selector
switches. If there is a choice at all, lower input volt-
ages result in better efficiency.
Maximum Load Current: There are two values to
consider. The peak load current (I
mines the instantaneous component stresses and fil-
tering requirements and thus drives output capacitor
selection, inductor saturation rating, and the design of
the current-limit circuit. The continuous load current
(I
ves the selection of input capacitors, MOSFETs, and
other critical heat-contributing components.
Switching Frequency: This choice determines the
basic trade-off between size and efficiency. The opti-
mal frequency is largely a function of maximum input
voltage due to MOSFET switching losses that are
proportional to frequency and V
quency is also a moving target due to rapid improve-
ments in MOSFET technology that are making higher
frequencies more practical.
Inductor Operating Point: This choice provides
trade-offs between size vs. efficiency and transient
response vs. output ripple. Low inductor values pro-
vide better transient response and smaller physical
size, but also result in lower efficiency and higher
output ripple due to increased ripple currents. The
minimum practical inductor value is one that causes
the circuit to operate at the edge of critical conduc-
tion (where the inductor current just touches zero
with every cycle at maximum load). Inductor values
LOAD
IN(MAX)
CC
) determines the thermal stresses and thus dri-
power cycled.
) must accommodate the worst-case, high
DL driven high and DH pulled
low after soft-shutdown
completed (output < 0.1V).
DL immediately driven high,
DH pulled low.
DL and DH pulled low.
DL driven high, DH pulled low.
DL driven high, DH pulled low.
DRIVER STATE
IN
2
. The optimum fre-
LOAD(MAX)
IN(MIN)
) deter-
25
)